By employing preliminary, predictive and preventive maintenance, and air compressor’s performance will be maximized
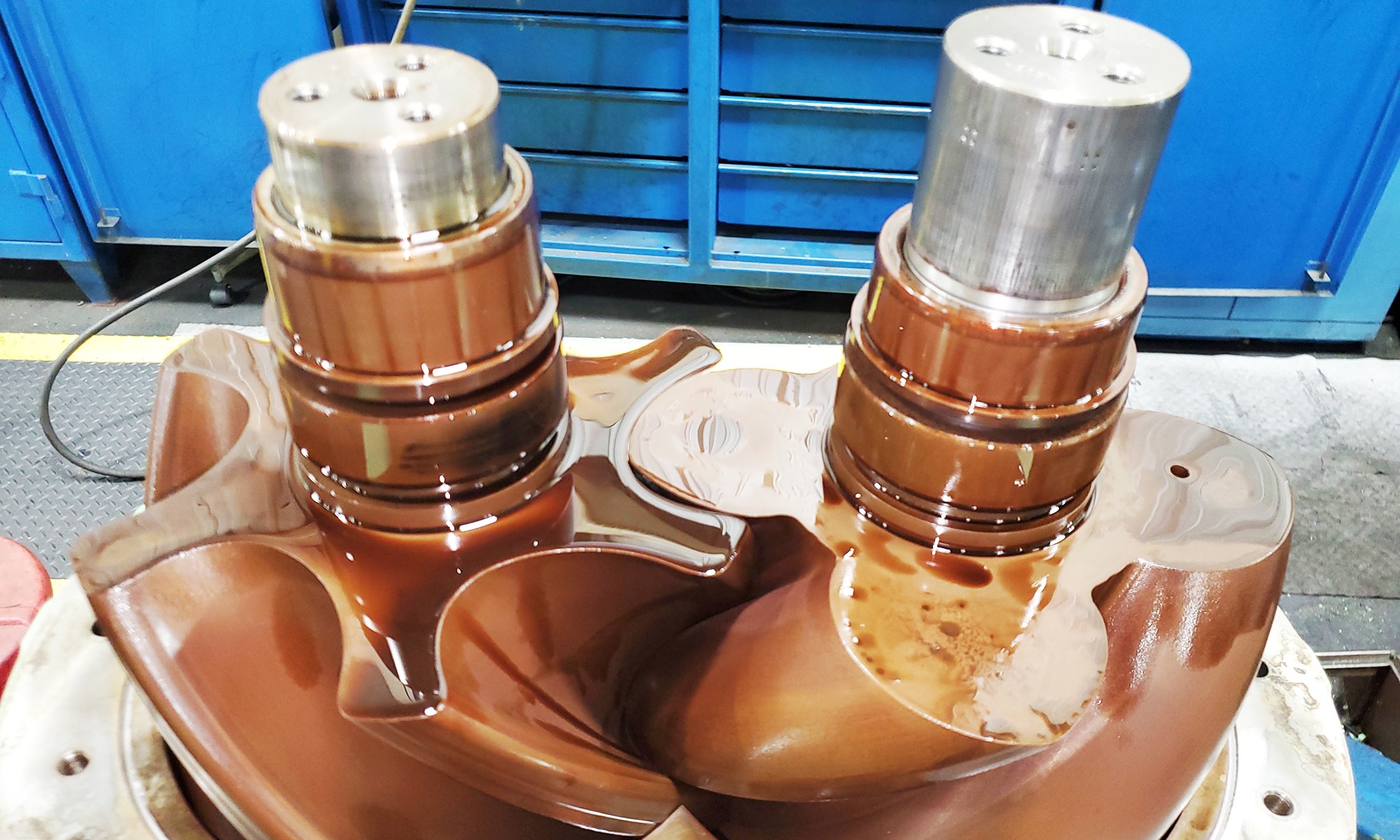
Learning Objectives
- Understand the importance of comprehensive air compressor maintenance. Learn how preliminary, predictive and preventive maintenance contribute to the reliability, efficiency and longevity of a rotary screw compressed air system.
- Identify key factors for compressor installation and maintenance. Understand how proper sizing, environmental conditions and strategic placement of a compressor impact its performance and maintenance requirements.
- Review typical maintenance steps. Gain knowledge of the tools and techniques like fluid sampling and regular system checks to prevent issues and ensure optimal air compressor performance.
Maintenance insights
- To ensure your rotary screw air compressor operates smoothly and efficiently, it’s important to focus on three key types of maintenance: Preliminary (before installation), predictive (monitoring performance trends) and preventive (regular upkeep).
- Proper sizing, optimal location and consistent checks on vibration, fluid and key components will extend the compressor’s lifespan and reduce downtime.
- By following a comprehensive maintenance plan, you can prevent costly repairs and keep your compressor running at peak performance.
A rotary screw compressed air system is essential to a business’s smooth operation. Proper, consistent maintenance ensures it runs reliably and efficiently, minimizing downtime, reducing repair costs and extending the compressor’s lifespan.
To achieve this, focus on the “three Ps” of air compressor care:
- Preliminary maintenance, or the steps one can take before installation.
- Predictive maintenance, which provides a picture of how the compressor’s peak performance.
- Preventive maintenance, which includes the routine, ongoing review and upkeep of the compressor.
Together, these steps prevent problems and address issues before they escalate.
Maintenance begins before installation
While it might seem counterintuitive, a top-flight maintenance program begins long before the compressor comes through the door. Choosing the right machine and determining its ideal location will impact a compressor’s performance.
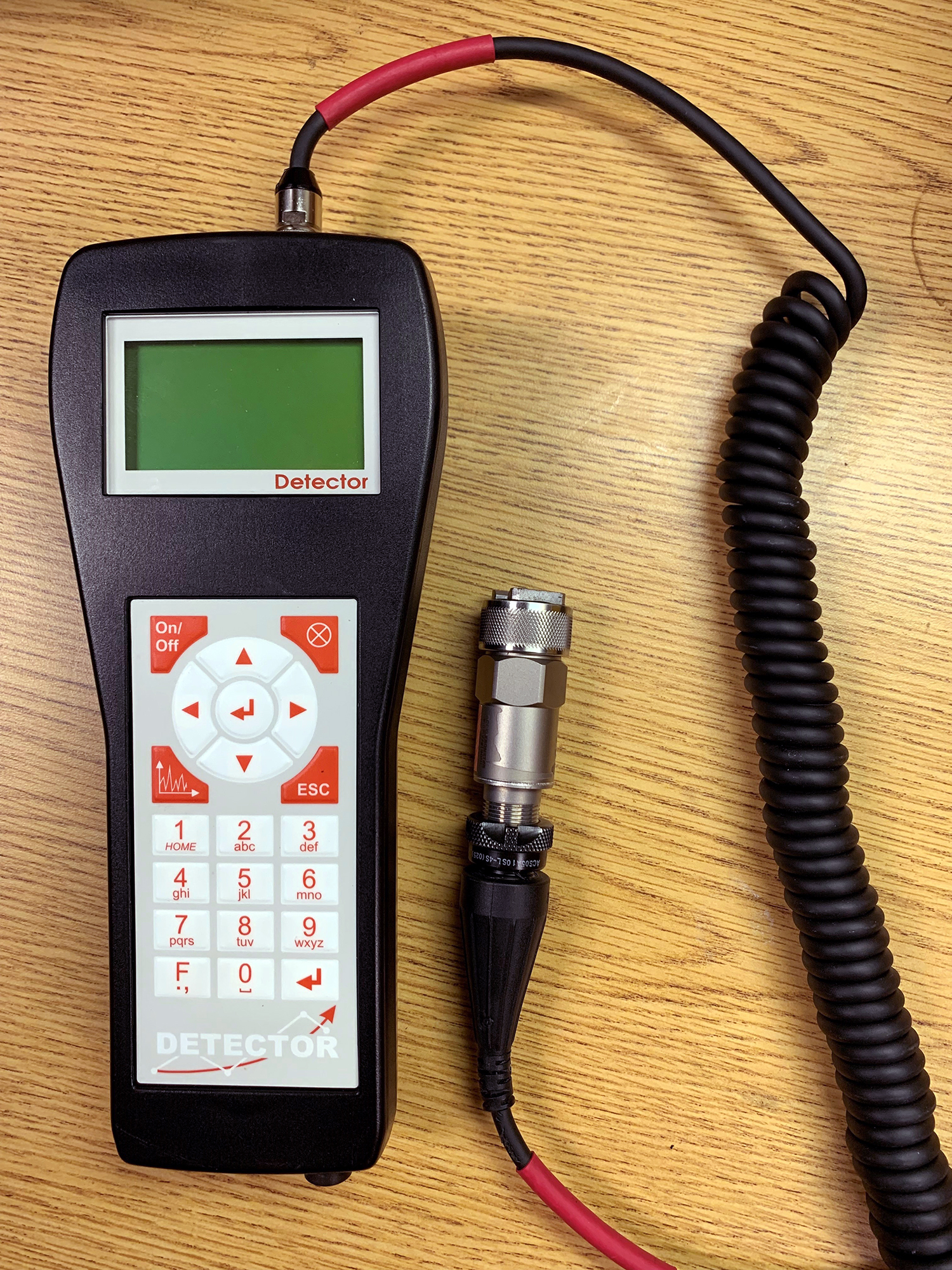
Size is a critical first step; simply put, users need to select the right compressor for the job. An undersized compressor can overtax the machine and shorten its lifespan. Similarly, a compressor too large for the operation — even if accounting for future growth — may be less efficient. An air audit by a certified professional can help you determine the correct capacity for the operation.
Location also matters. The operating environment plays a critical role in compressor maintenance. Do you operate in the scorching southwestern deserts or are you located in the often-frigid northern states? Is a facility sited in an arid climate or one where rain or snowfall are measured in feet, not inches? Does the facility generate significant dust and particulates, such as found in paper mills, or do you operate a pristine pharmaceutical operation?
All these location factors will play a role in maintenance processes and schedule. As you can guess, the dirtier the environment, the more frequent service calls need to be and the more vigilant you need to be tracking filter and cooler cleanliness.
Predictive maintenance: staying ahead of problems
Once a compressor is installed, predictive maintenance becomes key. This involves establishing a baseline for the compressor’s fluid and vibration profiles.
Vibration analysis tests and tracks a compressor’s optimum vibrations. Every compressor has a unique vibration signature and identifying that signature when first installed provides a baseline for the life of the compressor. Over time, if excessive vibration or other deviations from the machine’s normal profile are detected, potential problems which can shorten the lifespan of the compressor may be brewing.
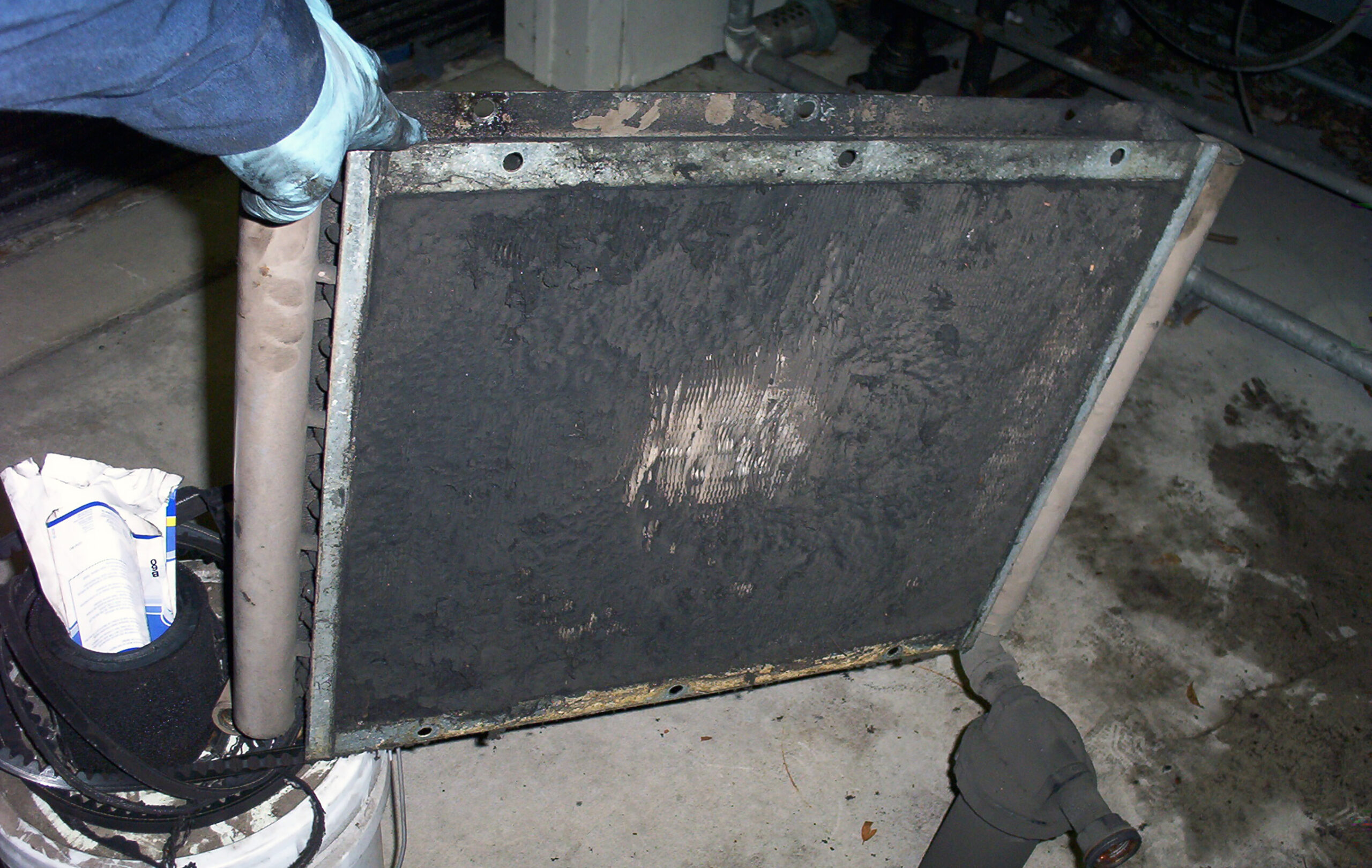
Higher vibrations, for example, can be traced to failing bearings or gears or a decaying rolling element.. Higher vibrations can also be traced to misalignment, motor faults, mechanical looseness or broken motor mounts.
Ideally, a baseline vibration measurement should be recorded within the first few weeks or months of operation. A solid predictive maintenance program should include annual vibration measurements.
Fluid sampling is another predictive tool. Regular sampling of compressor fluid can reveal issues like bearing wear, fluid breakdown and ingestion of contaminates. Again, establishing a baseline soon after installation allows you to spot deviations that might indicate a developing problem.
Preventive maintenance means routine checks
Beyond preliminary and predictive is preventive maintenance. Guidelines for proper preventive maintenance can be found in the air compressor’s manual. Keep in mind the manual is only a guide and proper maintenance depends on unique operating circumstances. Your certified compressor maintenance technician can help set up a program that fits your specific needs.
Key preventive maintenance areas to monitor include:
- Lubricants: Use original equipment manufacturer (OEM)-recommended lubricants to avoid issues like varnishing and overheating.
- Filters: All filter elements have a maximum usable saturation point and eventually need replacing. Over time, contaminants build up on filter elements (including coalescing filters, as some solid particles, however small, are always present). Eventually, this buildup reduces the efficiency of the element. This efficiency loss causes larger pressure drops and allows more contaminants to pass through.
- Coolers: Coolers should be cleaned as often as needed. If the compressor is located outside near pollinating trees or indoors in a dirty, dusty environment, you may need to clean coolers more often to keep efficiency in check.
- Cooling water: In water-cooled compressed air systems, the cooling water needs to be checked at regular intervals and maintained to a certain standard — such as a certain pH and sediment value.
- Condensate system: If a condensate drain fails — which it can do — water can make its way into the downstream process and potentially damage sensitive equipment. Air can also escape through the drain, leading to reduced efficiency.
- Valves and couplings: The minimum pressure check valve (MPCV) should be disassembled and cleaned on a quarterly basis and rebuilt once a year. If the MPCV is not adequately maintained, you can run into all sorts of issues, such as the compressor not starting or unloading properly. Coupling elements should also be inspected regularly (quarterly) and replaced as needed. Couplings can fail and cause excessive vibrations, as well as damaging the pump and motor.
- Motors: Electric motors have bearing greasing requirements spelled out by the manufacturer unless equipped with sealed bearings. Even sealed bearings need to be monitored through routine predictive vibration measurements. Proper greasing can keep contamination out, temperatures down and repairs manageable.

Because the lubricant and filters you use in a compressor are vitally important, careful attention must be paid to them.
Lubricant maintenance
Lubricants have three primary functions in rotary screw air compressors: they coat bearings, seal rotors and reduce or dampen heat. Other important functions include the prevention of varnishing or the formation of crystals that can raise internal compressor temperatures. Heat and varnish are the two primary enemies of rotary screw air compressors and the two are directly related. High temperatures create more varnish, which in turn creates more heat. It can become a vicious cycle.
Use only OEM-recommended lubricants in the system because they are specifically engineered for a machine. There are hundreds of compressor lubricants, dozens of lubricant manufacturers and even more resellers. To begin, start by considering the components of which the lubricant is made. Each lubricant has a primary ingredient, commonly referred to as a base stock. Each of these base stocks has different properties and pros and cons. Components include:
-
Hydrocarbons (mineral oils).
-
Hydrotreated hydrocarbons.
-
Synthetic hydrocarbons (PAO).
-
Polyglycol blends/diesters.
-
Polyglycol/polyol esters (PAG/POE).
Ideally, you should choose a polyglycol lubricant whenever possible. These products are the crème-de-la-crème of compressor lubricants. While they have a higher upfront cost, they are the premier lubricants and come with virtually zero downside.
Air compressors using these lubricants produce biodegradable condensate, reducing a company’s environmental footprint and costs for condensate disposal. Polyglycol lubricants also do not varnish and, in fact, remove existing varnish that may have been built up in the compressor. This helps create a more energy-efficient machine and prolong the compressor’s life.
Air filter maintenance
For compressed air filters, there are three types:
Particulate filters remove particulates from the air stream by trapping contaminants on the media. The filter element design and material determine the size of the particles it can trap, so particulate filters have varying degrees of filtration.
Coalescing filters remove water and aerosols of liquids like oil by coalescence. Coalescence is the process of trapping smaller droplets along the media until they combine into larger drops that fall out of the air flow. The structure and type of media determine how much aerosol can be removed, so they also have varying degrees of filtration.
Some filter designs act as both particulate and coalescing filters. With these designs, one filter with a single element can handle both types of filtration.
Activated carbon filters are used to remove oil and hydrocarbon vapors from compressed air and reduce oil carryover to 0.003 mg/m³. These filters are most typically used where removing taste or odors is critical, e.g., food processing and pharmaceuticals.
Degrees of filtration
The level of contaminants removed can vary widely in compressed air filters. The following is a breakdown of the degrees of filtration:
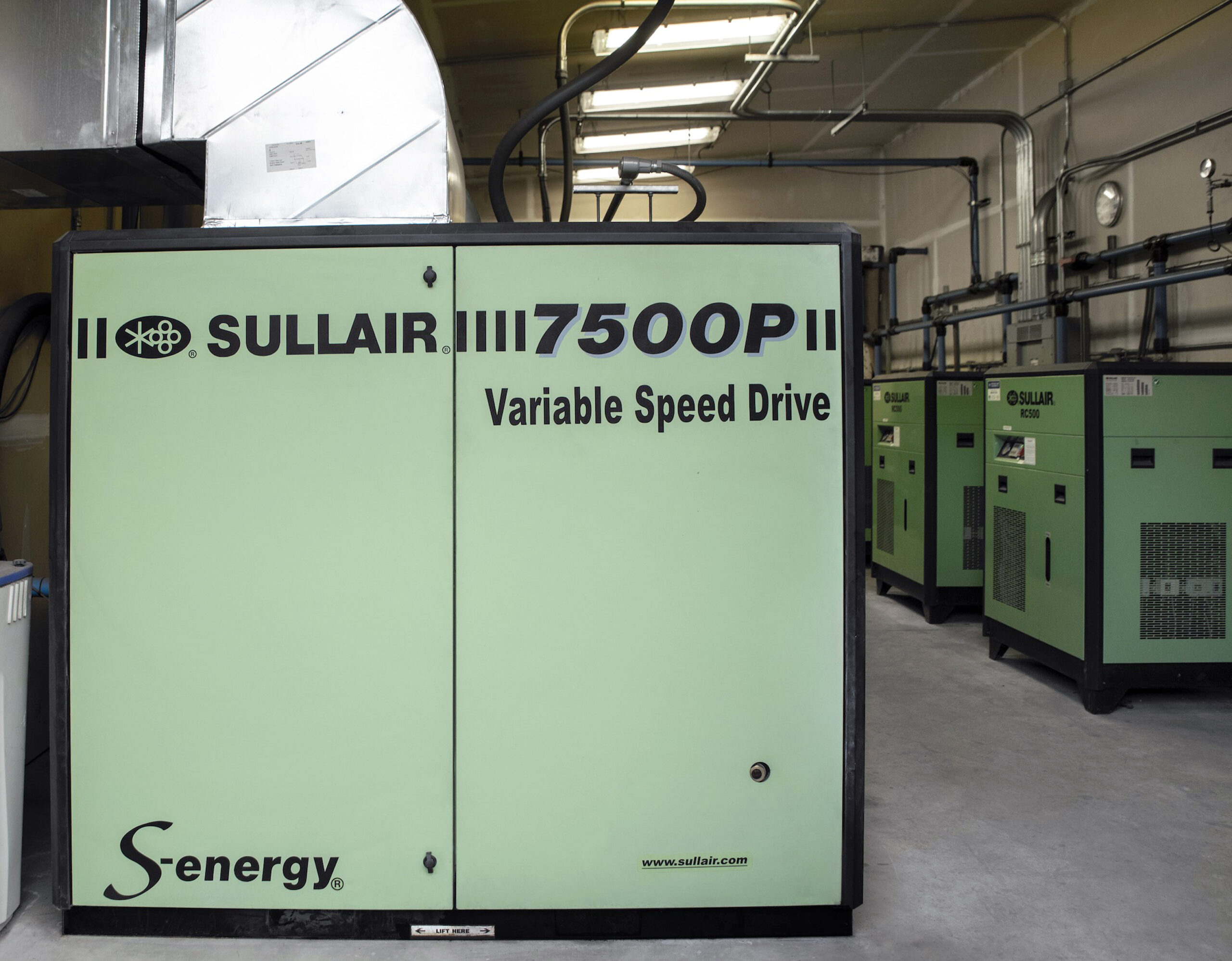
Coarse particulate filters can only remove large particles from the air stream. Depending on filter materials and design, the smallest particles they can remove will be anywhere from 5 to 40 microns.
Coarse coalescing filters can reduce oil carryover to as little as 5 mg/m³. In most cases, coarse filters don’t provide high quality air. However, they can help remove moisture and keep large particles from fouling compressed air tools and instruments (unless those tools or instruments require higher quality air, of course).
Fine filters are typically the minimum size needed where applications or equipment need high quality air. Fine particulate filters can remove particles as small as 1 micron. Fine coalescing filters can limit oil carryover to 0.1 mg/m³. Superfine filters are used when the highest quality air is needed, for example, for food production, pharmaceuticals, spray painting and instrumentation. Superfine (sometimes called micro) particulate filters can remove particles as small as 0.01 micron. Superfine coalescing filters can limit oil carryover to 0.01 mg/m³.
All degrees of filtration can collect larger particles and aerosols than they are optimized for. That might tempt you to just use filters with the highest degree of filtration needed — but you shouldn’t.
When filtering larger contaminants with finer filters, the buildup and loss of efficiency can happen much more quickly. (An active carbon filter could become clogged in hours, for example.) This can lead to unnecessary costs for replacement elements.
Detecting and preventing air leaks
In addition to the preventive maintenance checklist above, identifying and repairing air leaks should be an ongoing focus in any facility. Air leaks can significantly increase energy costs and reduce efficiency. Based on data from the Compressed Air Challenge, 50% of compressed air generated is wasted. Of this wasted 50%, 33% is attributed directly to leaks, with another 8% wasted due to elevating the system pressure to compensate for leaks. As a point of reference, a quarter-inch air line leaking to 100 psi (7 bar), can cost thousands of dollars a year and reduced efficiency.
To find leaks, many manufacturers conduct air audits. Regularly auditing a system for leaks — especially during quieter times when they’re easier to detect is best. The audible frequency range of hearing for the human ear is 20 hertz (Hz) to 17 kHz; ultrasonic sound begins at 20 kHz. The suggested setting of an ultrasonic leak detectors used for compressed air leaks is 40 kHz — higher than what can be heard by the human ear. Many users find that most leaks are small and only located by using an ultrasonic leak detector.
Maintaining the maintenance plan
Finally, maintaining a solid preventive maintenance program requires good record-keeping. Writing detailed logs can help a company stay ahead of potential issues. Consistent logging helps you spot patterns in machine performance and helps you manage the total cost of ownership.
If you are keeping good logs, users can share that information with their service tech to be sure he/she has a full picture of a compressor’s health. Typically, a service tech should be servicing each compressor roughly every quarter for routine maintenance. Also, inspect a compressed air system daily (if possible) to make sure things are running as they should.
As air compressor technology becomes more advanced, the importance of routine inspections and a robust maintenance program — including preliminary, predictive and preventive steps — are essential for keeping the system running at peak performance.