Augmented reality (AR) is changing the way manufacturers work in the field. See three benefits of augmented reality and three examples of how AR helps users.
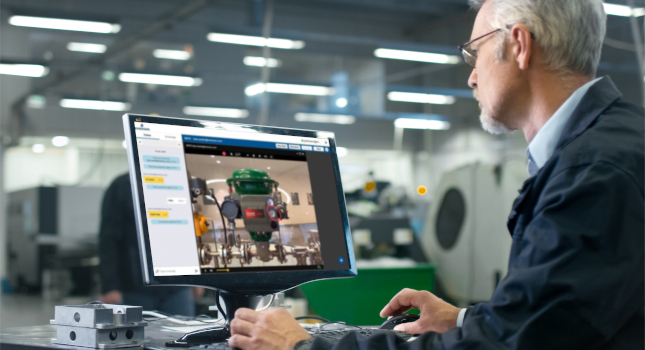
Learning Objectives
- Augmented reality (AR) technology can help younger workers learn skills from older workers in the field.
- For AR to deliver the most value, the technology must be integrated with operations technology (OT) data systems such as an asset performance platform.
- AR technology can reduce costs and safety risks and improve collaboration and training.
As a new generation of technicians begins to step up, plant management can no longer rely on workers’ long-nurtured abilities to detect sights and sounds in the field. Those skills will come with time, but to accomplish continual improvements to safety, productivity and efficiency, organizations need to provide field technicians with tools such as augmented reality (AR) to bridge the gap and accelerate skill development. AR is already moving beyond the buzz and delivering value to organizations. The difference between flashy digital transformation technology and practical value to business is in the strategy.
Prepare a strategy to get the most practical value from AR technology. Adopters should look for AR solutions that integrate with existing plant and operations technology (OT) systems that provide three key benefits: situational awareness, IoT data integration and live remote assistance. Building a strategy around these elements helps organizations implement with ease and achieve fast return on investment (ROI) through practical AR applications to their operations.
Augmented reality delivers situational awareness
Two issues that vex new and incumbent workers in the field are knowing where to find devices and identify the correct assets when they have made it to the right location. Industrial sites can easily have thousands of devices scattered across large areas in the field. Further complicating asset identification, sometimes a facility can have similar devices adjacent to each other, making it possible for an inexperienced technician to disable the wrong device by accident.
AR helps field workers build the situational awareness they need to quickly locate malfunctioning devices to resolve issues. Advanced AR technology includes functionality that helps operations and maintenance personnel visually map elements in the plant so that they can locate, identify and resolve problems.
Navigation tools built into AR help users locate assets. Through their mobile devices, plant personnel can view assets in the field and see overlays that identify assets by name and provide an intuitive health status.
Augmented reality in action: Situational awareness in chemical processing
One chemical manufacturer in North America has a large manufacturing site with numerous facilities – many of them adjacent to one another.
Contracted instrumentation and engineering (I&E) technicians often don’t know the layout of the facility they are working in, so every time they visit, they are chaperoned by a plant employee to make sure they work on the correct equipment.
To reduce the time personnel must spend chaperoning I&E technicians, the organization is implementing AR technology. This allows the I&E technicians to use AR technology to find their way to a landmark such as a command center or a skid unit, and then quickly identify the right assets through an overlay on a mobile device.
Augmented reality delivers relevant IIoT data integration
For AR to deliver the most value to operations, the technology must be integrated with OT data systems such as an asset performance platform. However, manually engineering that integration can be expensive. Organizations should prioritize solutions with native integration that eases implementation. Otherwise, they risk spending more than the technology costs just to implement it.
Integration provides field workers with instant IoT data relevant to a specific asset. Using a mobile device, users can tap the asset to bring up its entire catalog of asset and process data, documentation, and history of previous maintenance.
With immediate access to all relevant asset data, field operators and technicians avoid the need to make multiple trips back and forth to the maintenance staging area. Assets are fixed efficiently, reducing outage lengths and simplifying routine maintenance.
AR tools also help level the playing field for less experienced technicians by ensuring they have all tools needed for fast troubleshooting and maintenance – including history of work on the asset, notorious problems, and notes left by previous technicians.
Augmented reality in action: Data integration in oil and gas
A natural gas organization in Asia has decades of plant knowledge stranded in the brains of an ever-diminishing number of experienced technicians and engineers. The reliability team wants to capture this knowledge to help upskill future generations of workers at the plant.
To build the database necessary to preserve knowledge, the reliability team will capture the methods of experienced personnel in the AR system and tie them to the assets they impact. Newer technicians will have fast access to that knowledge directly from the field. The captured knowledge will serve as a powerful tool in the field as well as a learning platform to help improve the skillset of inexperienced personnel.
AR also gives field technicians immediate access to a knowledge library containing tools they need to perform maintenance. Currently, technicians print manuals and loop diagrams to take to the site. If they arrive and discover they have the wrong materials, they need to go back. With AR, technicians know they always can access the right documentation – loop diagrams, datasheets, manuals, plant diagrams, and more – on the mobile device.
Augmented reality enables, enhances live remote assistance
Even when equipped with the right tools and resources, technicians can run into problems in the field they don’t know how to fix. When an assigned technician can’t figure out what is wrong, they often escalate the issue to more experienced personnel. experienced technicians and engineers are in high demand and waiting for them to travel to site often can cause extended delays.
A more efficient solution is to remove the need for experts to travel to site. AR enables multiple technicians to work together from anywhere to resolve the problem more quickly. Experts can use AR tools to see what the field technician is seeing and share live on-screen annotations, provide voice and text assistance, and link to additional resources. When experts are available faster and have more tools to help fix problems in the field, asset downtime is reduced, leading to fast return on investment for the AR system.
Augmented reality in action: Live remote assistance in oil and gas
At the natural gas facility in Asia, technicians currently use a phone or a chat app to communicate with experts from the field. If a problem occurs late at night, this means waking up the expert on call and having them search the internet for a manual to provide guidance over the phone. In the worst cases, the on-call expert will have to travel to site to help the technician. The organization wanted to improve field work and limit travel with AR but didn’t want to add additional hardware.
With AR, experts can avoid site trips. The experts have remote assistance tools and documentation available in existing mobile devices to point a field technician in the right direction using step-by-step and AR-annotated procedures. An expert also will be able to see what the field technician sees, which makes it easier to provide accurate diagnosis and guidance. Any troubleshooting steps and notes can be saved for future use in the knowledge library.
Augmented reality drives improved performance
AR technology has the potential to increase productivity of field workers while reducing costs, safety risks, and repair times. The right AR toolset can improve collaboration, training, support, and knowledge transfer to help field technicians make the best decisions today, while preparing them to be more effective. AR solutions provide critical infrastructure for those same personnel to pass their own knowledge to future generations for sustainable, successful long-term operations.
Anna Velena, product manager for software interfaces; Vineesh Kapoor, director of Plantweb product management, Emerson. Edited by Chris Vavra, associate editor, Control Engineering, CFE Media and Technology, [email protected].
MORE ANSWERS
Keywords: augmented reality, Industrial Internet of Things, skills gap
ONLINE
Search “augmented reality” at www.controleng.com for additional stories about augmented reality.
CONSIDER THIS
What plant applications would benefit most from augmented reality?