When using Industry 4.0, a positive return on investment (ROI) should always be front of mind for manufacturers. Three questions for considering potential ROI are highlighted.
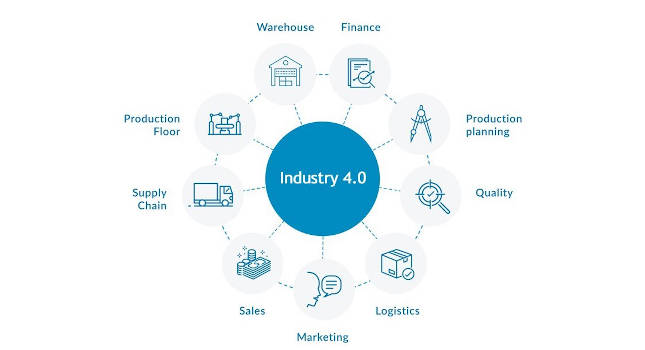
Learning Objectives
- Industry 4.0 implementation should have a positive return on investment (ROI) when it is implemented.
- Manufacturers should track key performance indicators (KPIs) and target areas where they can improve most.
- Good Industry 4.0 implementation should translate to positive results for employees.
Return on investment (ROI) is a hot topic for mid-sized manufacturers interested in investing in operational improvements on the factory floor. Regardless of if the team involved plans on investing $1 or $100,000 in digital transformation, that expenditure should positively impact profit. Recently, factory floor investments for mid-sized manufacturers have circled around an even hotter topic: Industry 4.0. The ourth industrial revolution uses the adoption of computers and sensors on the factory floor to capture valuable statistics that can be used to increase profit and efficiency.
The ROI for Industry 4.0 can seem less tangible to manufacturers since improvements rely on better usage of data. Industry 4.0 relies on modern smart technology to acquire data that can be turned into actionable intelligence instead of simply adding a new piece of automation. Ultimately, if data is not being measured accurately, it cannot be improved.
When considering your potential ROI for Industry 4.0 implementation, companies should ask three questions:
1. What are my key performance indicators (KPIs)?
The four areas where mid-sized manufacturers will see a return on investment from Industry 4.0 implementation are product quality, machine availability, efficiency (measures such as cycle time and labor) and energy consumption. By closely tracking KPIs before, during and after implementation, manufacturers can demonstrate proven ROI.
KPIs also can highlight areas that would benefit from smart technology to improve performance. However, if the implementation has no payback for the bottom line, there could still be qualitative benefits for the organization. Industry 4.0 also provides better data in a timelier manner, which can benefit more than just profits.
2. What are my biggest production pain points?
Manufacturers want to know the best strategies for implementing Industry 4.0 to increase efficiency. The secret is targeting areas on the factory floor where inefficiencies and loss costs could hinder profit margins. Industry 4.0 can be taken on in bite-sized pieces; not everything needs to be changed at once.
By targeting the biggest pain points on the factory floor, mid-sized manufacturers can use actionable data to improve performance while demonstrating ROI for the smart manufacturing costs. Short periods of change such as 90- to 120-day increments should be used and measured on these pain points for manufacturers to move incrementally toward digital transformation without breaking the bank.
3. What does Industry 4.0 mean for employees?
The latest U.S. Bureau of Labor Statistics report showed a marked decrease in new hires in the manufacturing sector since May 2020 and many manufacturing floors are struggling with employee retention. Implementing Industry 4.0 means employees will not have to capture data points with pencil and paper, which improves data accuracy. An improvement in data accuracy brings consistent product quality and less complaints brought to the production floor. Efficiency and the right technology are important to everyone, especially the operators of manufacturing equipment since it affects daily workflow.
In the end, big investments should show big results. When implementing Industry 4.0, mid-sized manufacturers should track KPIs, target weak areas, and improve employee’s experience to demonstrate a proven ROI. By not implementing the technology for Industry 4.0, mid-sized manufacturers risk incurring a cost of inaction (COI) which is the cost of lost opportunity. Historical habits on factory floors also can affect the bottom line. Just because a process has always been performed a certain way does not mean there is not a more efficient way to perform the task. Inaction may feel safer, but it does not build a stronger factory floor.
Terri Ghio, president, FactoryEye. Edited by Chris Vavra, web content manager, Control Engineering, CFE Media and Technology, [email protected].
MORE ANSWERS
Keywords: Return on investment (ROI), Industry 4.0
CONSIDER THIS
What KPIs are most important for your company during an Industry 4.0 implementation?