Natural gas-powered reliability.
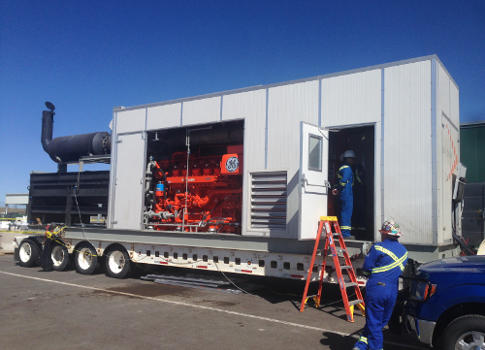
For healthcare centers, universities, and government facilities, it has been typical to install diesel engine-generator sets as standby generation. They are able to pick up critical elements of the facility electrical load if the utility power goes down. Diesel engines start quickly and, if properly maintained and periodically tested, provide reliable backup power. But what if another approach could supply reliable power not just to cover short-term outages, but could carry a major part of the site load in demand-response service, supplementing central-station power at peak times? Such a solution exists.
Natural Gas Engine-Generators
In a recent presentation at a Technology and Market Assessment Forum conducted by the Energy Solution Center, Aaron Trexler, Waukesha Senior Product Line Manager from GE Power discussed this alternative route. He noted the traditional approach for facilities that require standby power was diesel-fuel powered engine-generator sets. These are often sized between 500 kW and 3 MW. If properly maintained, they operate reliably for the relatively short hours needed in standby service.
However, Trexler noted, diesel units have their limitations. "They require on-site fuel storage for two or more days of operation, and that fuel has to be kept in good condition. Because of emission restrictions, unless they have significant upgrades for pollution control, they cannot be operated other than in emergency service.
Emission Restrictions on Non-Emergency Diesel
He explained that recent court decisions have confirmed emission restrictions for standby engines used on demand-response applications. "According to the U.S. Court of Appeals for the District of Columbia Circuit, beginning May 2, 2016, engines used for any demand response activity must meet emissions requirements for non-emergency engines. They must be fully compliant. Older engines are not grandfathered — they must be updated. Demand response with diesel just got more expensive, and fast-start natural gas units are a viable alternative."
Trexler suggests as an alternative that institutional and industrial owners should consider these natural gas-fired engine-generator sets such as the Jenbacher and Waukesha models offered by General Electric. "These units not only provide reliable standby power, but can also be used in a demand-response mode, reducing utility demand charges and providing economical site energy for 1,000 hours a year, or more. They are no longer a ‘stranded asset,’ but in effect become a profit center.
Rapid Start Now a Feature
Trexler indicates that at one time natural gas engines couldn’t meet the requirement to carry full load within 15 seconds. This has been overcome. This criterion for rapid startup in emergency situations can now be achieved by many Waukesha and Jenbacher natural gas engines, matching the performance of diesel engines. Qualifying Waukesha sets are available in sizes from 200 kW to 3.6 MW, and Jenbacher sets range from 200 kW to 10.0 MW. "These units are well proven, with over 36,000 units operating in over 170 countries."
Trexler noted the high efficiencies available with today’s natural gas-fired engines, with proven performance levels ranging from 35% to 50%, depending on size and type. "Application of gas-fired engine-generators in combined standby and demand-response service can show a payback as short as two and a half years. If yours is also a potential cogeneration application, it could be even sweeter."
Alternative Gaseous Fuel Options
Several of the GE lines of engine-generator sets are designed to use alternate gaseous fuels such as propane, CNG and LNG. This makes them practical alternatives even when there are no pipeline gas sources. This also fulfills the need when it is a critical standby classification that requires on-site fuel storage.
He noted that conversion of existing diesel engines to dual fuel (diesel+gas) service has some significant limitations. "You’re still using diesel fuel, so there are emission restrictions. Unlike engines designed for natural gas, these conversions do not have pistons, cylinder liners, crevice volumes or bowl configurations designed for gas. Their efficiency and reliability suffers. Our gas engines are designed to combust air/fuel in such a way to extract the maximum amount of power. The same cannot be said of today’s dual fuel engines."
Striking Fuel Cost Comparison
Additionally, Trexler pointed out the fuel economies with natural gas as compared with diesel. He indicated that with diesel at $1.88/gallon, the fuel cost would be $14.56/MMBtu, compared with natural gas at $2/MMBtu. "This would result in a diesel-only fuel cost for electricity of $131/MWHr versus $24/MWHr with pipeline natural gas."
He states that the cost of a natural gas-fired unit would typically be about 50% more expensive that a standby-only diesel. However, if the gas unit operates for 2,500 hours per year in demand-response mode, the project payoff is 2.5 years. This assumes no cogeneration application. There is no payoff for the diesel unit, because it can only operate in standby situations.
Quieter and Cleaner
Other advantages of gas engines include the fact that they are significantly quieter than diesel units. According to Trexler, the difference can be as high as 20 dB. Gas units on pipeline have no limitation on operating hours, and require relatively inexpensive emission controls as compared with diesel. He indicates the diesel unit will require five to ten times more expensive emission controls.
Now that the rapid-start issue has been overcome, for most institutional owners the choice of natural gas engines for combined standby and demand-response service is obvious. It’s the way for your standby system to pay its way. When you are installing standby power, keep this option in front of you.
MORE INFO:
Energy Solutions Center Info on Engine Generation
DOE Information on Distributed Energy
General Electric Power Generation
This article originally appeared in the Gas Technology Summer 2016 issue.