Sometimes the problem is too many options
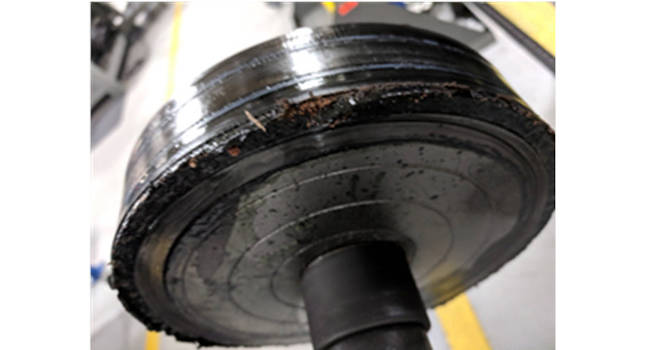
Although the world is focused on going all-electric, most applications will still be better served by fluid power cylinders. Whether hydraulic or pneumatic, fluid power cylinders offer benefits such as power density, shock tolerance, structural flexibility and application simplicity, to name just a few. In this article, we will discover how choosing the right fluid power cylinder can add value to your design.
Although pneumatic systems are in some respects simpler, they are generally incapable of achieving the transfer of higher loads and forces. Hydraulic cylinders have the advantage of smoother, more controllable movement as they are devoid of the spring-like action associated with gaseous media. As an added benefit, hydraulic systems can perform ancillary functions such as lubricating and cooling.
However, since the availability of power and media is a non-negotiable factor in fluid power system design, it should be noted that a properly designed and sized pneumatic system can achieve higher performance where a compact footprint is not required.
Considerations when specifying a cylinder
Specifying hydraulic cylinders is essentially a balancing act as each design factor influences one or more of the many other design considerations.
Although NFPA standards and ISO-compliant guidelines are a great starting point for hydraulic system design, many industries have guidelines of their own. Working with a cylinder manufacturer experienced with all these standards can expedite the design process.
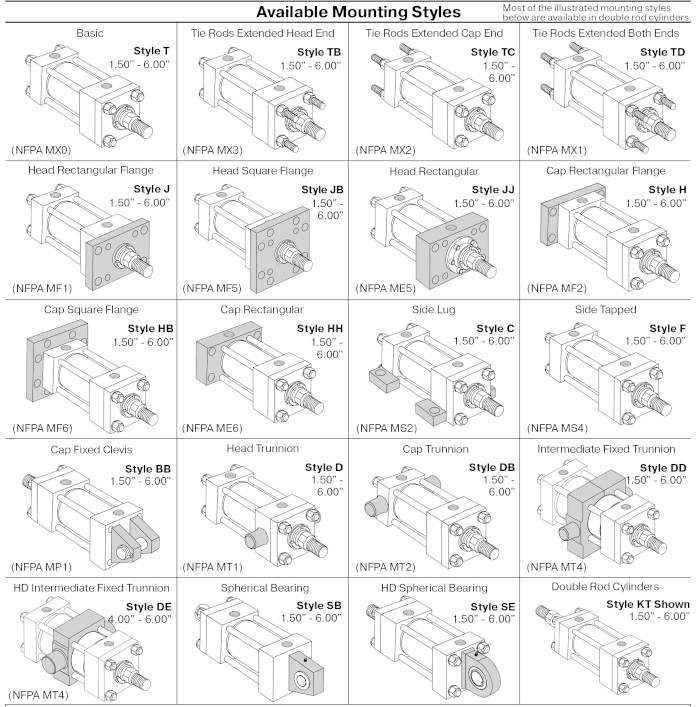
Cylinder manufacturers can offer a range of options capable of achieving the widest scope of performance requirements which increase the likelihood that standard components will meet the design criteria of an application. The major factors to consider when specifying hydraulic cylinders include:
- Capacity: Medium-duty systems account for most of industrial applications and are typically at 1000 PSI. Standard heavy-duty hydraulic cylinders are capable of handling pressures as high as 3000 PSI, which are typically required for hydraulic presses, automobile manufacturing applications and other related industrial applications.
- Stroking distance requirements: Although stroke distances longer than 10 feet (3.05m) are possible, pressure rating can be a concern. An appropriate minimum rod diameter would need to be determined to handle the load.
- Speed: Standard hydraulic cylinder seals can easily handle speeds up to 3.28 feet (1 meter) per second. The tolerance threshold for standard cushions is roughly two thirds (2/3) of that speed. Typically, low-friction seals are the better choice for higher speed applications.
- Temperature: Hydraulic cylinder systems using standard components can be designed to meet application temperatures as hot as 500°F (260°C) or as cold as -65°F (-54°C). Applications requiring temperature extremes at either end or both ends of the temperature spectrum require extensive knowledge of the interdependency of individual components to achieve the best balance of short- and long-term performance expectations.
- Mounting styles: There are three types: 1) fixed mounts that absorb force along the centerline of a cylinder, 2) fixed mounts that do not absorb force along the centerline, and 3) pivot mounts that absorb a load in a curved path.
- Cylinder bore size: Bore size is related to operating pressure. The required push or pull force at a known pressure determines the necessary area and, subsequently, bore size.
- Piston rod size: Design engineers probably request customization of piston rod sizes more frequently than any other hydraulic cylinder component. Always remember to consider that push or pull is never independent of stroke length when determining piston rod size.
- Cylinder configurations: For applications requiring equal pressure on both sides of the piston, a standard double-acting cylinder configuration using pressure to extend and retract the cylinder, combined with a standard four-way directional control valve to direct pressure to either the head or the end cap, is almost always preferable to more customized solutions.
- Rod ends/rod threading: Standard threads can be made in inch or metric format. Customized rod ends are possible but rarely needed or warranted, due to delays, expense, and the inability to readily mate with standard accessories.
- Cylinder body tube: Standard cylinder bodies are plain steel (some with chrome plating on the inside) and will be able to handle the majority of applications. The use of corrosion-resistant materials, such as stainless steel or bronze, is common in special applications like a water-type environment.
- Stop tubing: Stop tubing is generally used to lengthen the distance between the rod bearing and the piston bearing in order to reduce bearing load on push-stroke cylinders when the cylinder is fully extended. Stop tubing is especially critical for horizontally mounted cylinders where it helps to restrict the extended position of the rod.
- Seals: Experienced hydraulic system manufacturers will offer seals to meet a complete range of temperatures and fluid types and can help guide an engineer’s specification to meet precise application requirements.
More to consider
Every industrial application is unique, and there are many additional factors involved in hydraulic cylinder specifications. Energy-absorbing cushions, pillow block bearings, regenerative circuits, over- or under-sizing ports — all these and more contribute to optimizing the performance of hydraulic systems, depending on each application’s specific performance requirements.
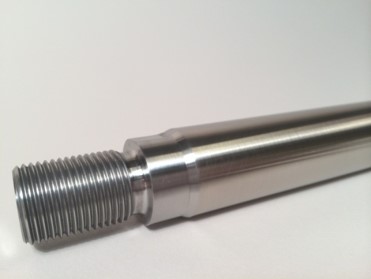
As with the specification of more fundamental components, selecting appropriate ancillary features can present a specification challenge. For example, cushions are intended to retard motion at end of stroke, but engineers sometimes overlook the fact that loads may be not moving very fast anyway and may not require such redundancy in their systems.
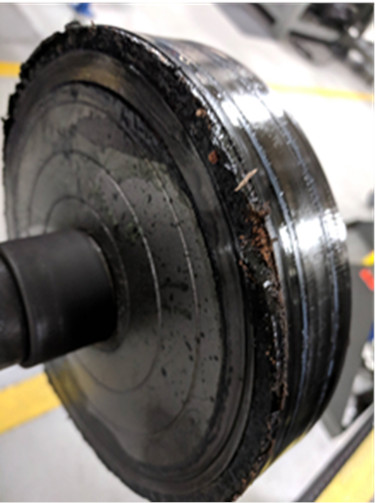
There are certainly applications for which specifying the right cylinder for the right duty requires some customization in component size, material type or configuration. However, far more often than not, partnering with an experienced hydraulic system solution manufacturer early in the design process will save the engineering team significant time and money, while ensuring the system does its assigned duties as efficiently as possible for as long as possible.