Don't forget the demand side of your audit when assessing your compressed air system
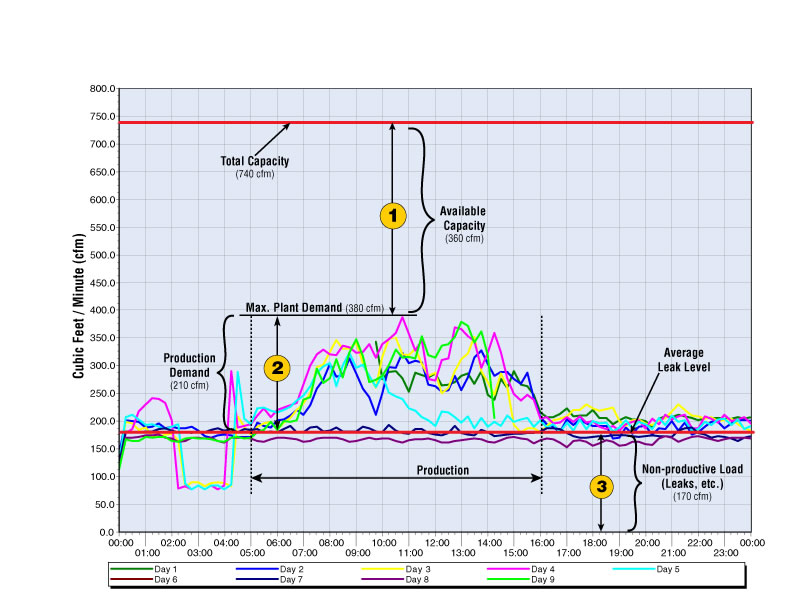
Though still a small minority, more and more industrial plants are taking the initiative to conduct compressed air audits to collect and analyze data that show how their systems are operating with an eye to how they could more reliably deliver stable air pressure, use less energy, and in many cases, both.
Generally, most compressed audits collect data on the “supply side” of the air system (e.g. when compressors are running, main header pressure, etc.). They may collect pressure data from further downstream that can indicate “demand side” issues, but they usually don’t directly assess them.
Supply side audits are very helpful in making adjustments to compressor sizing and controls to meet current or projected demand, but they assume that the demands are productive. The reality is that much more air is produced than is needed. Artificial demand (unnecessary high pressure), inappropriate uses, and leaks are the culprits.
Leaks are in effect just another user of compressed air. Ideally, plant operators would review all compressed air uses and reduce or eliminate inappropriate uses before conducting audits that influence changes to the compressed air supply. But the reality is that often it’s the audit that first alerts the user of significant leakage. The following chart from an actual compressed air audit showed that this plant was losing 170 cfm to leaks—this accounted for 45% of their total 380 cfm demand.
Air audits and leak detection go hand-in-hand. The best preventive maintenance programs capitalize on this relationship and make it truly cyclical:
Both approaches make sense. If you know for a fact that you have a high leak load, then don’t start with an audit. Fix the leaks first.
Dealing with artificial demand and inappropriate uses can be complex if it requires in-depth process analysis. Leaks, on the other hand, are much more straight-forward.
Leak detection should be part of a preventive maintenance program but rarely is. We often remind customers that leaks are very wasteful, yet customers are for whatever reason reluctant to fix them. Be the exception—don’t ignore them and hope they’ll go away. Fixing the leaks will immediately add money to the bottom line.
To sum up: evaluate and reduce as much of your demand as possible before evaluating and changing supply side equipment or settings. Look for ways to eliminate unneeded high pressure and air wasting applications. But even if these are not feasible, finding and fixing leaks is the low hanging fruit.
Michael Camber is the Marketing Services Manager for Kaeser Compressors, Inc. For more information, visit www.us.kaeser.com.