The IPD process can be successfully used for grassroots projects, facility expansions, major upfits, and relocation projects. For many, the IPD system reduces project risk, delivers predictable results, and maximizes the effectiveness of capital funding.
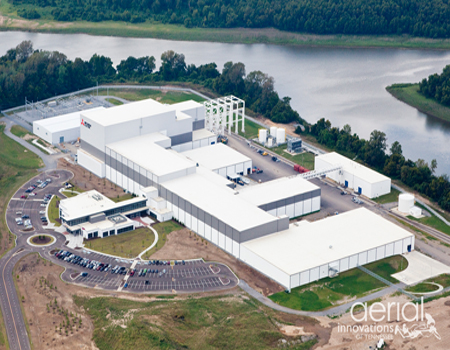
In the past, independent teams have focused solely on completing their portion of a construction project. Having separate workflows and hierarchies meant the flow of communication remained manageable. But the days of keeping each aspect of a capital project separated are a thing of the past. Communication has become much easier, not only in terms of conversations, but in terms of embodying and conveying complex ideas. It is desirable, therefore, that the efficiencies of a more collaborative workflow be captured. To accomplish this, integrated project delivery (IPD) has been used increasingly, achieving success in the industrial and manufacturing sectors.
What is IPD?
IPD is a collaborative project delivery system where the owner, design team, procurement, estimating, construction team, suppliers, and others, work together to optimize project results, minimize risks, reduce waste, and maximize efficiency. Rather than each participant focusing exclusively on their portion without considering the implications on the whole process, goals are jointly developed. IPD brings all participants together early with collaborative incentives to maximize value for the owner. With this approach, everyone has input and a stake in the project, and the risks and rewards are shared.
Why should it be used?
Industrial owners are increasingly focused on speed to market. Once a decision is made to invest in a capital project, owners now require aggressive construction schedules. In the construction industry, improvements in communication are enabled by building information modeling (BIM) and other software. BIM is essentially a set of processes that are supported by technology. For project teams formerly dependent on independent, 2-D renderings, BIM offers integrated virtual models that incorporate technical, physical, graphic, environmental, and operational data. Collaborative websites and mobile devices allow users increased accessibility and the ability to keep all communications, documents, drawings and other types of electronic files in one place. Through the use of version control, users are able to view and mark up files online without the need for native software.
Without these types of collaborative software, the practical implementation of IPD would be difficult. Technology has evolved to automate many of the processes involved in IPD, enabling project confidence, mitigating risk, and accelerating project delivery. Beyond its use in IPD, BIM also has the potential to add value for owners who are also managers of their buildings. As BIM allows for easier storage and transfer of information, the next application of this modeling software could be using it to seamlessly transfer from the end of the construction phase into long-term facility management and operation. The technology is bringing the true benefits of collaboration on board at the onset of the project, where it can pay the biggest dividends to both the owner and the project team.
Developing IPD
The IPD system was created in the mid-1990s. Many IPD principles were adopted from Lean manufacturing processes. The originators of the process believed that by working as one unit, the owner was better served and the construction project was completed faster, cheaper, and with less stress. Development of the IPD system was especially driven by the construction industry, which suffered from a productivity decline for decades. The IPD approach combats industry problems, such as schedule, budget insufficiencies, or adverse relations among involved parties, by allowing informed decision making early on in the project. Collaboration eliminates design waste and allows data sharing between the design and construction team.
IPD lends itself to the delivery of large capital projects in the industrial and manufacturing sectors, and these sectors are seeing some of the greatest gains from IPD today. Changes to ‘business as usual’ have happened so fast, however, that despite the efficiencies and improved outcomes associated with IPD, company cultures sometimes have a hard time adapting quickly enough to fully optimize these advantages.
Implementing IPD
Understanding the specific steps which can be taken to hasten the adoption of change will help move individual facilities closer to a productive implementation of IPD:
- Stage one: Several elements of a company’s culture can lay the groundwork for a smooth transition to IPD. The first is placing value on trust. As parties are united together through contracts and an equal, shared commitment to the project’s success, trust is a key component in working together successfully and minimizing conflict.
- Stage two: A second element is a desire to consistently analyze projects for opportunities to eliminate waste, identify savings, create efficiencies, and improve a facility’s lifecycle performance. Examining similar projects that could have benefitted from the IPD method helps provide the motivation to implement IPD for future projects with similar scopes.
- Stage three: Helping internal parties understand the differences between IPD and other delivery methods will help ease some of the discomfort that occurs when implementing a new process. By understanding their concerns and involving them in the discussion, the various parties will better understand how collaboration can be used to improve the delivery of capital projects.
Sometimes the transition can be undertaken in stages. If a project does not lend itself to full-fledged IPD, or a company is looking to “test the waters” before implementing an IPD model, there are opportunities to integrate elements of IPD without the full delivery method. This type of implementation considers IPD as a philosophy, not a delivery method, and it reflects an owner’s interest in collaboration and its inherent benefits. A crucial consideration in this situation, however, is to carefully define the collaboration so all parties clearly understand the expectations.
IPD in the marketplace
Speed to market is a delivery trend critical in the industrial and manufacturing markets, and it lends itself well to the IPD method. Owners and manufacturers determined to get their production facilities up and running faster can beat their competition to market. Many are companies entering new markets, particularly global companies wanting to continue to build their global footprint. These companies want to work with someone they can engage with early in the planning phase and use throughout their capital expansion program.
For industrial projects, IPD focuses on the final value created for the owner – the finished building. This approach engages owners very early in the process. An integrated approach aligns process and facility design from the beginning, providing a single solution for production operations and the facilities and utilities that surround it. The end result is a facility that meets the owner’s needs, through a process that is often faster, more efficient and less expensive. The integrated approach to project delivery can also enhance construction and operational safety. Construction risks can be minimized by reviewing complex project details and developing processes and procedures before construction starts on site.
Brian Gallagher is the director of marketing for O’Neal, Inc., an engineering and construction firm that specializes in the design and construction of manufacturing, chemical and pharmaceutical facilities.
Edited by Jessica DuBois-Maahs, associate content manager, CFE Media, [email protected].