Although you may make every effort to ensure that a motor has a long life, there will come a time when it eventually needs to be repaired or will need to be replaced. At this point, one common question that is going to be asked is in regards to the benefits of repairing the motor versus replacing it with a new one.
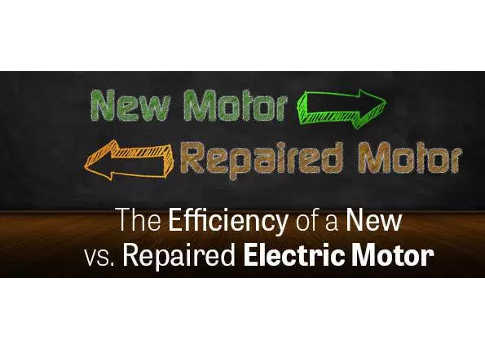
Although you may make every effort to ensure that a motor has a long life, there will come a time when it eventually needs to be repaired or replaced. At this point, one common question poses the benefits of repairing the motor versus replacing it with a new one.
Of course, the primary benefit to be considered is cost, but the bottom line may be somewhat deceiving. Many facilities managers will immediately consider the financial savings of repairing a failed motor, but the savings may only be during the initial purchase. When you consider all of the factors involved, is it truly more cost-effective to repair a motor? That depends on the efficiency of the motor and the cost of operating it from that point forward.
When considering energy efficiency, you need to get back to basics. Power goes into the motor, and it is converted into mechanical work but during the process, a certain amount of energy is going to be lost. That energy may be lost to heat, windage, or friction or combination of the three. Energy efficiency is a matter of reducing the losses in those three regards, and manufacturers have made significant strides in making new motors energy-efficient.
A common misconception associated with repairing or rewinding a motor is that you could not do so without reducing the initial efficiency rating. According to several rewind studies, it is possible to maintain the efficiency of the motor during a rewind or repair. As long as the proper practices were followed during every phase of the repair process, the efficiency could be maintained. What are some of the best practices that need to be considered?
One of the factors that must be considered is bearing friction loss. If you replace the bearings with anything substandard, it will result in a loss of efficiency. As long as you replace the bearings with the original bearing type, as well as use the proper lubricant, you will not lose efficiency because of the replacement.
There are some additional factors to consider when deciding whether to replace or repair a motor. It goes beyond being able to maintain the efficiency during the repair, and it is often necessary to look below the surface to make the proper decision.
First of all, you need to determine if the motor has been properly selected for the application. If the motor is exceeding its rated temperature or has sustained significant damage as a result of being improperly selected, repairing it would likely result in motor failure at some point in the future.
The bottom line is, it is possible to maintain motor efficiency if it is repaired properly. That doesn’t mean, however, that it is always going to be the best choice for every situation. Each motor failure must be considered individually to determine if it will be the best course of action for the long term to repair or rewind the motor or to purchase a high-efficiency replacement.
—David Manney is a marketing administrator at L&S Electric. This article originally appeared on L&S Electric Watts New Blog. L&S Electric Inc. is a CFE Media content partner. Edited by Erin Dunne, production coordinator, CFE Media, [email protected].