Choosing the right lubricant can have a significant impact on reducing energy and labor and equipment costs for a company and save money long-term.
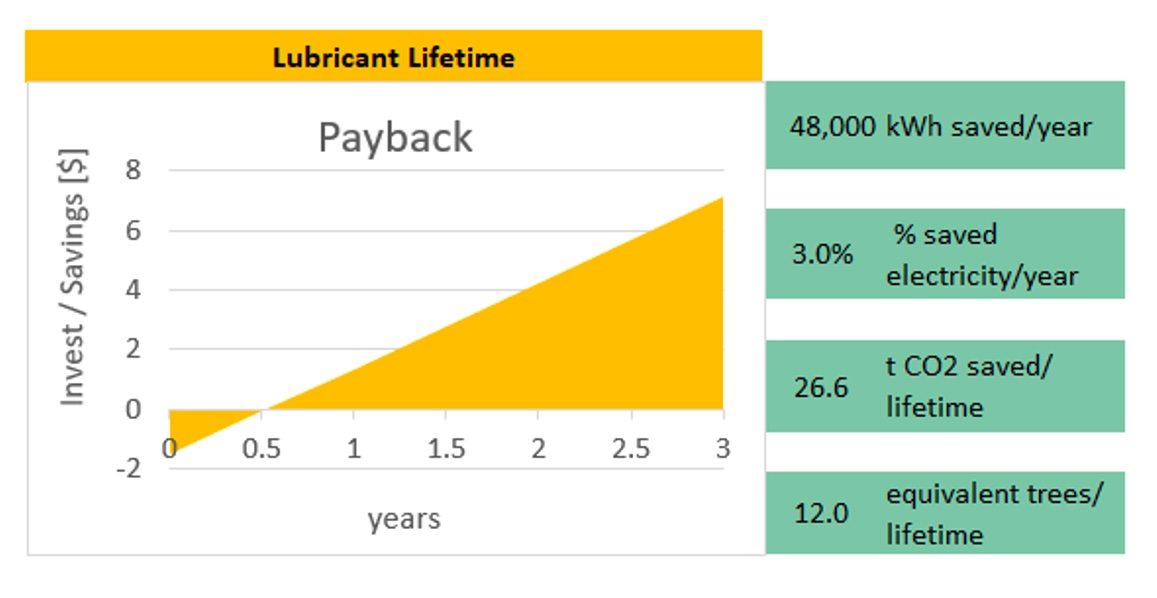
Learning Objectives
- Understand the role lubrication plays in keeping machinery well-run and efficient.
- Understand how choosing the right lubricant for a facility or operation can affect the bottom line and reduce overall costs
Lubrication insights
- The lubricants a company chooses can have a significant impact on high-visibility and high-value line items such as energy, labor and equipment costs.
- Avoid the pitfalls of purchasing lubricants based solely on price by evaluating the current program and requesting a comparative cost benefit analysis from the potential supplier.
The right lubricant is more important to a company’s bottom line than most realize. Because lubricants typically make up only 1% of a company’s total operating costs, many lubrication programs do not receive the attention they deserve. However, the surprising truth is the lubricants a company chooses can have a significant impact on high-visibility and high-value line items such as energy, labor and equipment costs.
Price versus cost
Identifying the true cost of a lubricant program is the first step in optimizing the plant to positively impact the bottom line. When analyzing the current lubrication program, consider how much lubricant is being used, how often lubrication occurs and how much time it takes. Another factor lubricants impact is the consumption of energy depending on their coefficient of friction. Proper physical lubricant management also will ensure the lubricant is in optimum condition for service.
If this isn’t part of the process, companies should take some time to establish a baseline so it’s easier to conduct an “apples to apples” comparison when considering alternative products. By tracking these variables, companies will realize the true cost of their lubrication program includes much more than the price per kilo or price per liter.
The next step is evaluating where savings are possible, which involves several key factors.
Increased productivity is the name of the game
Facilities are constantly pushed to increase productivity while reducing maintenance and operating expenses. Productivity is lost when equipment is idle. While some maintenance, including lubrication, can be completed while the line is in operation, some has to be conducted during downtime. This is not a huge inconvenience if the regularly scheduled downtime coincides with the relubrication schedule.
However, if companies have to bring a machine down once a shift specifically to relubricate, that’s money taken away from the bottom line every shift. What if companies were using a lubricant that extended that relubrication interval to once a month? Consider, for example, a manufacturing facility in the food and beverage industry running nine lines, with a total operating time of 8,000 hours per year. Their current bearing lubricant requires re-lubing once a week. Using a specialty synthetic lubricant their relubrication interval could be extended to once a month. This not only saves time, but also reduces consumption.
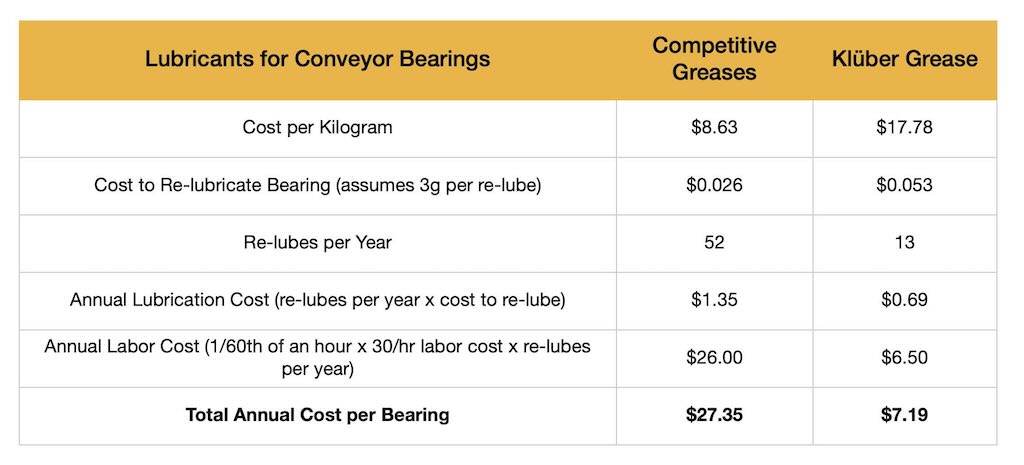
Reducing maintenance costs and operating expenses
Most plants often have a wish list of maintenance projects waiting for the manpower and time to get them done. While even the best lubricant can’t create time, an optimized lubrication program can free up resources to accomplish those tasks.
If a lubrication specialist is able to extend relubrication intervals through the use of synthetic, newer generation products, companies can do more with the same staff and with the same time. In one case study, the facility had the potential of reallocating almost 1,500 man-hours annually. Imagine what could be accomplished in that time.
Used-lubricant disposal is also a variable in calculating the costs of a lubrication program. Extended lubrication intervals impact these figures. If less lubricant is being used, then less is being disposed, which is another savings to the bottom line. Don’t forget spare parts inventory. Proper lubrication can help machinery and its components last longer which means less money spent on repairs or rebuilds. Equipment is a major investment and should be maintained accordingly.
More opportunities on savings are on components that are difficult-to-reach or that require equipment shut down for lubrication routines, such as chains, open gears and manually lubricated bearings. Additional labor reduction and improved equipment reliability can be achieved when single point lubricators (also known as SPL or autolubers) are installed to replace manual lubrication. SPLs change frequent manual relubrication activities and possible equipment shutdown, by extended lubrication service supported by quick visual inspections. Optimum results are obtained when the best lubricant for the application is combined with the right SPL for that application.
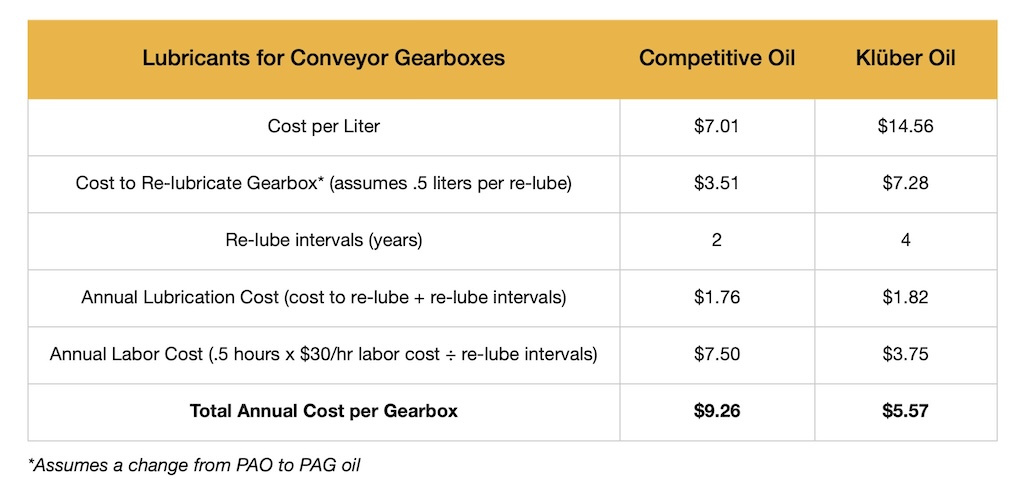
Another factor, many companies fail to consider is how much energy a company can save by utilizing highly efficient gear oils or compressor lubricants, among other applications. The right lubricant can reduce the coefficient of friction and present improved viscosity-temperature behavior, resulting in reduced power loss. The right lubricant equals less required energy, leaving companies with a lower energy bill at the end of the month.
By using a properly selected high-performance lubricant, the savings in energy can have payback period of a few months. Furthermore, savings in energy and lubricant consumption, contribute to a more sustainable operation and reduction of the carbon print of the facility. All of which serves the bottom line.
Performing a lubricant change focused to save energy (or energy efficiency) is a streamlined process. It starts by measuring the energy consumption of a machine for a period and estimating the energy savings potential. After the oil has been changed a new measurement is performed for a similar period and compared to the original conditions.
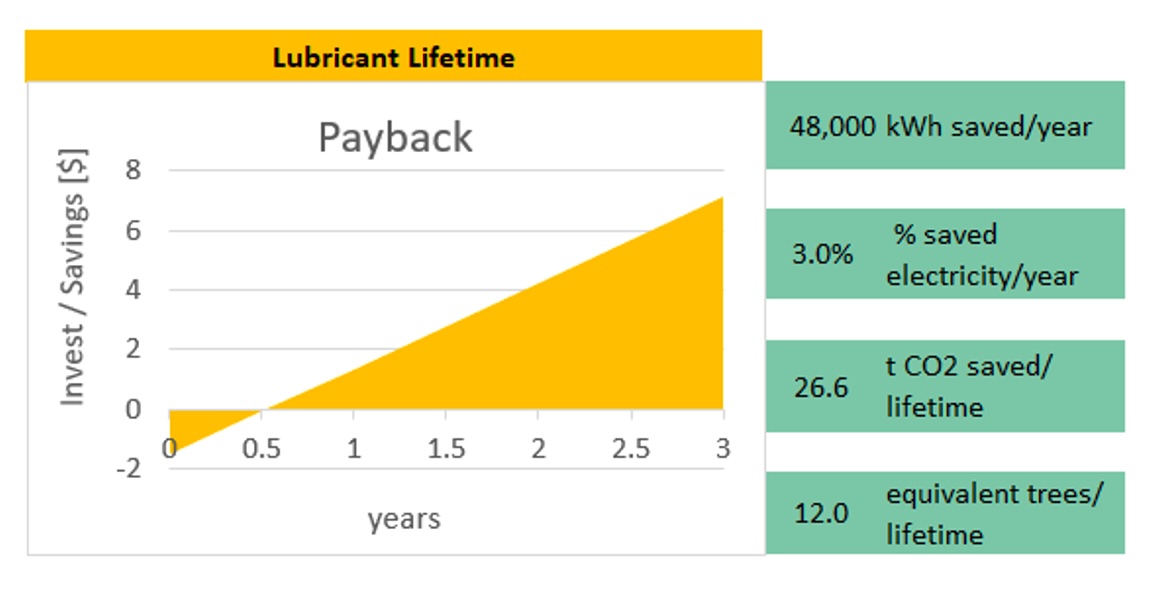
The difference is calculated considering equipment load. Below is an example of a case study of energy savings and payback period resulting of replacing a conventional oil with a fully synthetic lubricant in the gearbox of a cement mill. This principle is applicable to other machines in diverse industries.
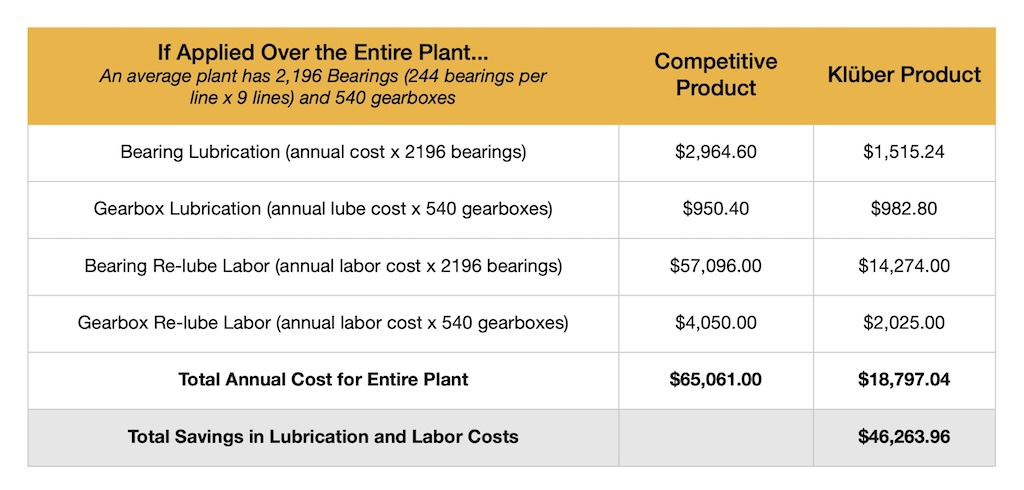
Lubricants on the production line affect the bottom line
In order to avoid the pitfalls of purchasing lubricants based solely on price, evaluate the current program and then request a comparative cost benefit analysis from a potential supplier. Simple calculations can reveal significant savings that aren’t always evident in the initial cost of a lubricant. The numbers tell the story.