Achieving quality oil-free air for these applications is vital to help ensure product quality and safety, but there are different methods to achieving this.

Learning Objectives
- Explore the air quality classes and what the different levels and classifications mean.
- The differences between oil flooded and oil free rotary screw air compressors including the benefits of each.
- The types of air treatment and the role each plays in air purity.
Compressed air insights
- An oil-free compressor can help improve a company’s operation and is a valuable tool if air purity is important for the manufacturing process.
- There are several different types of compressors and some work better than others, depending on the operation and the importance of air quality.
Compressed air purity is critical for many operations — particularly sensitive applications such as food and beverage, pharmaceutical, semiconductor manufacturing and more. Delivering quality, oil-free air for these applications is vital to help ensure product quality and safety in some cases.
There are many ways an operation can attain oil-free air, but the process is not as straightforward as it seems. In a typical rotary screw compressed air system, oil is present in the air leaving the compressor, and will come in contact with the end product unless steps are taken to treat the air; or an oil-free rotary screw compressor is used. The type of air compressor, the filters used and even the ambient air the compressor is pulling from impacts the quality of compressed air produced.
To complicate matters, air quality is classified according to the level of contaminants in the air; from Class 0 to Class 1-2-1 to Class 1-3-2, etc. There is a lot to unpack when it comes to air and air quality; the following will break down the different air classes as well as examine the important differences between oil-flooded and oil-free rotary screw air compressors. We will also examine the types of air treatment — and their role in air purity.
Air quality classes
Air quality is broken down into seven primary classes of three contaminant types: solids, humidity and liquid water and oil. Solid particulates (like dust or pipe scale) can be removed by filters. Humidity and liquid water can be removed by compressed air dryers. Oil (liquid and vapor) can be removed by coalescing oil removal filters and activated carbon (charcoal) oil vapor adsorbing filters.
The International Organization for Standardization (ISO) 8573-1:2010 Air Quality Classes outlines the contaminants allowed by class. Depending on the application, Class 1 air – sometimes called “technically oil-free” may be appropriate, but also may require additional downstream filtration.
For applications where air purity is essential, Class 0 air has the most stringent requirements for each type of contaminant – solid particles; water/moisture; and oil and oil vapor.
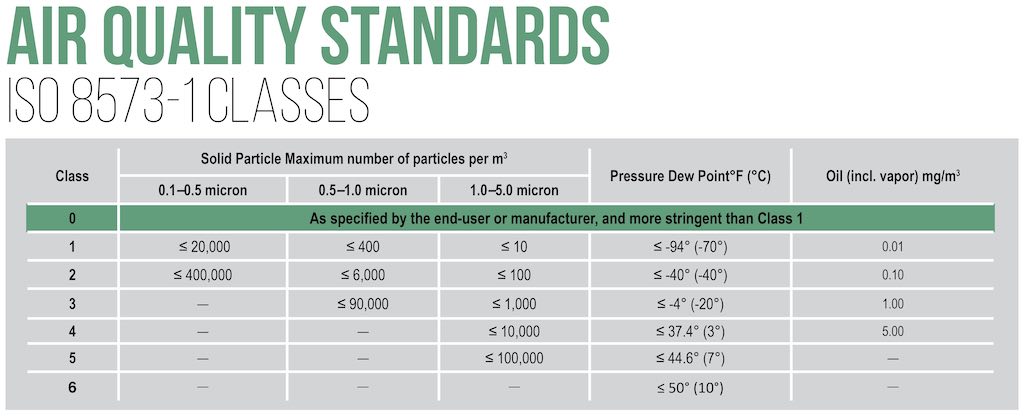
ISO8573-1:2010 measures contaminants in three categories:
-
Solid particles: Measures the solid particles contained in the compressed air stream. Within this column are three sub-columns indicating the quantity of allowable particles by micron size. The bigger the particle, the fewer parts per million allowed.
-
Pressure dew point: Measures the maximum allowable water content in the compressed air stream.
-
Oil (including vapor): Measures the maximum allowable oil content in the compressed air stream.
Class 0 air is more stringent than Class 1 and essentially, the lower the class, the lower the concentration of compressed air contaminants. For applications requiring oil-free air, Class 0 air is a less risky solution than Class 1 because it doesn’t require inline filtration — which may fail and requires regular monitoring — to remove oil contamination which may be coming from the compressor.
Class 0 air is commonly produced utilizing an oil-free compressor which does not introduce any lubricant into the compression chamber that can then enter the compressed air stream.
The difference between oil-free and oil-flooded air compressors
The simple difference between oil-free and oil-flooded rotary screw air compressors is the introduction and use of oil in the air compression chamber. In an oil-flooded rotary screw compressor, lubricant is used to coat and seal the rotors to help with temperature and lubrication. As the input air moves through the compressor, it mixes with the oil in the chamber. While most of the injected lubricant is separated from the airstream after compression, residual oil is still present. Removing additional oil requires a downstream filter.
However, oil-free rotary screw air compressors do not utilize oil in the compression chamber thanks to a special coating on the rotors and therefore no oil comes in contact with the air as it is compressed. Further air purity may be obtained by downstream filtration to remove any contaminants in the intake ambient air.
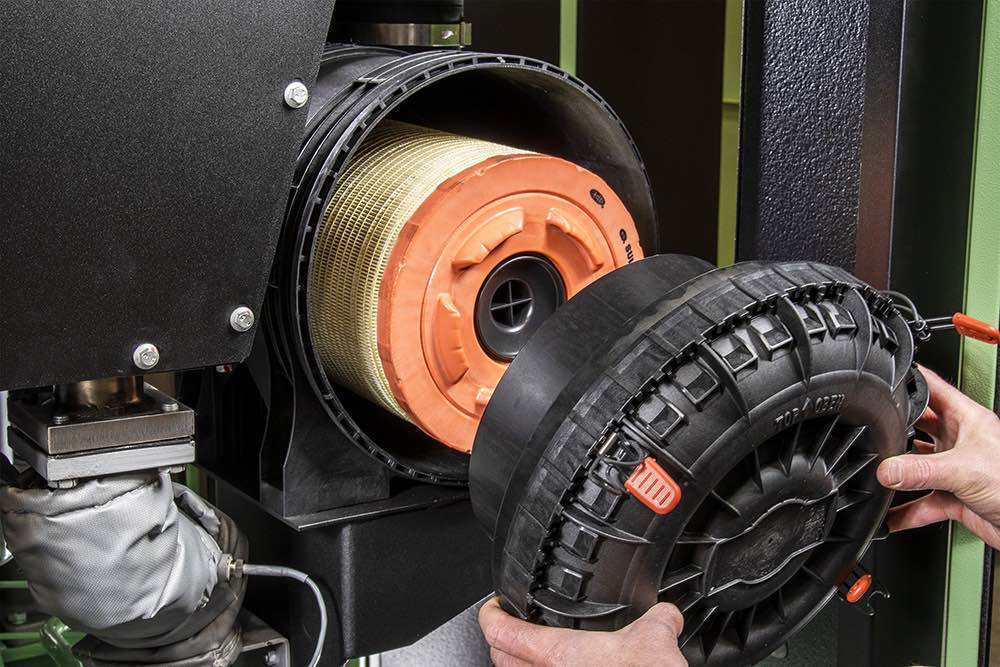
Recognize just because an oil-free compressor doesn’t introduce lubricant into the compressor chamber doesn’t mean oil can’t be introduced from the outside air. If the ambient air feeding the compressor contains oil vapor from other machinery, etc., the air leaving the compressor may be contaminated. Think, garbage in, garbage out. To help maintain air purity when using an oil-free compressor, particular attention should be paid to the intake air. The cleaner the intake air, the less chance of contaminants downstream which can affect production. To meet even more stringent air quality needs, air treatment (filtration; mist elimination) may still be necessary to eliminate other contaminants.
Why doesn’t everyone choose an oil-free compressor? For some applications, air purity is not a priority and oil-free compressors often come with a higher upfront cost. It all comes down to the application and the quality of air needed. The peace of mind of knowing downstream applications are less likely to be contaminated is often worth the added up front expense.
Air treatment in oil-free compressors
Once the compressed air leaves the compressor, there are more opportunities for it to be treated before leaving the compressed air system and entering the greater manufacturing process. The major categories of air treatment in a compressed air system are 1) dryers – most commonly refrigerated and desiccant – more on those below – and 2) downstream filtration and mist eliminators. There are dozens of different options and assortments to help remove contaminants from compressed air.
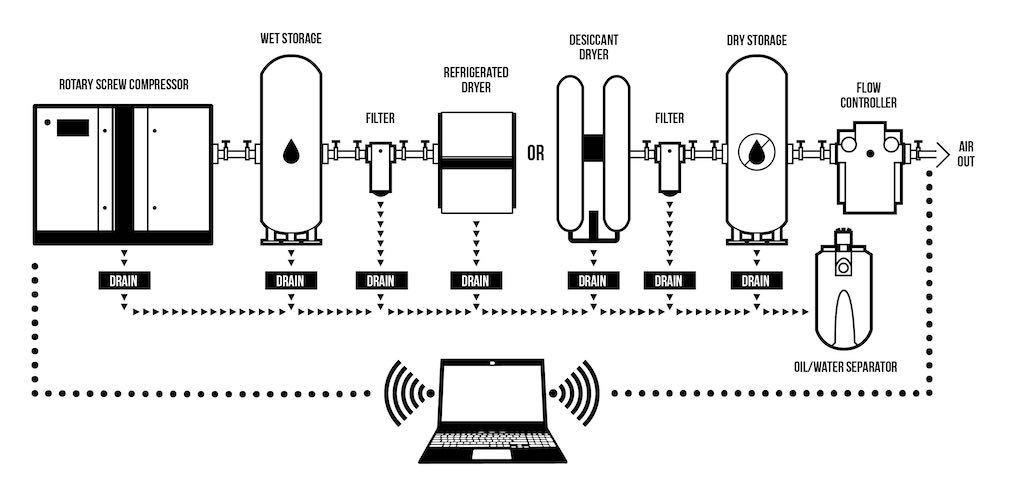
For an industrial compressed air system, removal of moisture from the compressed air stream is a vital task. Dry compressed air* helps keep air-powered tools, equipment, and instruments running well. It can also help prolong the life of both tools and piping by reducing the rate of corrosion caused by excess moisture. In sensitive applications, where the air contacts the final product, or in some cases even its packaging, it is critical the compressed air be the proper quality, including the dew point of the air.
Refrigerated air dryers as their name implies, remove moisture from the compressed air stream mechanically by cooling it. Cool air can’t hold as much water vapor as warm air, so as the air cools excess water vapor condenses out as liquid water which is then removed from the system.
Desiccant dryers remove moisture from the compressed air stream chemically by passing the air over a bed of desiccant. The desiccant adsorbs the water vapor, meaning the water vapor clings to thousands of tiny pores in each bead of the desiccant. Once the desiccant bed becomes saturated, either very low dew point compressed air or heated purge air is used to dry the desiccant. Desiccant dryers often have drying beds arranged in pairs. So while one desiccant bed is drying the air, the other desiccant bed is being dried, allowing for continuous drying of the compressed air stream.
Air purity benefits in manufacturing
If air purity is important for the manufacturing process, an oil-free compressor can help improve a company’s operation, profitability and peace of mind by reducing risks. However, users shouldn’t forget to maintain air treatment and ensure the oil-free compressor is pulling quality ambient air.
*The term “dry” when associated with compressed air is relative to the needs of the process. Compressed air considered clean and dry enough to operate machine tooling is not considered dry enough for a powder coating process.