Maintenance is a perfect fit for an IIoT world.
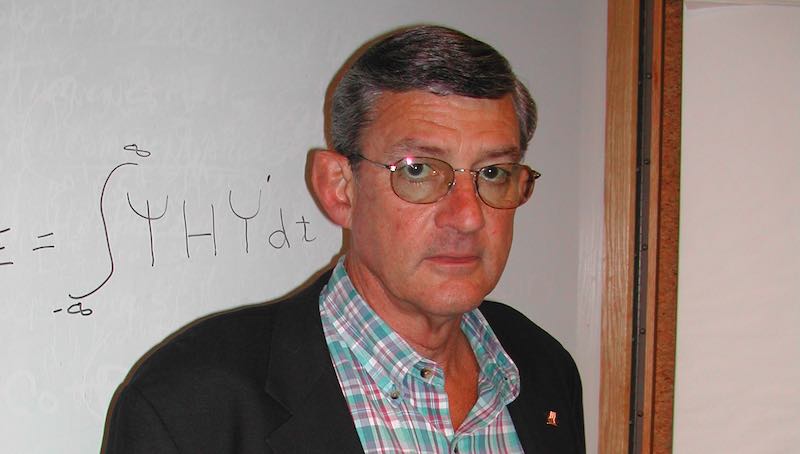
Maintenance 4.0 is the new buzzword for an improved level of condition monitoring, maintenance, and asset management. With Maintenance 4.0, the emphasis is on risk management maintenance. Some of the characteristics of risk management maintenance involve a higher level of condition-based maintenance through the use of sensors on critical equipment and through Big Data analysis that determines more precise trending and the state of the equipment.
Of course, determining the level of risk to the overall operation for each piece of equipment if it fails—and the economic impact—is taken to a much higher level. It is critical to take proactive steps to eliminate that risk for the equipment or system with the most impact. This could take the form of statistically determining if one brand of bearing lasts longer for a given application and using the longer-lasting bearing regardless of cost. In oil analysis, preferably through use of sensors, we monitor not just the health of the oil per se, but rather, the critical additive systems in the oil as they begin to break down. Thus, the oil can be changed before the machine actually sees degraded oil.
When one thinks of the enormous capital investment and the equally enormous repair expense in large wind turbine farms, a Maintenance 4.0 approach would seem the only logical method to manage these assets. Manufacturing robots also can be an expensive investment that is amenable to a Maintenance 4.0 approach. Interestingly, when you think about manufacturing something with complex robots, it seems clear that the operations and maintenance departments begin to merge into one.
An operator no longer makes or assembles things; the robot does that. The operator programs the robot to do what is needed, then monitors it through the use of sensors and Big Data analysis of the robot to see that it does what is intended. At the same time, the operator attends to the needs of the robot—its maintenance.
When you consider the risks and costs associated with operation of nuclear power plants, a Maintenance 4.0 program looks pretty good as well. At the OilDoc Conference in Bavaria, Germany, STLE-member Steffen Bots, the vice chair of the OMA Certification Committee and a member of the STLE Certification Board said, “The terms ‘Industrie 4.0’ or ‘Industrial Internet’ should indicate the starting point of a fourth industrial revolution following modern industry, mass production, and digital revolution. It is a synonym for automated production while all information about the production process, or the condition and performance of the production equipment, is continuously monitored. A key aspect of this idea is networking of machines, sensors and humans in order to communicate about the Internet of Things.”
Bots illustrated these concepts as they impact the oil analysis community with Oil Analysis 4.0. He sees that customers are asking for more and more data to be transmitted to them electronically. This requires that increasingly more testing, results, and interpretation must be monitored internally with sensors, programming, memory storage, and related IT services to allow the data to be sent—and ultimately to conform to Big Data computing and transmission. Oil analysis as a maintenance discipline uniquely fits the model for Big Data analysis for Industrie 4.0.
One of the Big Data challenges is that typical relational databases are not up to the task of managing the volume and statistical requirements. New storage, computing, and analysis methods are needed, yet there are no standards for such development. Equally, there are no models for secure access, data interpretation without human intervention to add application knowledge, technique, and context. Or, as Bots puts it, “someone sitting in the cockpit.”
Each part of the manufacturing industry has both its unique issues and the common problems related to use and implementation of Big Data. Indeed, we hear similar concerns outside of manufacturing with the concept of automated cars and trucks.
Yet, this is the nature of all transformative science and technology. There are very, very few “Eureka!” moments. Instead, there is much slogging ahead in the mud of technological trenches: two steps forward, one back. This is how progress is made. This is how science is made.
Bob Gresham is STLE’s director of professional development. He can be reached at [email protected]. This article first appeared in TLT, the magazine of the Society of Tribology and Lubrication Engineers, a CFE Media Content Partner.