Variable frequency drives (VFDs) are designed to reduce energy usage by controlling the speed of the motor and can offer cost-effective benefits for plants.
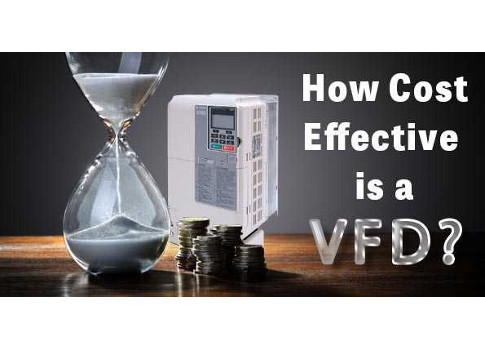
Most business owners are aware of the high cost of operating electrical motors, but there are ways to reduce the costs. Improving the efficiency of an electric motor will save money in the long run, but it is important to understand that not every choice is going to be the right choice for every application.
An example of one way that many businesses can save money in energy costs is through installing variable frequency drive (VFD) technology. VFDs are designed to reduce energy usage by controlling the speed of the motor. While useful, they aren’t always the best solution. There will be cases when VFD’s cost and installation overshadow the savings they can provide to companies.
Understanding VFD technology benefits
A VFD’s primary benefit is adjusting the speed of an ac motor by adjusting the available voltage. When the speed is adjusted, it helps to improve the efficiency of the motor, primarily by adjusting the output of the pump to match the flow and pressure requirements.
Any pump system that has a dynamic demand is a good choice for installing a variable frequency drive. If the pump operates at a lower flow than what is possible from the ac motor, controlling the motor with a VFD considerably reduces the energy consumption.
Installing a VFD can also extend the life of the motor by reducing mechanical wear, which, in turn, reduces maintenance costs, replacement costs, and can keep the motor running at high efficiency.
Is a VFD needed for the application?
A VFD is not always going to be the best choice for every design. Energy and cost savings need to be calculated to determine if it beneficial. This requires the operator to determine the minimum to maximum pump operation, estimate how long the pump would run at various speeds, and estimating how much energy is used at each flow rate.
When considering the costs associated with VFD installation, the operator also needs to consider the cost of the VFD and any potential rebates offered through the utility company for installing it. Factor in any reduction in expenses for maintenance or replacing the pump due to extended pump life from operating at lower speeds.
During a new installation, the benefits of a VFD are usually obvious. In a retrofit, however, there may be additional factors to consider, such as a larger footprint than a motor starter as well as the cost of power cables that may be necessary for the installation as well. In many cases, VFDs can help facilities save money once they are installed and utilized to their fullest potential.
– David Manney is a marketing administrator at L&S Electric. This article originally appeared on L&S Electric Watts New Blog. L&S Electric Inc. is a CFE Media content partner.