How bridging the gap between building utility controls and process controls enhances plant performance.
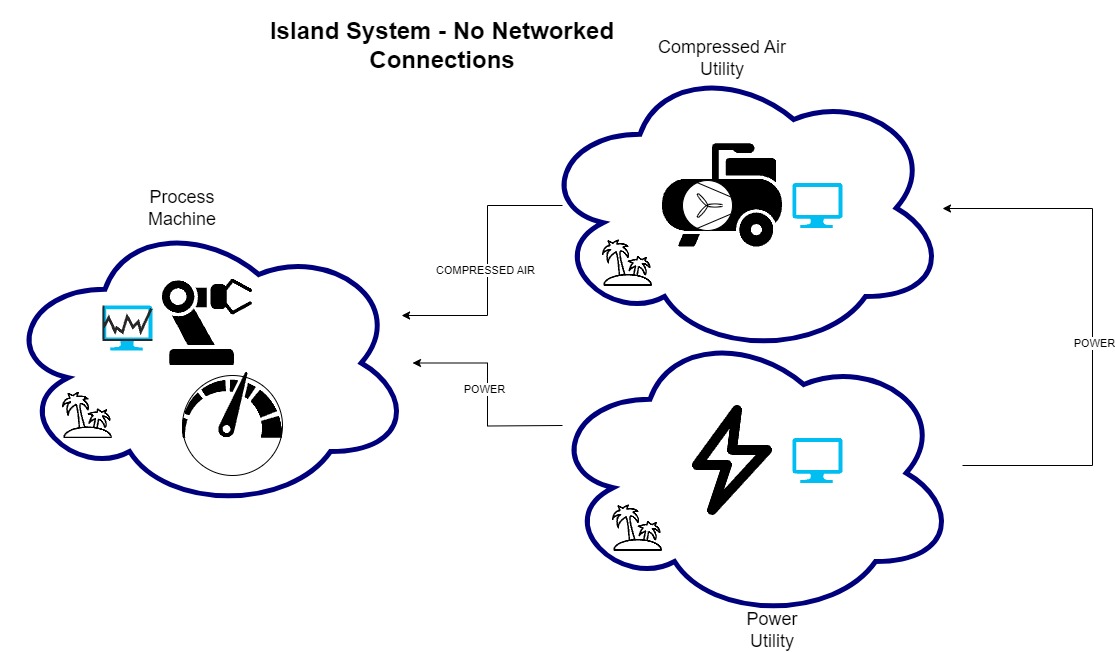
Learning Objectives
- Comprehend the benefits and significance of integrating building utilities controls and process controls to enhance plant performance.
- Understanding the importance of a documented long-term plan for the integration of control systems.
- Gain insights into the technological intersections, key terminology and upfront planning strategies essential for cohesive control system integration.
- Gain a basic understanding to have a cohesive system that integrates both major components of a manufacturing facility.
Control insights
- This article is tailored to two members within the plant design team: the building direct digital controls designers and the manufacturing process automation controls specialists. The professionals from both realms will gain a comprehensive view of the larger industrial control ecosystem, understanding how integration can directly enhance operational performance and plant efficiency.
- It is important to note that integration between the two control systems may not be universally necessary. It is something that needs to be assessed on a case-by-case basis during upfront planning.
A cohesive control system manages and optimizes interactions between machinery and utilities for efficient production. The lack of adequate coordination between the machinery and utilities can lead to interruptions or inefficiencies in a manufacturing system.
A unified control strategy can harmonize the communication between the traditionally segregated control systems in the plant to ensure that the disparate systems are running in an integrated fashion. The integration enables centralized communications and trend logging capability across seemingly independent systems that, in fact, are interdependent for optimal plant operations.
Planning control strategies
The primary barrier to an integrated architecture is not one of a technical nature but rather a lack of upfront planning. To facilitate the communication between the building utilities control and process automation control systems, a well-thought-out plan is essential.
This plan involves a carefully strategized and integrated operational technology (OT) network, supervisory control and data acquisition (SCADA) system and IT system. Additionally, it provides a roadmap for vetting original equipment manufacturer (OEM) machines that would enable control and data to be centralized in a redundant and high-availability system.
A carefully thought-out and well-documented roadmap is the most critical step to having an integrated architecture. Without this, plant managers risk increasing the cost and complexity in integrating these two systems in the future. Human machine interfaces (HMI) and controls are usually localized at each machine and logging the data that exists on these standalone machines becomes more challenging. It is doubtful that maintenance staff manually pool this data together with the rest of the facility’s devices in a central location. Even if they do so, the next question is whether it is in a manageable format for analytics and optimization.
Not having a clearly defined and communicated roadmap can lead to equipment purchases that cannot support cross-platform integration. Achieving this integration would require adding intermediate communication gateway devices or replacing the equipment all together. Both options are more expensive than initially procuring equipment that supports the upfront plan. Without a plan, it is likely that the network infrastructure is not easily expanded, has more security vulnerabilities and is more susceptible to network failures. Chances are that the equipment ordered will be from various vendors making maintenance and support more difficult.
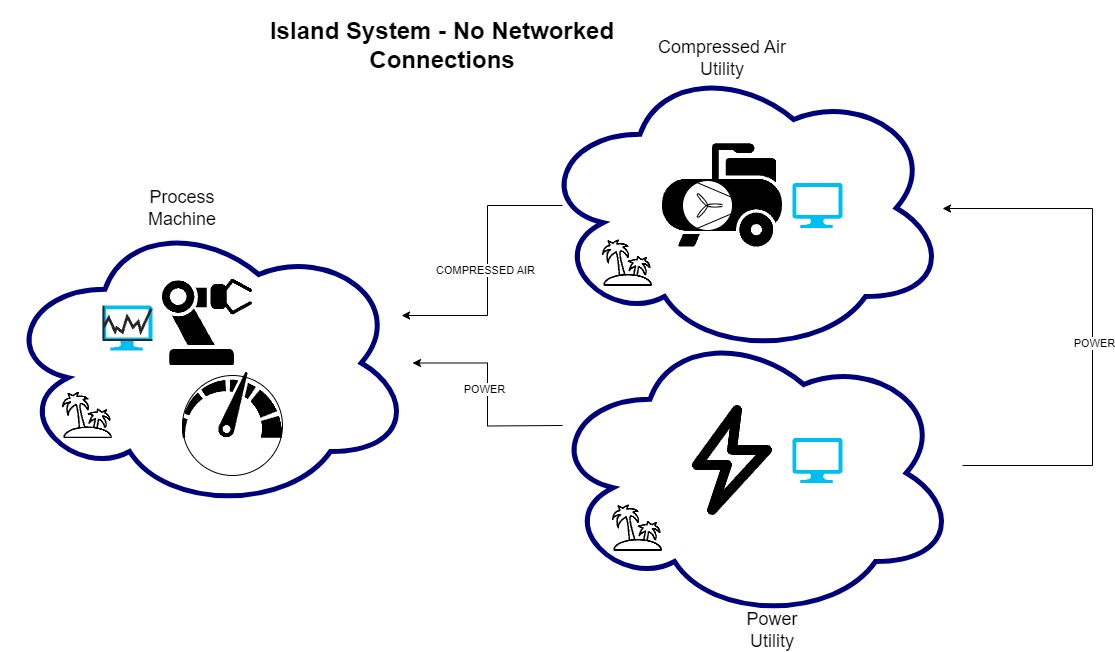
It is crucial to take the time to develop a long-term OT network, SCADA and IT strategy. This is the most critical step to both building new sites and to deliberately upgrading existing sites. A vision and standards document must be in place for all and it must be driven to ensure all major players and contractors are aware of it.
Any equipment purchases or any project plan has to be validated to align with this long-term plan. Particularly in the beginning, effort will need to be placed on enforcing the plan. If in-house expertise is not present, it would be recommended to partner with trusted and proven outside consulting partners to create this plan. This document will set the foundation for an organized digital transformation, enabling the integration of the manufacturing process systems and the building utility system controls.
OT network control
The OT network is arguably the most important section of the upfront plan. The OT network will serve as the backbone of the whole process and enable communication between all systems. Once this has been thought out, it provides sites with the flexibility to establish reliable, secure and widespread communication paths to all areas and devices. A cohesive network plan ensures that all purchased and installed equipment follows a unified strategy. Unfortunately, many sites overlook having an organized OT network, yet it is the most critical component that enables a digital factory or Industry 4.0.
Not having a network plan in place can introduce many complications. Networks built without much foresight typically end up being flat networks. Expanding on a flat network or adding new equipment without proper planning can be dangerous. A single network issue can potentially disrupt the whole plant.
Security is nearly nonexistent on flat networks. If devices and machines are purchased without external network capabilities, there is no way to enable their communication path to a central SCADA system. Attempting this after the fact will be cost-prohibitive and might require purchasing from another OEM altogether.
With a robust network plan in place, all equipment, whether building utility or process, should possess the necessary network capability to integrate into the overall system. This ensures that all new equipment will not be constrained to its own communication island. The plan dictates how plants divide their areas using virtual networks with managed switches. This approach prevents any network issues affecting one area from impacting other areas within the plant. A well-designed communication backbone leaves manufacturing plants well-prepared for expansion and the addition of new equipment.
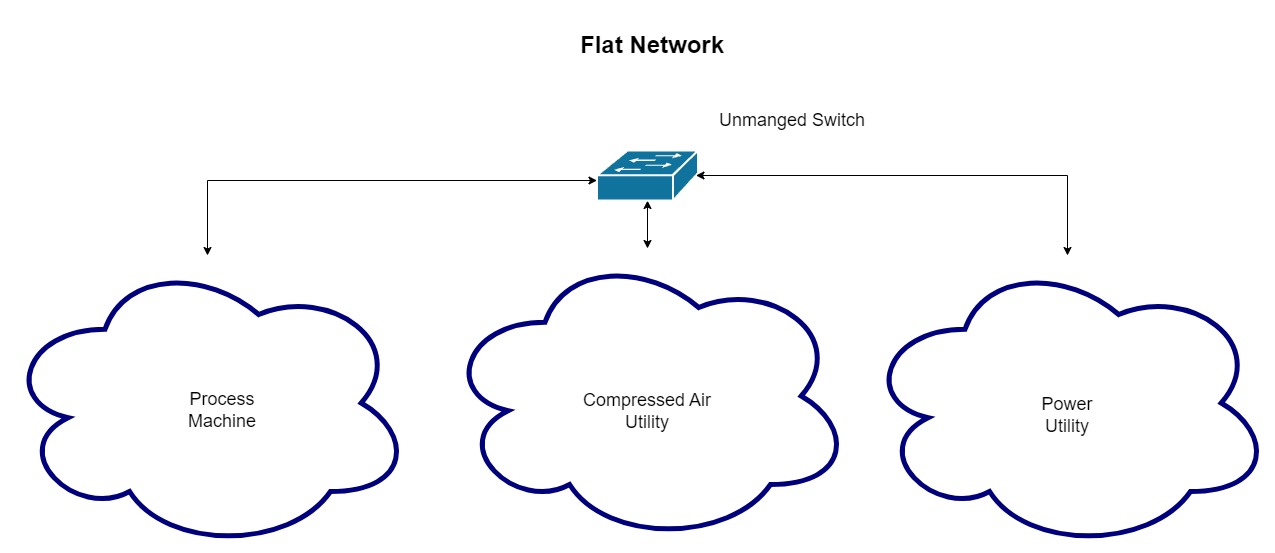
Selecting a SCADA system
To pave a clear path forward, establishing a standard for the SCADA system is essential. The choice of a SCADA system involves weighing the pros and cons of each option. When vetting OEM equipment, selecting an OEM system that seamlessly integrates with the existing SCADA system facilitates easier maintenance and upgrades by the controls team.
Other things to consider when selecting a SCADA platform:
-
Cost
-
How well it integrates with third-party or other external software on the IT side (e.g., enterprise resource planning, or ERP).
-
Internal maintenance capabilities.
-
Scalability
-
Third-party support.
The other problem typically seen with unplanned SCADA systems is that the SCADA system has one application that treats each system as completely separate applications. As a result, there is no visual interface to quickly and accurately pinpoint issues in large facilities.
During the early phases of selecting a SCADA system, it is crucial to understand which protocols it supports. Some common protocols include Modbus, OPC UA or BACnet. Additionally, one also needs to understand the industrywide support for these protocols among OEMs and their troubleshooting complexities in the SCADA selection process. This knowledge drives requirements when choosing OEM devices.
In SCADA system design, simple and effective navigation and plant overview should be prioritized. A holistic view of the entire site is enabled by connecting utility systems and plant processes to the same central SCADA system.

IT/OT convergence
This is a key factor in enabling powerful analytics for manufacturing. What this means is that the OT/plant floor systems/SCADA system are in some way shape or form, integrated with IT software like ERP systems. For an even more comprehensive system, especially for companies with multiple sites, this entails pooling information from all sites for analytical purposes.
The whole purpose of Industry 4.0 is to facilitate the flow of data from both plant floors and business processes. From there, its purpose is to then allow businesses to make informed decisions or implement dynamic improvements based on the analysis of this data.
Both IT (primarily from a business side) and OT (from operations side) need to understand each other’s goals and find the right software solutions to accomplish them. Fundamental tools such as barcode tracking/serialization and other production metrics provide insights necessary for accurate forecasting.
To bring this full circle, adding the utility systems to the overall SCADA system is another part of gauging overall plant performance with IT/OT convergence, businesses can track performance across their enterprise. Just as pain points can be pinpointed by a single facility, insights can be funneled by the corporate team to various other facilities to target the next project.
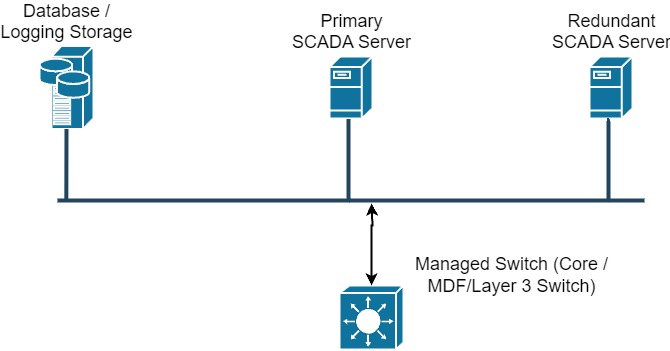
Compressor control case study
A prime example from one of Barry-Wehmiller Design Group’s clients’ factories where air compressors are confined to a small room with localized controls could serve as a noteworthy illustration of the challenges posed by isolated systems in manufacturing. Air compressors, crucial for supplying compressed air to the entire plant, are placed in a small room with a local control system isolated from the external world.
These large bedroom-sized compressors are typically monitored locally and the manufacturing process eventually starts experiencing quality issues. Could the suboptimal operation of the air compressors, due to their isolated controls, be adversely affecting the manufacturing process and causing an unreliable air supply? Is there a connection between the performance of these compressors and the overall performance of the manufacturing process?
If these compressors were integrated into a central SCADA system combining utilities data and control with the manufacturing process, plant professionals could have analyzed plant and line performance along with compressor performance. This data-driven analysis on logged points would have enabled the optimization of compressor performance, the balancing of supply and, if needed, modification of production for optimal system operation with the compressors. Achieving such dynamic optimization is not possible if the building utility system is not tied in with the manufacturing process control system.
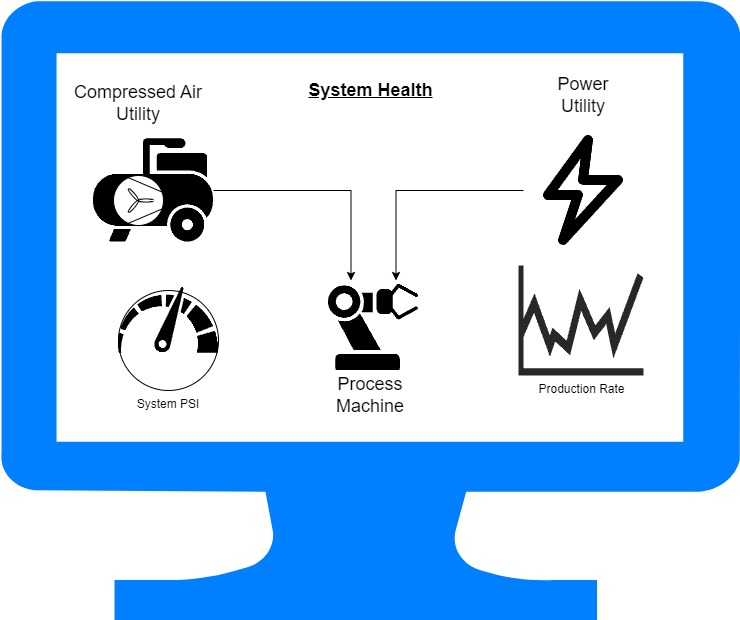
Long-term planning
In the evolving realm of manufacturing, harmonizing the controls between both the building utilities systems and manufacturing processes is not just a technological modernization — it’s a strategic imperative. It enables a holistic view of the health of plants, enabling business owners to navigate complexities with foresight, agility, insight and efficiency.
The future of the industry lies in the seamless orchestration of building utilities and process controls. Establishing a long-term plan for network, SCADA and OT/IT convergence can help keep an organization on track to achieve this operational synergy.
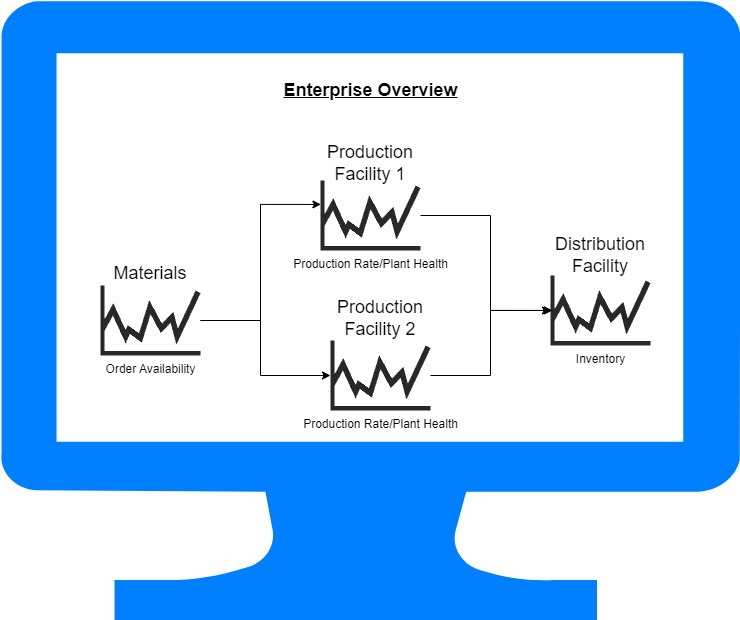
Glossary
The industry is full of specialized terms and phrases.
-
Building management system (BMS): A combined software and hardware system that enables control of building infrastructure and collection/visualization of associated plant data.
-
Direct digital controls (DDC): A system that uses digital devices to monitor and control building mechanical and electrical systems.
-
Enterprise resource planning (ERP): A software system that helps businesses coordinate activities including finance and operations such as manufacturing.
-
Flat network: A network where all components fall under the same broadcast area.
-
High availability: A server setup that enables quick recovery to another server.
-
Human-machine interface (HMI): A user interface, typically a touch screen used for interfacing with plant machines and devices (common for both SCADA and BMS).
-
Industry 4.0: Fourth industrial revolution, characterized by the integration of smart technologies like internet of things and artificial intelligence to enhance automation and efficiency in manufacturing.
-
Information technology (IT): In this article it specifically refers to business side software that sits on a network separate from the plant network.
-
Operational technology (OT): In this article these are network or computer components that are on a plant-side or manufacturing network. Think of OT as plant floor/SCADA and IT as business systems.
-
Programmable logic controller (PLC): Used to control manufacturing and building automation equipment.
-
Supervisory control and data acquisition (SCADA): A combined software and hardware system that enables control of plant equipment and collection/visualization of associated plant data.