Despite propane’s established reputation on the floors of facilities of all kinds, a few misconceptions about propane forklifts persist.
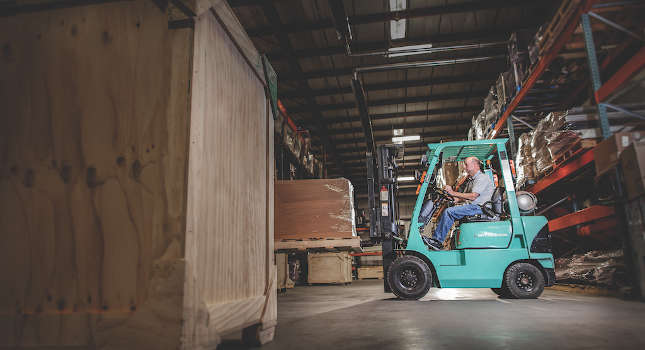
Propane forklifts have long been a key piece of equipment in plant and facility operations across the globe. From their first appearance in the 1950’s, propane forklifts commanded markets with their versatility and payload capacity. Propane still powers more than 600,000 forklifts across the United States today.
Despite propane’s established reputation on the floors of manufacturing plants, distribution centers, and facilities of all kinds, a few misconceptions and myths about propane forklifts permeate the marketplace. The following are the most common myths associated with propane forklifts and the truth behind each.
Myth #1: Propane is a gaseous fuel, so it can’t be used indoors.
Actually, one of the biggest advantages to using propane forklifts is the fuel’s versatility to operate inside, outside, on concrete, or dirt.
Well-maintained propane forklifts produce much lower levels of carbon monoxide than gasoline or diesel, so they can be used anywhere electric forklifts operate in properly ventilated facilities. This versatility is especially noteworthy when considering that 68% of forklift fleets work both indoors and outdoors, according to a recent survey conducted by the Propane Education & Research Council (PERC) of individuals responsible for managing and/or maintaining their companies’ forklifts.
Propane forklifts can handle small loads as well as loads heavier than 10,000 pounds. In fact, 70% of respondents to the PERC survey reported using propane forklifts for loads between 5,000-10,000 pounds—34% actually reported using propane forklifts exclusively in this weight class—in part because of the varied applications for which forklifts are used.
One example is Renze Display, a company that prints, builds, and ships state-of-the-art displays, graphics, and trade show exhibits up to 5,000 pounds from its Omaha-based office and warehouses. The company uses propane forklifts to maneuver products between shipping bays, fabrication, and storage because they needed equipment that ensured a healthy work environment when doors were constantly opened and closed between its office, manufacturing shop, and warehouse. For Renze, the difference between using propane and electric forklifts was the difference between sending a product on time or disappointing a customer with a late product because its forklifts were recharging.
In multi-shift facilities where work continues day and night, propane provides the quick refueling necessary to keep materials moving. Swapping out an empty propane cylinder for a full one takes less than a minute, so plants don’t need to purchase extra expensive batteries or allow for downtime during shifts for recharging. Refueling schedules can be tailored with a propane retailer to ensure a plant’s cylinder cage is always full.
Myth #2: Propane forklifts cost too much.
Plant managers using propane forklifts can actually see several advantages on costs compared to diesel and electric forklifts. Propane forklifts are less expensive at acquisition than electric forklifts. Plus, Tier-4 diesel requirements are already adding thousands of dollars to the purchase price of diesel equipment.
Electric forklifts are often miscategorized as equipment with fuel that’s only paid for during the initial purchase. But in reality, ongoing costs occur with electric forklifts as with any other type forklifts. Plant managers must also consider that battery life and power output will diminish over time and lead to future costs that can go overlooked. These costs include additional battery purchases, which can also add thousands of dollars to the lifetime cost of the forklift. Don’t forget about an increase in utility bills to constantly recharge the batteries for an electric forklift fleet, too. These ongoing charges can begin to add up in overall facility costs, especially with larger fleets.
In contrast, an investment in propane cylinders and storage cages can last decades. Facilities can set up a fuel delivery or propane cylinder exchange program and fuel contract with a local propane supplier to ensure an affordable price per gallon to make fuel management (and budgeting) simple.
Myth #3: Electric forklifts are the only way to reduce emissions.
For companies that want to reduce their carbon footprint, electric forklifts may seem like the only answer. However, that’s not true by a long shot. Propane forklifts offer emissions reductions for facilities still using older diesel forklifts, commonly used in the 10,000-plus pound forklift market where larger loads are being moved and power matters. Propane also offers reduced emissions compared with gasoline, natural gas, and even electric forklifts.
Regardless of weight class, emissions are taking on an ever-increasing importance around the country. Propane can be a cost-effective solution to reducing emissions while maintaining the power needed to handle larger jobs. Recently, PERC contracted with the Gas Technology Institute (GTI) to execute a comparative emissions analysis of forklifts. The analysis found that propane forklifts reduced greenhouse gas (GHG) emissions by 16%, NOx emissions by 17%, and SOx emissions by 15% compared with gasoline forklifts. Compared with natural gas, propane forklifts reduce GHG emissions by 11%. PERC also found that although electric forklifts produce no emissions during operation, using propane forklifts can reduce SOx emissions by 76% compared to electric when total site-to-source emissions are taken into account.
Given the right setting, propane forklifts can help plant managers and facility operations be more productive, while reducing costs and lowering a forklift fleets’ emissions profile. To learn more about how propane forklifts can improve plant operations, visit propane.com/industrial.