Remote monitoring protects against skill shortages, complexity.
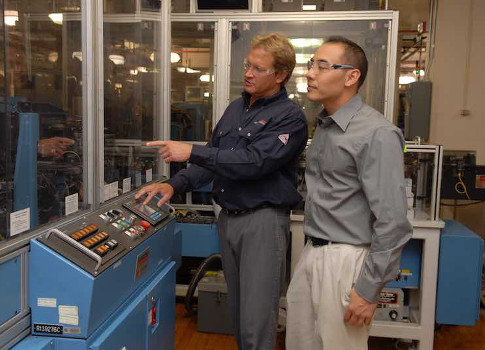
Avoiding downtime is a fundamental goal in any industrial operation. Improving uptime drives maintenance strategies, influences equipment purchases and sales goals, and it is entrenched in the minds of workers.
Even with a concerted effort to fight downtime, some companies are finding it more difficult than ever to control. There are a few reasons for this.
First, the jobs that are most vital to preventing downtime—industrial maintenance technicians—are becoming harder to fill. Experienced maintenance technicians are retiring and too few skilled young technicians are entering the workforce to replace them. This is part of a larger industrial skills gap that is expected to result in 2 million manufacturing jobs going unfilled between 2015 and 2025, according to report from Deloitte Consulting and the Manufacturing Institute.
Second, connected operations are adding greater complexity to industrial environments. Production systems are converging with information systems, and production downtime now goes hand in hand with network downtime. There’s a significant opportunity to use data available from connected operations to help reduce or prevent downtime, but that opportunity only can be realized with the right resources and expertise in place.
Finally, the simultaneous move to more flexible manufacturing processes has introduced its own complexity. Today, many companies need to produce multiple products in a single facility while minimizing changeover disruptions.
To keep operations up and running amid these challenges, more companies are turning to remote monitoring and support services.
Support is always there
Remote monitoring begins with collecting data from a company’s industrial assets. This data—which includes voltage, vibration parameters, temperature readings, and warning and fault information—then is contextualized into actionable information and delivered to workers.
Remote monitoring can be internally managed, with automated systems that deliver information directly to on-site workers. It also can be externally managed by a remote-monitoring service provider’s team of off-site specialists. These specialists monitor critical equipment and systems, and they can quickly notify on-site personnel of any detected issues and potential responses to those issues, or even predict some failures before they happen.
These remote-monitoring services can be scaled to address a company’s exact needs, whether it is monitoring a single machine in a plant, several pieces of equipment, a full production line, or applications, systems, and networks across multiple plants.
Some companies also choose to build additional services on top of remote monitoring. These services can include various forms of administrative support, such as system backups, recovery support, and patch and update recommendations. They also can include parts and on-site engineering support being delivered within specific response-time windows.
It’s not only manufacturing and industrial producers that can reap the rewards of remote monitoring. Machine builders can use it to gain new insights into the performance of their distributed assets. They can also use it to expand their service offerings, with the option to either manage the monitoring in-house or outsource it to a third party.
Industrial companies struggling to fill maintenance positions face a higher risk of downtime or even full plant shutdowns. In these cases, remote monitoring services can be used for key maintenance tasks when local talent isn’t available.
Case study: Distance learning
A coating company recently modernized the production lines at one of its facilities with new automation technology to increase capacity and address obsolescence issues. The project included installing new HMI systems on each line, and transitioning a paint line from decades-old motor generators and dc motors to new integrated controllers and drives. But because the facility is in a rural area, the company had limited access to engineers with knowledge about the new technology.
The company decided to use a remote service provider for around-the-clock system monitoring. The remote team monitors about 2,500 data points from controllers, drives, HMIs, and regulatory compliance parameters, and can notify on-site staff of any issues.
In addition to augmenting on-site staff, the remote monitoring support has provided predictive maintenance benefits to the facility. The remote support team can track the progress of maintenance issues, monitor trends and tolerances of devices, and track lifecycles. The team can then alert on-site staff of issues as they arise, and help them head off problems before a line stoppage occurs.
After implementing remote monitoring, the coating company saw a 50% reduction in maintenance downtime at the facility.
Case studies: Improved response
Other companies have used remote support to help manage the added complexity of modern operations where traditional IT support may not be a good fit.
This was the case for a large food manufacturer that deployed Ethernet and managed switches on the plant floor. The manufacturer initially decided to use its traditional IT provider to support the equipment, but they couldn’t provide the response time needed to keep things running on the plant floor.
As a result, the manufacturer switched to an industrial remote support provider. The support included monitoring of more than 400 switches, alarm profiles to monitor eight key parameters in those switches, and a 10-minute guaranteed response time to any critical alarm.
After the change, the company saw a significant improvement in uptime. In another case, a paper mill was experiencing challenges with instability and sheet breaks when switching between products. The company had recently installed a new drives system, but lacked the technical expertise to manage and support the system.
The company made the move to a service provider for remote technical support and troubleshooting. The support significantly reduced downtime, resulting in an annual revenue increase of $630,000. The mill also realized hundreds of thousands of dollars in additional savings in training and support costs.
A secure approach
Remote support is so widely used now that service providers have largely developed standardized services that can meet the needs of most industrial companies. Before selecting a service provider, however, companies should be sure the provider meets certain security requirements.
Companies should make it a point to work with a trusted service provider, one that follows core security principles when designing products. They also should confirm the provider’s platform delivers secure remote access, such as by limiting entry points, using outbound-only connections, and limiting access by user, site, and device.
By addressing security upfront, industrial companies can worry less about the risks of remote access and focus more on how it can help them keep their operations running in today’s fast-changing world.
Ante Tomicic is remote support services supervisor and Phil Bush is remote monitoring and analytics product manager for Rockwell Automation.