A brief overview of establishing and maintaining a robust fall protection program for facilities, plants, warehouses, job sites and more.
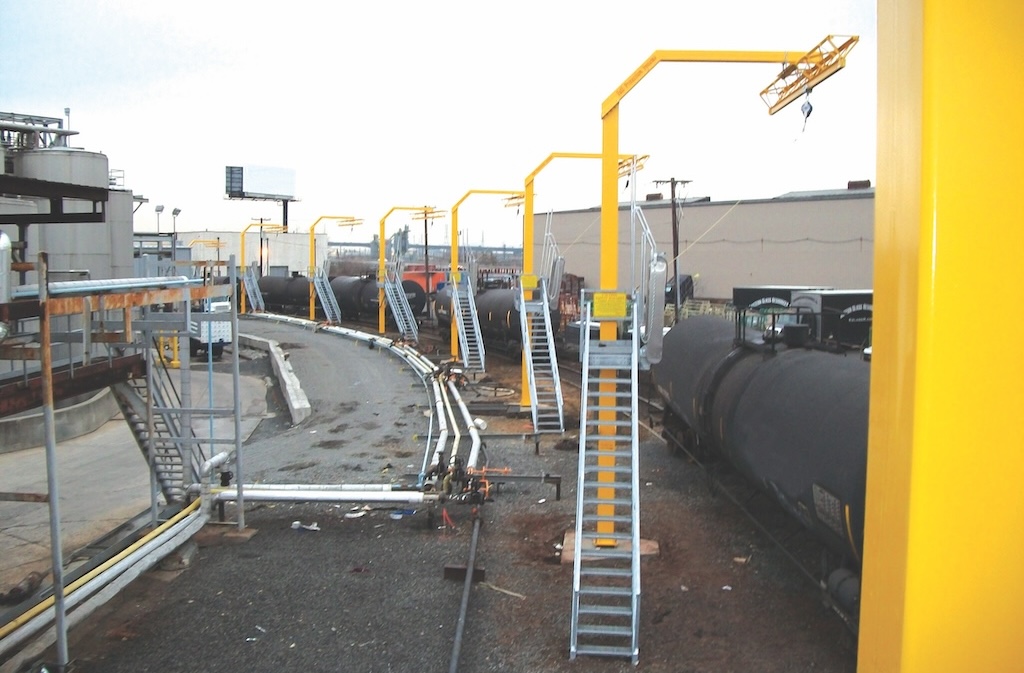
Fall protection and worker safety insights
- Maintenance technicians are essential for facility operations, requiring proper fall protection due to high injury risks. OSHA mandates protection for falls over four feet to prevent accidents.
- Implementing effective fall protection involves hazard assessments, solution evaluation, and regular training. Compliance reduces fall incidents, mitigating costs and enhancing worker safety.
Maintenance technicians are the backbone of any facility — be it treatment plants, manufacturing sites, warehouses or equipment maintenance shops. They keep the lights shining and the machines running. If a facility runs like a well-oiled machine, it’s because maintenance technicians are the ones oiling it. This why it is important to ensure workers are protected from falls when maintenance tasks require employees to work at heights.
Falls continue to be a leading cause of injuries and fatalities in the workplace every year. OSHA requires employers in general industries to provide fall protection if a worker is subject to a fall of four feet or more. Selecting the best fall protection solution to protect a worker is half the battle, and ensuring user compliance is the other half.
If solutions seem to be too cumbersome or require too much effort, workers may neglect their fall protection equipment and become exposed to unnecessary risks. This article will discuss some tips & best practices in establishing, maintaining and supporting a robust fall protection program that can apply to almost any facility.
Conducting fall hazard assessments
One of the first steps in establishing a fall protection program should be identifying all the potential slip, trip, and fall hazards in the facility. While fall protection is required when a worker is exposed to a fall of four feet or more, it should be noted a fall from any height can lead to debilitating injuries. Make note of the navigation paths used and be sure they are clear of holes or other tripping hazards.
It is recommended to survey the facility with at least one maintenance technician so they can convey what work needs to be done, how frequently tasks are performed, what risks are present and what safety measures are being used — if any. This process can be tedious, but it gives the surveyor a clear picture of how work is being performed in the facility and what improvements can be made to ensure worker safety is prioritized.
Identifying and evaluating fall protection solutions
Not all fall protection measures are created equal. The Hierarchy of Fall Protection controls offers a rubric when selecting which fall protection method is the most effective and the most feasible for the application. The hierarchy goes as follows:
-
Hazard elimination
-
Fall prevention
-
Active travel restraint
-
Active fall arrest
-
Administrative controls.
Eliminating a hazard is always superior to mitigating a hazard. As one goes down the hierarchy, the solutions offered will increase the risk of a fall occurring despite the consequences of the fall being mitigated. That is not to say that solutions lower in the hierarchy are less safe for the worker, but the increased risk does increase the chance of injury or fatality occurring.
Budget concerns are too often cited as one of the stronger arguments against the feasibility of solutions. However, understanding the financial facts and figures involved if a fall incident occurs can be a good counter to those arguments. According to the Bureau of Labor Statistics, the typical fall incident (without adequate fall protection) costs $50,000 in direct costs. Indirect costs, such as decreased productivity due to poor morale, loss of business due to damaged reputation and employee turnover can amount to up to four times the amount of direct costs.
Improve personnel training
Another way to increase worker safety & compliance is to regularly train workers. OSHA mandates that employers must designate any employee who will use fall protection equipment as an authorized user. Those users must be trained on the proper care, inspection, storage and use of equipment before initial use. OSHA also specifies a few scenarios where retraining is necessary.
One such circumstance is when changes in the workplace render previous training obsolete. This could happen if a company purchases new fall protection equipment or identifies a new fall hazard in the facility. Another is when inadequacies in an employee’s knowledge indicate they no longer have the understanding or skill necessary to safely perform their work at heights. Perhaps the employee was found to be neglecting their daily pre-use inspection or using a connection device rated for overhead use only while attached to a foot-level anchorage. If the employer feels there is a gap in understanding of the employee’s capability to comply with the fall protection program or OSHA code, retraining is necessary and should be conducted as soon as possible.
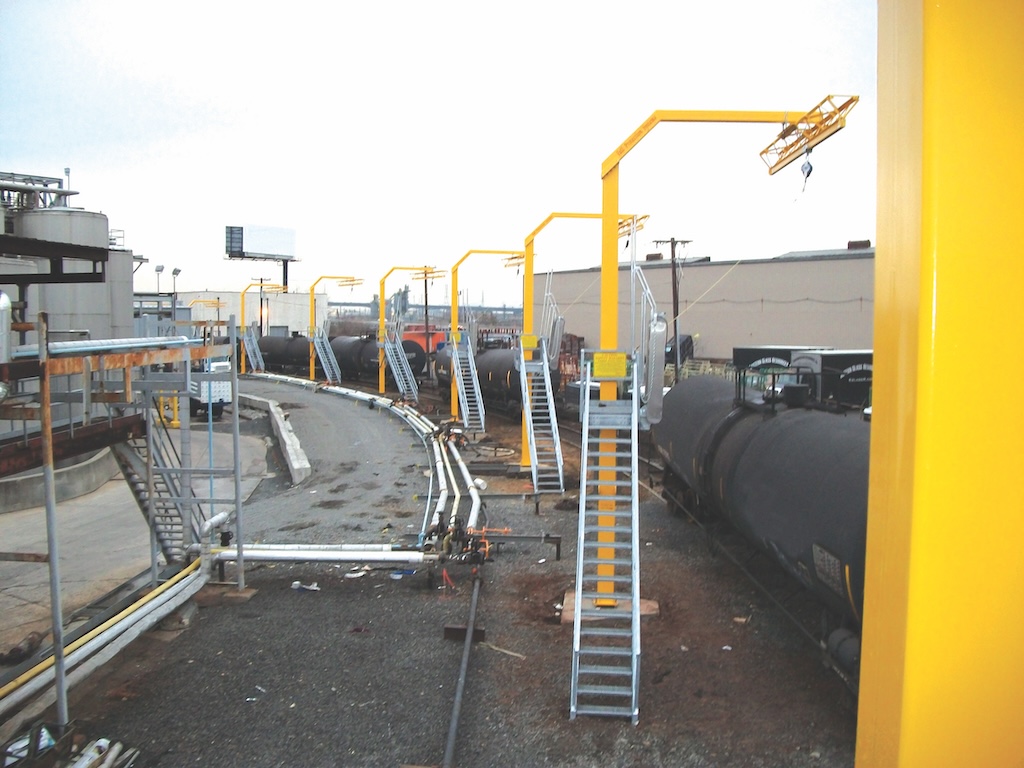
Fixed ladder safety
Portable ladder use is common and fall protection is not often required when using them. However, fixed ladders are also common in many facilities and often utilized as exterior roof access points, and a recent OSHA update will require new fall protection equipment for many fixed ladders. An update to the OSHA 1910.28 Walking Working Surface standard that took effect in 2018 now mandates all fixed ladders 24 ft or greater to have a permanent fall protection system installed (except in California, where this rule applies to ladders 20 ft or greater). The ladder cages commonly associated with fixed ladders are not now considered illegal, but they are no longer considered adequate fall protection either.
This new rule mandates that ladders installed before November 2018 must be retrofitted with a permanent fall protection system or ladder safety system by November 2036. However, if there is any maintenance, repair and/or construction performed to an eligible ladder before 2036, OSHA states the retrofit must occur at that time.
Reducing fall protection issues in the facility
Fall protection violations are a continuous leader on OSHA’s Annual Top Ten Citations report each year, which indicates many organizations still struggle with proper implementation and compliance.
Maintaining a robust fall protection program in any facility will not come without its challenges. However, there are now more manufacturer and vendor partners than ever that eagerly want to get involved with organizations looking to enhance their safety programs.
With standard updates, new product releases/discontinuations and the process of integrating the next generation of workers, it can be daunting for any individual safety manager to keep up with all these changes. Connect with peer industry groups, lean on safety distributors and never be afraid to seek support when it’s needed. Don’t go at it alone.