Select the right products and equipment for the right situation
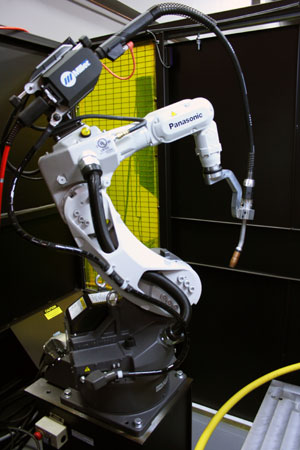
Companies make the investment in welding automation with an eye toward the potential long-term benefits it can provide — better productivity, improved weld quality and reduced costs. Protecting that investment and realizing a quick return on it is as much a matter of planning as it is one of proper equipment selection and usage. That equipment includes everything from the robot itself to small components, including the front-end consumables on the robotic MIG gun.
While seemingly insignificant, the nozzles, contact tips and gas diffusers used in robotic welding can have a marked effect on the overall performance of a robotic welding cell. Frequent changeovers can result in unnecessary downtime and costs. Poorly functioning consumables, or ones that are simply not appropriate for the application, can generate weld quality issues that compound productivity delays and could lead to expensive rework.
Selecting the proper consumables and implementing some best practices for storage, installation and maintenance can help ensure the best results, increase product life and support the benefits sought in welding automation.
General selection considerations
Robotic welding systems typically operate for longer periods of time and at higher amperages than a semi-automatic application, and may utilize transfer modes that are especially harsh on consumables. For example, Pulsed MIG programs — those in which the power source “pulses” between low background currents and high peaks — tend to generate high levels of heat that can erode contact tips more quickly.
For that reason, it’s important to select ones that are durable enough for the application. Contact tips are available in heavy and extended-life heavy-duty varieties composed of chrome zirconium, and are a good option for gaining longer performance due to their hardness (compared to copper). Typically, machined grooves at the base of the thread are the identifying mark for these types of contact tips.
Selecting nozzles and contact tips that are well-machined with a smooth, consistent surface is the key. Smooth surfaces are much less prone to collecting spatter, and therefore more likely to last longer. In some cases, these consumables may not be the least expensive option, but it’s important to weigh out the up-front costs versus the longer-term savings of minimizing changeovers and downtime.
Space and duty cycle factors
Space is always a consideration with robotic welding systems. Fixturing and tooling can limit the ability of the robot to maneuver to a part. Bottleneck, straight or tapered nozzles are common choices to accommodate for those restrictions since they are narrower than standard nozzles and can provide better access.
The more tapered a nozzle, however, typically the thinner it is. As a result, it may be less able to withstand higher amperage or higher-duty-cycles commonly used in robotic welding applications. For jobs requiring 300 amps or greater and/or those that have a high level of arc-on time, it may be best to select a heavy-duty style nozzle. These have thicker walls and insulators and are more able to resist heat.
In the end, a good rule of thumb is to select the heaviest-duty consumable for the application that still allows access to the tooling in order to make it last the longest. If in doubt about the best choice, consult with a robotic integrator or welding distributor for a recommendation.
Nozzle maintenance
Employing a nozzle cleaning station (also called a reamer) is a good defense against premature consumable failure and poor performance for many different styles of nozzles. A nozzle cleaning station cleans spatter out of the nozzle and clears away debris from the retaining head that tends to accumulate during the welding process.
These stations can also be outfitted with a sprayer that applies a water-based anti-spatter compound to protect the nozzle, retaining head and workpiece from spatter after cleaning.
For the best results, place the nozzle cleaning station close to the robot so it is easily accessible, and program the robot to use it in between cycles (during part loading or tool transfer, for example) so it doesn’t interrupt operation. It should only take 5-6 seconds for the nozzle cleaning station to complete its job and the results are measurable — less spatter and longer consumable life.
Storage and handling
As a best practice, keep consumables in their original packaging until they are ready for use. Opening them and placing them in a bin can lead to scratches or dents that allow spatter to adhere and will ultimately shorten the products’ life or cause them to function poorly. It can also cause dirt and oils to accumulate on the surfaces of the contact tip, which may impede them from properly seating together with the gas diffuser. It can also lead to electrical resistance and heat build-up issues that can, again, shorten their life span.
Wear clean gloves when handling or replacing contact tips, nozzles and diffusers. It helps prevent dirt, oil or other contaminants from adhering to them and leading to premature failure or poor performance.
Also, keep storage containers for new consumables separate from those for discarded ones to prevent the reuse of a contact tip or nozzle that may have dents or scratches and be prone to spatter accumulation.
Proper connections
Good electrical conductivity helps ensure consistent arc performance and weld quality, and can help minimize excessive heat and extend the life of the consumables. Installing the consumables properly — according to the manufacturer’s suggestions — and periodically inspecting them for good connections is the best way to ensure that conductivity.
Channel-lock pliers or other recommended installation tools work well to install contact tips and diffusers. Never use wire cutters or side cutters. Too much pressure from these tools can damage the inside diameter of the contact tip, and they can also cause scratches that attract spatter.
A good rule of thumb is to hand-tighten the contact tip until it is fully seated into the diffuser. Next, grip the contact tip with an appropriate tool as close to the base as possible, tightening it one-quarter turn past finger tight. Follow the same procedure for installing and tightening the diffuser so that it fully connects with the neck.
Some contact tips can be installed and held in place by hand-tightening the nozzle. Check the manufacturer’s recommendation for proper installation instructions
Finally, look for consumables that are designed to fully seat together and mate securely, too, as these can further increase their longevity by minimizing electrical resistance and heat build-up.
As with any part of a robotic welding system, the goal is to keep consumables in the best working order so that the robot is able to continue doing its job. That, in turn, allows companies to spend more time reaping the benefits of the automated welding process and less time troubleshooting problems.
Ryan Lizotte is a field technical support specialist for Tregaskiss.