Many organizations are looking to modernization a flexible power system and approach maintenance for their power systems to improve sustainability and efficiency
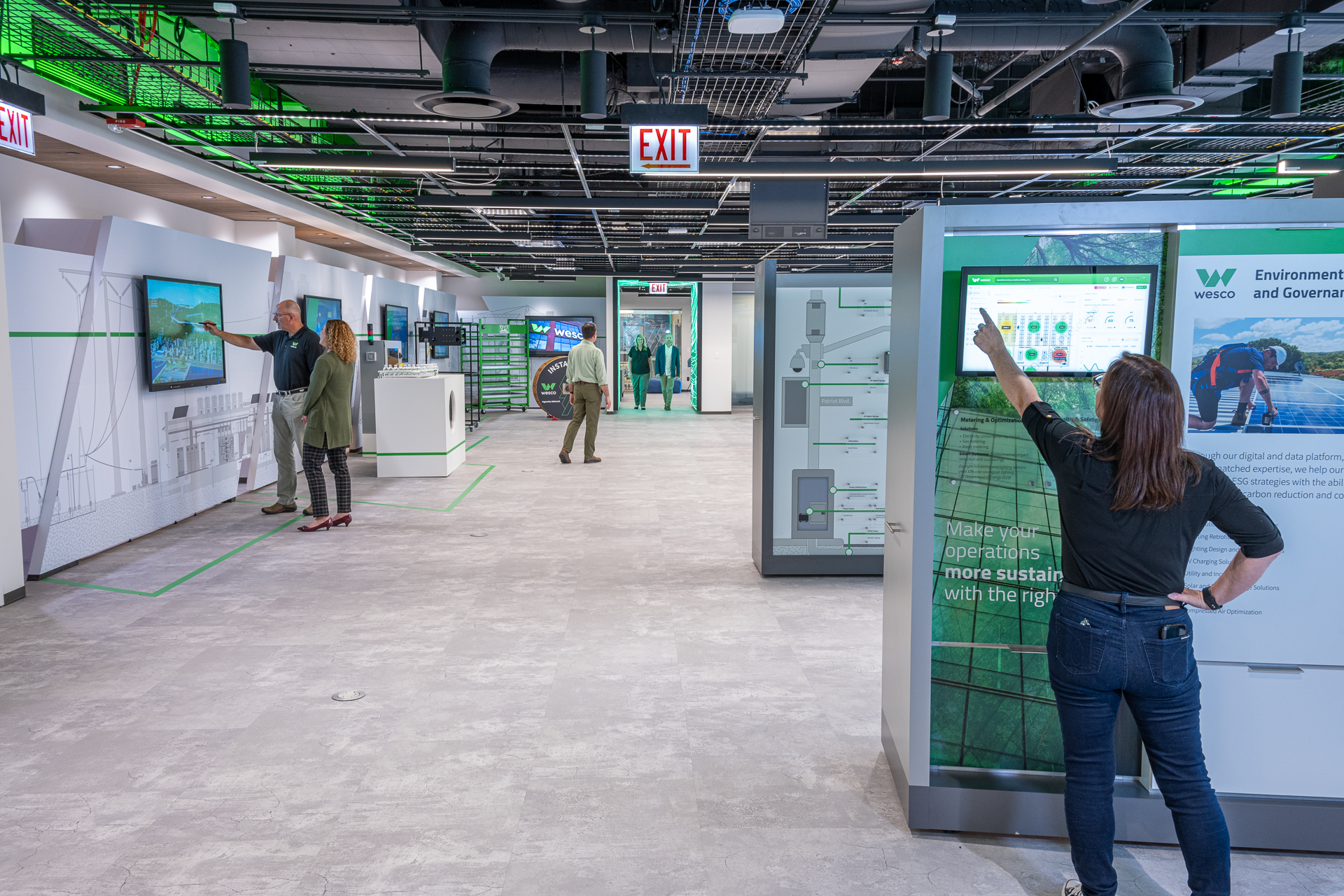
Learning Objectives
-
- Learn about the changing dynamics and needs for electrical and power systems for manufacturers.
- Learn about the techniques companies can use to get the most out of their electrical and power systems.
- Learn where to start and how modernization can help manufacturers get the most out of their systems.
Electrical and power insights
- In modern manufacturing, predictive maintenance and smart metering are essential for minimizing downtime and improving equipment effectiveness, ensuring reliable power supply and operational continuity.
- Switchgear modernization extends the lifespan of electrical systems, balancing safety, cost-effectiveness and compliance with evolving regulations, crucial for sustaining efficient manufacturing processes.
In today’s manufacturing environment, every operator is looking to enhance overall equipment effectiveness (OEE), drive productivity and avoid downtime. As the evolution of “smart” factories gains momentum, the ability to supply power to machines and systems — some old, some new — puts a much-needed emphasis on the electrical distribution systems already in place.
Many organizations, who also are trying to improve their sustainability efforts, are taking a fresh look at how to best create a flexible power system and approach maintenance for those systems.
Old equipment, new equipment and the smart factory
From low voltage to medium and high voltage, it’s fair to say many legacy power and electrical systems are nearing the end of life. This wasn’t much of a problem because these systems were one-dimensional machines that ran until they could not perform any longer. Then they were replaced.
Operators no longer have that luxury. As budgets have shrunk, businesses can’t afford to replace new equipment — they need to prolong the operating lifecycle for as long as possible. The downtime caused by a failure in the power system can have serious business ramifications. And as power systems have become “smart”, interconnected and microchip driven, waiting for failure is not an option. Instead organizations need to anticipate and address problems before they become an issue so they can improve the efficiency of power systems.
Getting the most out of electrical, power systems while minimizing downtime
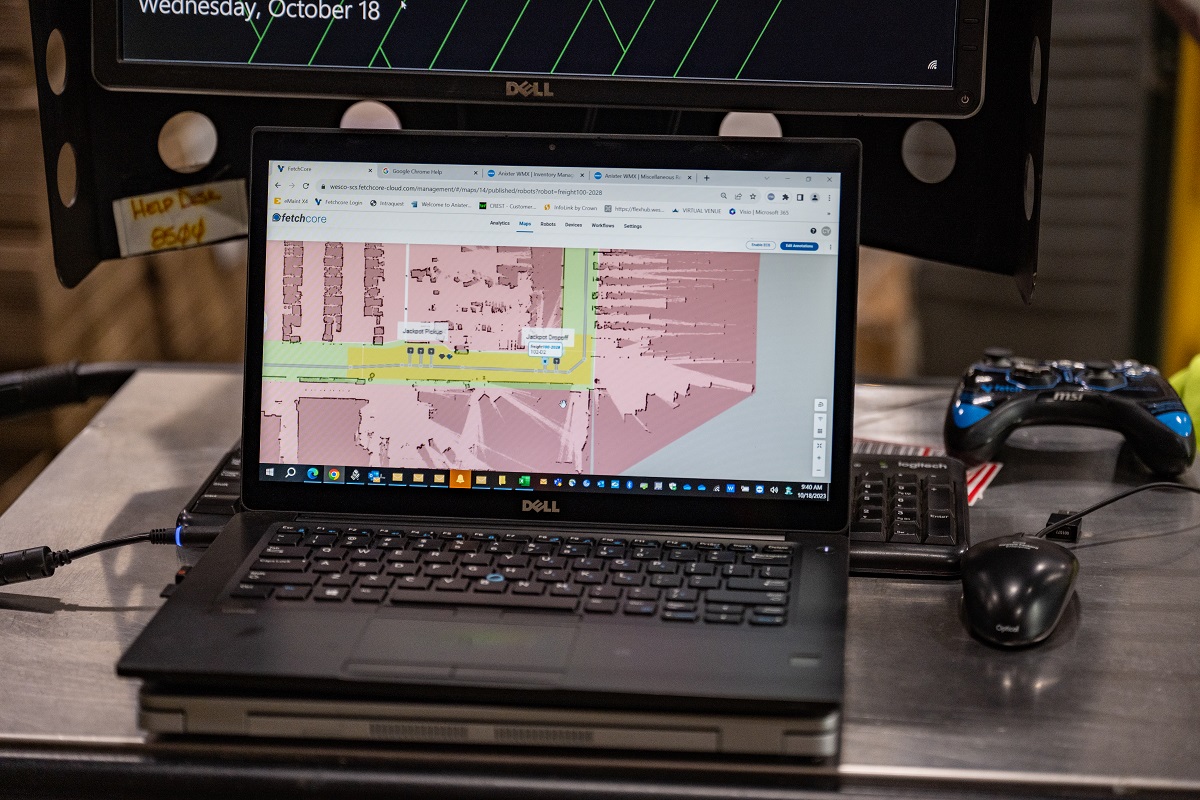
Consider it this way: Companies no longer have the luxury of fixing the plane while it’s in the hangar. Now they have to fix it while it’s in the air. This is a challenge because there are many moving parts, each piece dependent on the other and any one failure can be catastrophic. Even if systems and machines operate properly, companies still need to ensure constant, reliable access to power.
For plant managers, staying on top of these nuances can be complex and overwhelming. Individual components do more than ever, which requires plant employees to make sure they are on top of the ins and outs and working as intended.
It used to be if a component overheated and something tripped, it might take time to identify where and what went wrong. Now, several technologies can help plant managers stay on top of these challenges and address them before they impact operations.
• Predictive maintenance: By leveraging sensors, internet of things (IoT) devices and advanced analytics, plant engineers can get deep insights into how different machines or components are operating. These technologies can flag potential indicators that a machine may need service or maintenance, allowing workers to address issues before they become larger problems. For example, vibration sensors can send alerts when a machine is beginning to operate outside normal parameters. Engineers can then replace or fix any components before a catastrophic failure occurs.
• Smart metering: Smart metering is another example of a proactive shift in managing electrical power and distribution systems. Smart meters can show energy usage is near real time, allowing plant engineers can identify how and when power is being consumed. Manufacturers can in turn leverage power consumption outside of peak times to create a much more sustainable flow of power. They also can detect power outages quicker — and automatically alert utility providers when they occur. This is critical, because when the power goes out, minutes matter. Every minute of production lost due to a power outage can cost tens — if not hundreds —of thousands of dollars.
• Renewables and microgrids: Aging grid infrastructure and a rise in catastrophic storms have made these an attractive solution for companies that need guaranteed, uninterruptible power. Battery storage systems, solar panels and other renewables can not only help with sustainability goals, it also can ensure businesses still have access to power if the grid fails. As an added bonus, businesses can save money by generating their own power and selling it back to the utility.
Factoring in safety, standards considerations
It’s important not to forget about safety when thinking about maintenance for power and electrical systems. According to the Electrical Safety Foundation (ESF), contact with or exposure to electricity is one of the leading causes of workplace injuries and fatalities in the U.S. While many newer machines and power systems have enhanced safety capabilities, it’s also vital to have safety standards in place, especially when it comes to maintaining electrical equipment or components.
In 2023, NFPA 70B: Standard for Electrical Equipment Maintenance, which addresses electrical equipment maintenance, was moved from a recommended practice to a standard. Standards are recognized, mandatory rules of technology that strive to provide safety for all involved. At a high level, NFPA 70B sets maintenance guidelines and schedules for electrical equipment based on the type of equipment, its age and/or condition and how critical that equipment is for operations. While more rules can be frustrating, the pros outweigh any cons. A properly maintained piece of equipment is safer, less likely to fail and more likely to operate effectively.
These rules can provide benefits across the entire manufacturing process but perhaps most critically create an environment of trust. Trust the right processes, procedures and tools are being deployed across the plant floor.
Starting with switchgear modernization
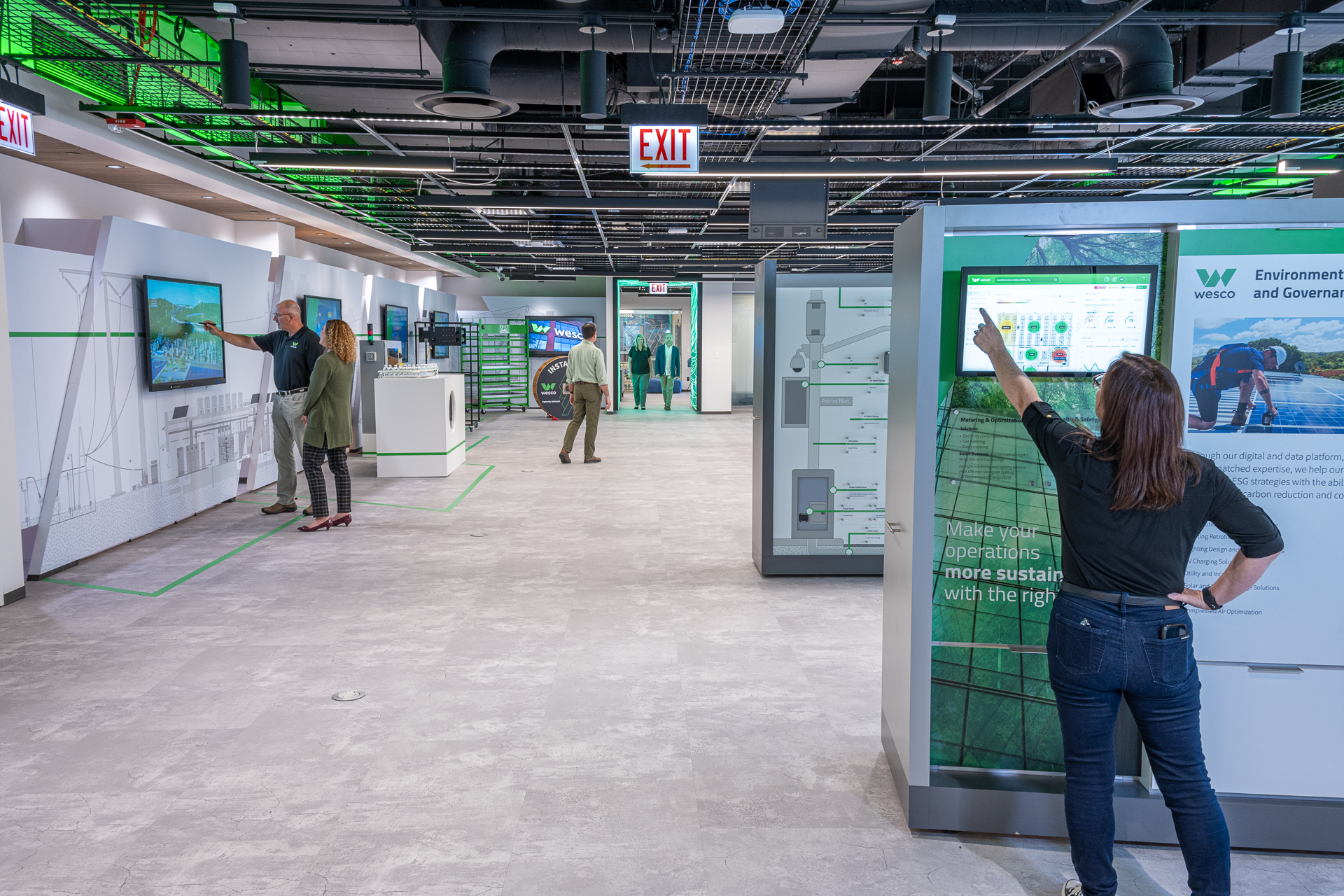
While an organization’s need often vary, many often start with their switchgear, as these systems are vital to safety and operational success. Many switchgear systems are designed to last for decades, but as they age, they become more vulnerable to failure. Completely replacing switchgear generally requires a significant capital investment, which is where modernization and life-extension solutions come in.
At a high level, this process converts a legacy system to a more modern platform without needing to replace it. Switchgear modernization can be a cost-effective way to extend the useful life of the facility’s electrical equipment. The original infrastructure can often be kept in place — including the existing conduit and cabling.
This solution improves OEE and overall safety while requiring less downtime than a complete equipment replacement.
Filling in the gaps with modernization
When it comes to modernization, industrial facility managers need to keep up with best practices to ensure OEE and compliance with the latest regulations. From electrical safety programs to low-voltage communications to cutting-edge industrial IoT (IIoT) applications, the nuances of electrical power systems are vast.
While the number of potential solutions are vast, navigating them and understanding which ones are right isn’t always easy. That’s why it’s important to have trusted partners in place. With the right partner, manufacturers can take a fresh look at the systems, machines and processes they have, identify potential maintenance gaps and ensure that their power delivery systems operate effectively. If new solutions are needed, the right partner can help companies identify what would best fit their specific business needs. They also can address concerns to ensure worker safety and maintain a competitive edge.