3D printing technology will change the way we make things
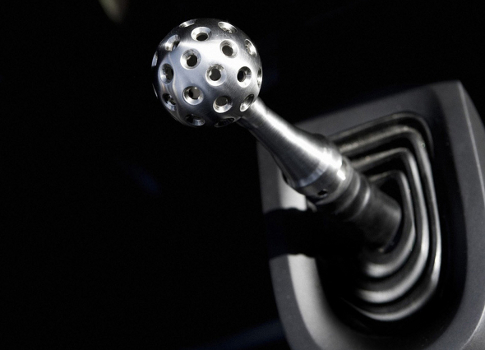
While some in science have searched for the smallest part of our existence, looking for quarks and hadrons and the fundamentals of what holds our world together, others are taking some of the granules of our existence and putting them back together in new shapes.
To call additive manufacturing the transformative technology of the 21st century may be underselling it. It is every bit the fusion of our science fiction dreams with the engineering and technological evolution of how we assemble our lives. To compare it to printing is to compare a black-and-white dot matrix printer to the high-speed color laser printers of today. Yet at its essence, additive manufacturing is printing.
Imagine this: Take a 3D CAD model, run those dimensions through a computer, direct a laser printer filled not with ink but with a powder made of metal or plastic or an alloy—whatever you’d like the finished product to be made of—and start printing.
The powder is passed over the base, over and over again, dozens of times a second, the material fused electronically with lasers, forming an exact replica of the CAD model. It comes out of the 3D printer in its final form. The difference between this model and one cut from a single block of the material is the speed of creation, the limitless form it could take, and the minimized waste.
Now imagine making 20 of those models, all at the same time, all on the same base, all in one pass. Or imagine making 20 similar models, but each customized for the specific application, or personalized for the end user, again all in one pass.
It is the cutting edge of manufacturing, without the cutting. And it’s just getting started.
Putting it all together
It begins with a dot.
If you stare at Georges Seurat’s painting, “A Sunday Afternoon on the Island of Le Grande Jatte” up close, all you see are dots. Step back a little bit, and the whole of the tableau of a riverside afternoon in the 1880s comes into view.
So it is with additive manufacturing. Take a few steps back from the idea that metal powder can flow through a printer nozzle, combined with a laser, and turned into a finished product and see what already can be made with additive manufacturing.
Prosthetic hip joints are being created, each custom-designed for the patient. Wings for the next generation of aircraft can be formed to the same curve, the same tolerance as the CAD drawing that designed them. The tiniest of stents for heart patients can be formed to precise tolerances rather than being laser cut. All can be done when they are needed, on demand.
That idea of “on demand” is crucial to the transformative nature of additive manufacturing. If you have a 3D printer, you suddenly have a warehouse. Need a screw for your assembly line? Instead of going to your parts crib, go to your supplier Website, download the CAD drawing to your 3D printer, and press Print. Need the wrench to tighten down the screw? Same process.
“It will change the way we make things, but it also will change the business of manufacturing,” said Ralph Resnick, interim director of the National Additive Manufacturing Innovation Institute (NAMII). “It has the capability of democratizing manufacturing, creating the possibility of personal manufacturing.”
It also figures to transform the design processes, and the manufacturing capabilities. “Most everything in manufacturing is done at a room temperature environment,” notes Jeff DeGrange, head of the Manufacturing Solutions Group at Minneapolis-based Stratasys, a manufacturer of 3D printing equipment. “So many parts under the hood of a car are in a hot environment. How hot can it get? How cold can it get? What are the strength properties of a material at 40 below zero? These are things we have to understand.”
“People are still trying to wrap their heads around it,” said Andy Snow, regional director of EOS North America. “It’s about educating how to design for process. It’s about understanding that you have the ability to open up a whole new way of manufacturing.”
Understand the potential
To try and understand additive manufacturing is to try and understand the discovery of fire, the wheel, penicillin, or any of the other small miracles of life. If that sounds a little too dramatic, look at what the rest of the world is saying:
From The National Intelligence Council’s report, “Global Trends 2030:Alternative Worlds”: “New manufacturing and automation technologies such as additive manufacturing (3D printing) and robotics have the potential to change work patterns in both the developing and developed worlds. In developed countries these technologies will improve productivity, address labor constraints, and diminish the need for outsourcing, especially if reducing the length of supply chains brings clear benefits.”
The report adds, “By 2030, additive manufacturing could replace some conventional mass-production, particularly for short production runs or where mass customization has high value.”
The Economist, in its November 22, 2012 issue, suggested: “3D printing is just one of many production technologies and trends which are transforming the way companies will be able to make things in the future. The old rules of manufacturing, such as ‘you must seek economies of scale’ and ‘you must reduce unit-labor costs,’ are being cast aside.”
Organizations and associations have rallied to the cause as well. NAMII, one of the early results of President Obama’s 2012 manufacturing initiative that created the National Network for Manufacturing Innovation, is less than a year old. Already it helped create a technology showcase in January at Penn State University, which already has a Center for Innovative Materials Processing through Direct Digital Deposition, or CIMP-3D.
On June 10-13, the Society for Manufacturing Engineers will bring its RAPID additive manufacturing event to Pittsburgh, not far from NAMII’s home base in Youngstown, Ohio.
Perhaps the most compelling example of additive manufacturing’s explosive potential and even more explosive growth is GE Aviation’s Nov. 20, 2012 acquisition of Morris Technologies and its sister company, Rapid Quality Manufacturing.
A Cincinnati-based manufacturer of 3D prototyping and component manufacturing equipment, Morris Technologies already was producing parts for GE Aviation. The acquisition brought that process in-house for GE.
“Morris Technologies and Rapid Quality Manufacturing are parts of our investment in emerging manufacturing technologies," said Colleen Athans, vice president and general manager of the GE Aviation’s supply chain division in a press release. "Our ability to develop state-of-the-art manufacturing processes for emerging materials and complex design geometry is critical to our future.”
The press release went on to state, “With this acquisition, GE Aviation continues to expand its engineering and manufacturing capabilities to meet its growing jet engine production rates over the next five years. In addition to acquiring these manufacturing processes, GE Aviation will open two new production plants in the United States next year.”
This was hardly the start of GE’s efforts. In 2011, GE scientists were studying how to produce a transducer probe for ultrasound equipment. The amount of cutting needed to produce such a probe is extensive, increasing costs. GE scientists believe additive manufacturing can dramatically reduce those manufacturing costs.
“Imagine if we could print transducer probes like we print newspapers—super fast and at very low cost,” said Prabhjot Singh, a mechanical engineer and project leader on the ultrasound transducer project in a company press release. “It would help make ultrasound systems more affordable and more accessible to underserved regions where health care services are limited.
“For as long as the world has been making things, manufacturing has been a game of subtraction where you cut and machine parts down into the product you want,” Singh added. “While these processes have improved, valuable time and excess raw materials are still lost. With new additive manufacturing processes like 3-D printing and laser deposition, the traditional ways of manufacturing are being turned upside down.”
The pace of adoption
Additive manufacturing already is capturing the imagination of the popular press, and of popular culture. A January episode of the CBS comedy The Big Bang Theory included a plot line about Raj and Howard digitally scanning each other in order to make action figures of themselves with a 3D printer.
On a more practical note, a BBC report talks about Dutch architect Janjaap Ruijssenaars, who is fusing the bricks for his Mobius strip-shaped house from a 3D printer. His hope is to construct the exterior of the $5 million house entirely from the printed bricks.
"3D printing is amazing," Ruijssenaars told the BBC. "For me as an architect it’s been a nice way to construct this specific design. It has no beginning and no end, and with the 3D printer we can make it look like that.”
The potential uses for additive manufacturing are more along the lines of the latter example. “In the sheet metal forming business, you’re bending a lot of metal,” Stratasys’ DeGrange said. “With additive manufacturing, that can be done with push-button ease. You can make very complexly shaped parts with plastic. They’re half the weight and less cost.”
Are we within a decade of wide adoption of additive manufacturing? “I think that’s probably a fair statement. Adoption is coming rapidly, keeping up with the demand of industries pushing for faster, cheaper technology,” said EOS’ Snow. “The market demand is there. The technology is not going to pass demand, but it is going to keep up with the demand. Lots of people are developing new and bigger systems. Applications are going to drive the demand.”
Some of that demand already is being driven, mixing the best of the new technology and traditional milling solutions. At the 2012 IMTS Show in Chicago, EOS and GF Agie Charmilles demonstrated a system to manufacture precise tibial trays for surgical knee implants. The complete process utilized both a direct metal laser sintering (DMLS) system from EOS and 5-axis milling machines from GF Agie Charmilles.
“While we have our core competency DMLS system, highly developed parameters, and can process a wide range of part materials, we are still dependent when it comes to an end-to-end solution,” said Snow in a press release at the show.
The 3D CAD rendering of the tibial tray is created through the EOS additive process, using a titanium powder. Once completed, it moves to the 5-axis machine for final milling, using the same CAD model as the additive machine.
Where is this headed?
In the infancy of any technology, there is the wonder of it all. Any great transformative invention or idea of the last 100 years began with a simple promise of a wonderful new world opening up. Then come the inevitable pitfalls and issues, and additive manufacturing is no different.
Perhaps the thorniest question will be, who owns the design? “Just as we went through with music industry, the issue is intellectual property,” said NAMII’s Resnick. “People make their living designing components. In the past, manufacturing was the barrier to make something. You had to have knowledge. If we can print a part like we print a page, that breaks down those barriers. As we know with the Internet, there is great accessibility to designs—including certain things we don’t want widely available. So there are lots of policy discussions.
“At same time from the U.S. standpoint, if want to be competitive, have to push forward. That’s why NAMII was formed,” Resnick added. “We have to look at these other issues. One aspect is that this ‘maker movement’ is very exciting and they are going at it at such a fast and furious pace. There also is a need to have some wisdom being imparted, so we don’t go off in one direction and go over a cliff. So we want to do this at an accelerated pace, but also at a controlled pace.”
In the music industry, the protection of licensing and intellectual property, while not absolute, has opened up a world in which digital books, music, and movies are now available to consumers on an a la carte basis. Resnick sees similar potential for products via home-based 3D printers. “The implication of that is very significant,” said Resnick. “It will result in an increase in the appreciation of intellectual property. They will be buying someone’s intellect.”
In wider applications, Resnick sees additive manufacturing as a powerful technology for manufacturers—but still just one tool of many already available. “It becomes complementary to a number of processes,” he said. “Look at things like EDM and water jet. They have not detracted each other. They have augmented each other and provided additional capabilities. It may have a direct impact, but all in all, additive manufacturing helps all of us in the manufacturing community.
“We will see how much mass customization is embraced,” Resnick added. “In some cases it will be directly important. We need to absolutely have mass customization. There is a natural drive for that. It’s going to be another significant tool in the toolbox.”