Key suggestions if your 2015 featured more “misses” than “hits” in maintenance. It might be time to think about getting more aggressive with your goals, activities, and accountability.
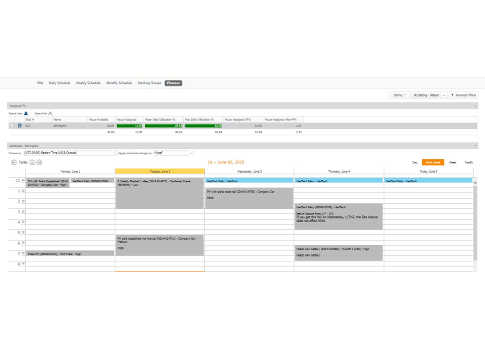
Before long, this year will be over and the next year will be here.
In your personal life, that may mean it’s time to wrap up the year and begin planning ahead. You may look back on the previous year and assess what you did well and where you still need to make improvements in your life. Perhaps you want to exercise more, or enjoy a long vacation, or keep in better touch with relatives or friends.
In life, we think about these steps for self-improvement all the time, but it’s really only at the beginning of a new year that we feel a compulsive pressure to act on them. New Year’s resolutions are a cultural phenomenon—many people have them and often we don’t want to feel left out, so we start making our life changes to fit in with everyone else.
Why can’t the same be true in a professional setting—specifically, when it comes to maintenance planning?
Just as it’s true in your personal life, it’s equally pressing at your place of business—as this year nears an end, it’s time to start making plans for 2016. What changes should your company make to the maintenance function? Is now the time to make a big move, such as budgeting for a CMMS upgrade or taking better advantage of the enhancements in a new release?
Here’s one way to go about establishing your "New Year’s resolutions" for your business. Start by making a list of what you achieved this year. Did you enact a mobile strategy? Did you reach a major target, such as reducing a percentage of corrective work orders? Celebrate the things you did right in your maintenance operations. Those represent significant steps forward for your organization.
You should also note your company’s shortcomings during the year, though. In your personal life, if you didn’t exercise or relax enough, it’s important to be honest with yourself, and the same principle holds true in your professional life. Look at where your operations came up short. If your 2015 featured more "misses" than "hits" in maintenance, then it might be time to think about getting more aggressive with your goals, activities, and accountability. Below are a few suggestions:
Matching KPIs with goals
If your time spent improving asset longevity should be below 1,000 hours annually, how are you working towards this goal weekly or monthly? Break down your goals into manageable increments and indicators and consult your KPIs on your CMMS dashboard on a regular basis. Work with your team to do the same for overall departmental goals as well. Sometimes it can be difficult to pull yourself away from the day-to-day "fires" to configure your KPIs—that’s when consulting services may be a good investment.
Automation, automation, automation
Regular e-mails can become a part of a routine no matter what your role in maintenance. Each of these e-mails, however brief, can quickly eat up the precious minutes of your day. See how you can automate your activities to the maximum extent your CMMS allows. Do you typically send out specific reports to upper management? Configure your CMMS to auto-generate reports on a weekly, monthly, or quarterly basis. Do you find yourself sending reminders about lapsed work orders to personnel? Set up e-mail notifications to be distributed if a work order hasn’t been modified in 7 or 15 days, as an example.
Fine-tuning the maintenance budget
Behind every successful business is an intelligent budget. This means that every dollar is spent on initiatives that make your operations more efficient, productive, and ultimately profitable. If you’re not leveraging your CMMS’ budgeting functionality for overall departmental spending or particular asset or site budgeting, you may not be calculating or tracking your maintenance funds as thoroughly as possible.
In conclusion…
The above strategies can prove beneficial for any company that cares about effective maintenance, but please note—it’s not necessary to do all of them right away. Think critically about the state of your business. Pick and choose appropriate areas to prioritize, and take action in 2016 on whatever initiatives can make the biggest difference for your business.
-Smartware Group. This article originally appeared on Bigfoot Blog. Smartware Group is a CFE Media content partner. Edited by Erin Dunne, production coordinator, CFE Media, [email protected].