Benefits of microprocessor-driven linkageless burner controls include optimized combustion, repeatability, improved safety control, maximum turndown, fuel and energy savings, and reduced emissions. Modern linkageless control systems include combustion sensing equipment, precise modulators for fuel and air and, ideally, an exhaust gas analysis feedback system.
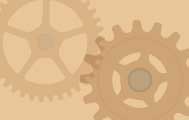
Linkageless control systems on boilers or other industrial burners can reduce energy consumption and harmful emissions, and assure better combustion. These systems control the combustion process using microprocessor technology, and are often combined with an exhaust emission analyzer to assure continuous ideal combustion.
Aqeel Zaidi, Energy Solutions Manager from Enbridge Gas Distribution in Ontario, has wide experience working with customers in improving burner efficiency. He indicates, “By eliminating the slop in mechanical linkages, linkageless controls will run a boiler at repeatable air-fuel ratios at all firing rates, resulting in optimum fuel combustion and safer boiler operation.”
What We Used to Use
Until the 1980s, nearly all burner fuel and draft controls operated through mechanical linkages. These used levers, jackshafts, cams, chains and gears. They were often adjusted with set-screws and spring tension. Under the best designs, there was inevitably some “play” in the control mechanism. Combustion could be optimized at one or a few points of the firing rate, but there were always points of less than perfect excess air control.
Perhaps most importantly, with repeated operation and changing environmental conditions, the linkages would drift out of calibration. From a process standpoint, the only feedback loop was the occasional check of combustion efficiency and exhaust gas conditions by a diligent operator, and not all operators did that with great frequency.
Beginning a few decades ago, manufacturers started using increasingly reliable and affordable microprocessors and sensors to create controls that always stayed in calibration and were sensitive to the smallest change in combustion or fuel conditions. The day of linkageless controls had arrived. John Devine, Vice President Sales and Marketing from Fireye Inc., compares traditional mechanical linkage controls with linkageless systems being like an old-fashioned carburetor to the precision of modern fuel injection.
Optimizing Combustion
Benefits of microprocessor-driven linkageless burner controls include optimized combustion, repeatability, improved safety control, maximum turndown, fuel and energy savings, and reduced emissions. Modern linkageless control systems include combustion sensing equipment, precise modulators for fuel and air and, ideally, an exhaust gas analysis feedback system, or “oxygen trim.” Zaidi notes, “Additional savings can be achieved if an oxygen trim is installed in conjunction with linkageless controls.”
Without oxygen trim, most boiler codes require a minimum of 15% excess air (3% oxygen). With an operating trim system, the boiler can often be operated more closely to an ideal fuel-air-mixture. Yet the oxygen trim capability is not inexpensive and can only react to instantaneous boiler load conditions. Thus for rapidly changing steam demand situations, oxygen trim may not be the best control option. A boiler consultant or linkageless control provider can advise you when the addition of oxygen trim can provide improved operations and energy cost savings.
According to Dennis Wood from Autoflame, a major manufacturer of these controls, emission reductions with linkageless systems can be significant. He cites a recent industrial installation where the system reduced NOx emissions 30% and carbon monoxide emissions by 92%. By improving combustion efficiency, the plant’s total carbon footprint is reduced.
The Added Benefit of Digital Controls
The status of the control system and the conditions of combustion are usually shown on an electronic display. Digital boiler controls also add additional safety features and many have data logging capabilities, allowing evaluation of boiler operations and often providing data to support preventive maintenance.
Linkageless controls, whether in a new boiler or in a sound older unit, can save energy, extend the life of the boiler, and reduce emissions. In a recent presentation at a Technology and Market Assessment Forum sponsored by the Energy Solutions Center, Carl Manoogian from Honeywell noted that of an installed base of 571,000 boilers in commercial and industrial service in the U.S. and Canada, fewer than 5% currently have linkageless systems installed. The opportunities for major improvements are great, Mechanical linkage combustion control is rapidly becoming obsolete. Now may be your time for a change.