Brutal honesty needed to properly manage, evaluate overall equipment effectiveness.
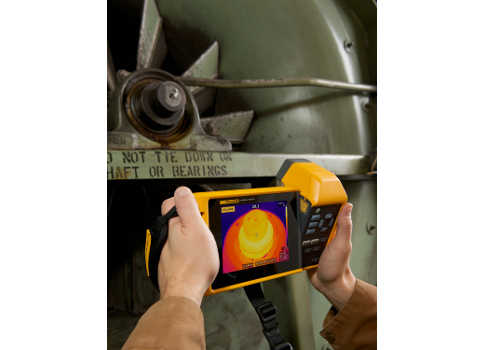
It’s a statistic. It’s a useful benchmark. But overall equipment effectiveness (OEE) is best used as a baseline for improvement, not merely a bragging point to show how well your manufacturing line, machine, or plant is running.
When managers initially calculate an OEE score on individual production lines, they are often shocked at how low the OEE score really is, and then they keep it quiet. However, production lines in the 30% range aren’t uncommon.
An outgrowth of the Lean manufacturing movement, Seiichi Nakajima of the Japan Institute of Plant Maintenance (JIPM) first described OEE in 1982 as part of the total productive maintenance (TPM) methodology, according to the OEE Foundation. By the mid-1990s, OEE had become a best practice management tool and a key performance indicator (KPI) to evaluate plant floor productivity. The metric empowers companies to improve their processes, compare themselves against a "world-class" standard, and, in turn, ensure the quality and consistency of products.
Beyond the numbers
OEE is a fairly simple formula: OEE = Availability x Performance x Quality. The percentage of each top-level variable is multiplied to determine the OEE score. Thus, an OEE score of 100% represents perfect production, while 40% to 60% is considered typical and 85% is world-class. Lower scores are often found when OEE programs are just getting started.
Yet, as it is with all high-level analyses, the complete story includes a number of important inputs. Those inputs go into each one of the top-level categories used in the OEE score, revealing losses and pain points that negatively impact how well your plant is running and the quality of products.
"People don’t like to advertise that this line is a 42%, or this line is at 49%," said Ken Bannister, a Toronto-area manufacturing consultant who works with companies to improve maintenance practices and OEE scores. "They don’t talk about it because someone is going to ask, ‘Why are we so bad and inefficient?’"
But it’s important for managers in manufacturing, chemical processing, oil and gas, and other factories to know that while an OEE score is a key top-line metric to reveal how well your operation is running at a given time, the score is just a data point fixed in time. It’s a benchmark that can swing.
To be sure, each manufacturing team knows the critical equipment and processes used to create products. It’s that critical equipment-typically the most expensive to replace-that draws the most attention and maintenance. But the OEE metric provides a more holistic view of your operation, a way to monitor and improve efficiency in your manufacturing process by going beyond simple uptime measurements.
"If a company has a brand-new line and its sister company has a line that’s 30 years old, and they both make the same product, the OEE will truly be different," said Bannister "You then need to come up with some way of harmonizing them so it’s an apples-to-apples comparison. One way to do that is to look at specific problems and specific downtime occurrences the line is experiencing. And if maintenance-related downtime can be prevented or predicted … that improves OEE."
Uptime of equipment is essential to all industries. Unplanned shutdowns not only impact your OEE, but they also can cost thousands of dollars in repair or replacement of critical equipment and, of course, the associated labor costs.
"There is a reason that availability is the first variable in the equation," said Bannister. "If you don’t have availability, and that’s tied to maintenance, quality and throughput don’t matter. As far as OEE is concerned, when machines get out of adjustment and experience trouble, you have potential failure and you not only lose throughput but you can put quality at risk.
"It depends on the industry," he added. "If you’re looking at a company that makes a frozen food like frozen pizza, you can use an infrared camera to determine whether it’s frozen correctly or if there are leaks in refrigeration. That directly effects quality, by the failure to cure the frozen food properly."
Thermal imaging at a substation
One example was recently seen at an electrical substation, which has many complex electrical systems and equipment that handle very high voltage current. To help ensure safe and consistent performance, more utilities are using infrared cameras to run proactive maintenance inspections on equipment ranging from oil-filled transformers to lightning arrestors to high-voltage transmission lines coming in and out of the substation.
A thermographer scanned the substation with an infrared camera and discovered the knife switches showed abnormal temperature. Because there appeared to be high resistance a short distance from the switch, that overheating could have led to a failure. Finding this situation in a routine inspection could potentially save the utility company and its customers a major power outage. Without the inspection, a switch knife failure could have occurred and caused unplanned downtime. This would have directly impacted the availability of equipment, thus the OEE matrix.
Six big losses
The major goal in any OEE program is to minimize or reduce the causes of inefficiencies. To determine what events contribute the greatest loss, thus what should be targeted by countermeasures to improve performance, loss events associated with availability, performance, and quality are identified and quantified. These can be calculated manually or through a number of free calculators available online.
As can be seen in Figure 1, preventive maintenance strategies to avoid equipment failure, slowdowns, and rejected parts are important to an OEE calculation.
When determining your OEE, don’t get caught up in the initial metric and how it compares to the rest of your industry. Instead, use the OEE metric as a baseline from which you can achieve and celebrate success.
Frederic Baudart is a product application specialist with Fluke Corp., based in Everett, Wash. He can be reached at [email protected].
SIDEBAR:
Breaking down the OEE metric
Breaking down each metric gives us a picture of just how valuable the full picture of the OEE metric truly is to your process.
Availability
Availability answers the question: Is the machine running or not? Availability also takes into account downtime losses. It is a percentage of the amount of product time the machine is running in proportion to the amount of time the machine is available.
Availability = Run Time / Total Time
A key input into the run time, of course, is unplanned downtime, which cuts into the availability.
Performance
By definition, performance is a percentage of the total parts produced by the machine to the production rate of the machine. Or, in other words, how well the machine is running when it is running.
Performance = Total Count / Target Count
Quality
Quality is a percentage of the parts produced that meet specifications out of the total parts produced on a machine or process. Simply put, how many good parts versus bad parts a machine or process has produced.