Temperatures that are too high affect machine performance and lifespan.
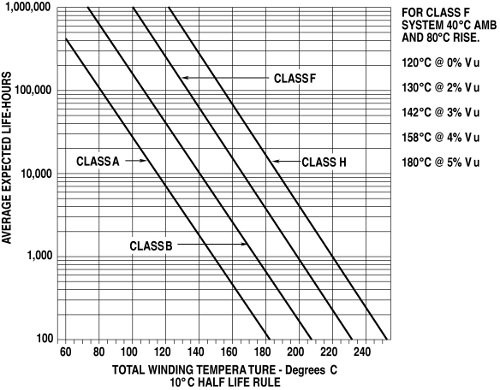
It’s not uncommon for a maintenance technician to call a service center about a repaired motor that’s now “running hot.” When asked how hot, the reply frequently is: “Well, I can’t hold my hand on it!” Think about that answer for a minute. The typical human can tolerate touching something that’s about 60 to 65 C (140 to 150 F), depending on calluses, threshold of pain, or how many people are watching. Now keep those numbers in mind as you read the following discussion of typical motor operating temperatures.
NEMA Standards MG 1-2011, 12.43 defines temperature rise for motors in a maximum ambient of 40 C. Two points are noteworthy here. First, in keeping with the NEMA standard, temperature is given here in Celsius; Fahrenheit equivalents are provided only where appropriate. Second, ambient temperature refers to the temperature of surrounding air. Some people confuse this with the expected temperature rise of the motor, which it is not.
The Class F (155 C) temperature rating is popular these days, so it’s a good one to discuss. With Class F insulation, the maximum allowable temperature rise ranges from 105 to 115 C for the motor’s winding insulation, depending on how the motor is configured. For example, if the motor that was reported to be “running hot” has a 1.15 service factor, its maximum temperature rise would be 115 C plus the 40 C ambient. The winding embedded in the slot is almost always the hottest part, so the winding temperature for this motor could reach 155 C.
Motor construction
The surface that our maintenance technician tried to touch will be somewhat cooler than the winding temperature, depending on the motor construction. On a large cast iron, totally enclosed, fan cooled (IP 54) motor, for instance, the surface may be 20 to 25 C cooler than the winding hot spot, but only 10 to 15 C cooler on a rolled steel frame motor, where the surface is much closer to the winding. Temperature differentials are often much greater—as much as 60 C—for open drip-proof motors (IP 12) and Weather-Protected I (WP I) or Weather-Protected II (WP II) enclosures. Differences in flat rolled steel and ribbed cast iron frame surfaces also affect the amount of heat our technician would feel.
Of course, motors are not designed to run at the maximum allowable temperature, because that would drastically decrease motor life. In fact, every 10 C rise in operating temperature reduces insulation life by half. Therefore the ultimate design is one that optimizes motor life and function, while keeping the cost of production, maintenance and efficient operation as low as possible.
As an example, suppose that a motor with a 65 C rise (very conservative by most standards) is put in service on a hot summer day. If the ambient temperature is 35 C (95 F), the winding total temperature would be: 65 + 35 = 100 C. If motor is so constructed that its surface is about 20 C cooler than the winding, the surface temperature would be: 100 – 20 = 80 C (176 F)—i.e., much too hot to touch safely! Remember that this is a conservative design, so the surface temperatures of many motors will be much warmer.
Thermally protected motors
At first glance, the maximum motor temperature rise limits given in NEMA Stds. MG 1, 12.43 appear to contradict those given for the same insulation classes in NEMA Stds. MG 1, 12.56 and Table 12-8. Actually, the maximum temperatures shown in Figure 3 apply only to “thermally protected” motors.
The words “Thermally Protected” on a motor nameplate indicate that a thermal protection device is an integral part of the machine and, when properly applied, will protect it from dangerous overheating. In other words, thermally protected motors are an exception to the rule. If the motor has this added, special layer of protection, the higher temperatures may be allowed. Based on our earlier example, you can see how these higher winding temperatures would impact the surface temperature of the motor.
Thermal protection and the correspondingly higher temperature limits are generally reserved for smaller motors. Even then, however, motor manufacturers will not design a motor to run at the maximum temperature allowed unless application considerations make it necessary.
Special cases
Some applications require that a motor be housed in an enclosure for noise abatement or other reasons. In such cases, special care should be taken to control the ambient temperature inside the enclosure where the motor is located. Cooling is usually adequate if the auxiliary cooling supplies the same volume of air as the motor’s integral fan.
If the driven equipment generates heat (e.g., a compressor) and is contained in the motor enclosure, it can contribute to the temperature rise of the motor. One example that comes to mind (details vague to protect the innocent) involved more than 100 compressors, each of which was housed in an enclosure with its drive motor and equipped with a radiator to cool the gas as it was compressed and liquified. Unfortunately, air for cooling was drawn through the radiator and then exhausted by a fan on the drive motor. With this arrangement, ambient temperatures in the enclosures reached 70 C, thermally stressing the motor winding insulation to its limit. Overheated lubricant also evacuated bearing housings, causing numerous bearing failures.
Temperature control is an important factor in successful motor operation. Care must be taken in the design, application and maintenance of these machines to optimize their performance and life. Having said all that, it is unsafe to place your hand on a motor to see if it is too hot; get a thermometer instead.
Jim Bryan a technical support specialist at the Electrical Apparatus Service Association (EASA).