Many factors can impact how proper use can avoid friction.
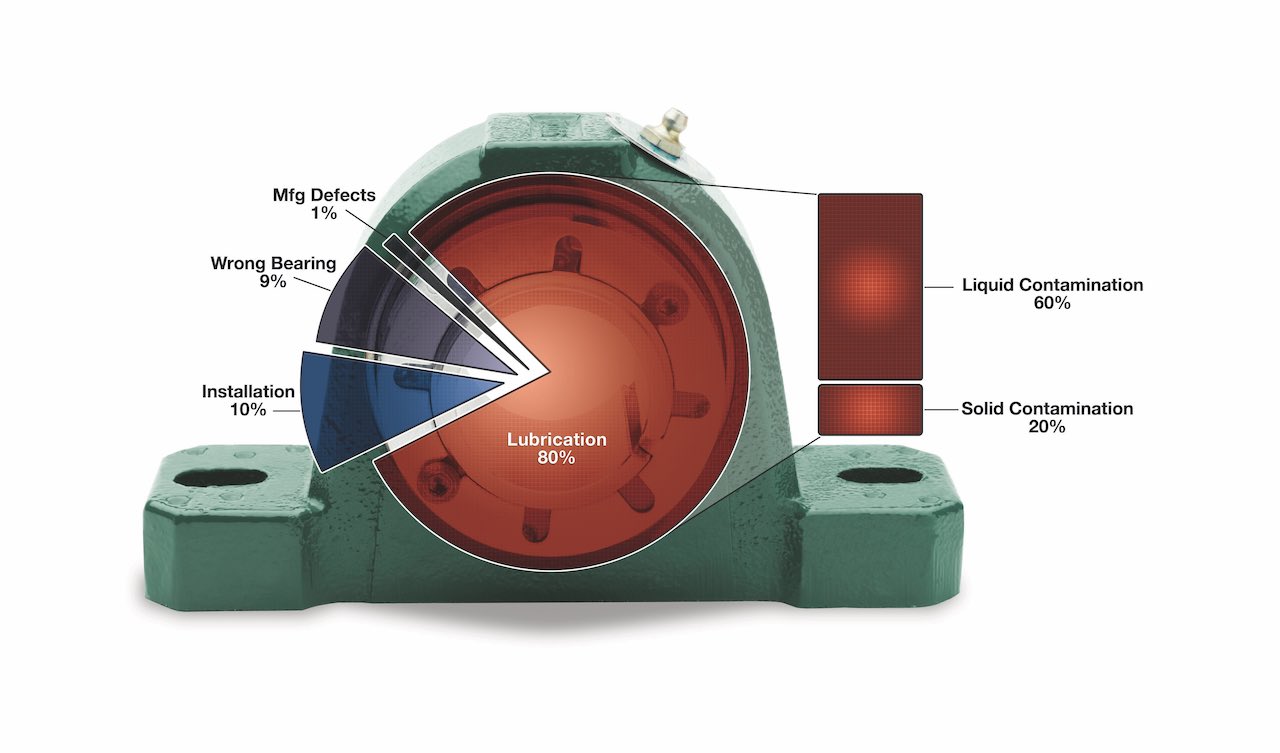
Proper lubrication is the factor that has the largest impact on bearing life. It is commonly believed in the industry that at least 80% of bearing failures are related to lubrication and contamination issues. Lubricants minimize wear, prevent corrosion and reduce heat. Lubricants are made up of several components and can be mineral or synthetic.
Grease lubrication is used in most rolling bearing applications. Grease is a combination of a thickener and base oil. The oil type can be mineral or synthetic. When used, grease clings to the internal bearing components, releasing or bleeding oil onto the moving components. In grease lubrication, oil is still providing the critical lubrication function. The thickener is just the media holding the oil.
In grease lubricated bearings, oil bleeds from the thickener onto the moving components. During use, the oil properties will fade and need to be replenished. This is referred to as the grease service life (GSL). Many factors such as speed, operating temperature, loading and environmental conditions affect the GSL. Replenishing grease intervals should be sufficient so that new grease is added to the bearing before the GSL. If the intervals are too long, the film thickness will break down, causing bearing wear and damage.
When bearings are regreased initially, the new grease charge will cause a temperature increase because the new grease adds some drag to the bearing. This is temporary, and bearing temperatures typically return to normal levels. At low to moderate speeds, bearings may be 100% packed with grease as an added measure to prevent the ingress of contamination. However, in applications where bearing speeds are high, the drag and friction associated with too much grease can cause a runaway temperature condition and cause the bearing to fail. The amount of grease added at each interval should be evaluated based on the desired function of the grease.
Greases are formulated to operate in a wide array of applications. Varying types of thickeners, oils and additives are blended to produce a grease with the desired performance criteria. Not all greases can be mixed together. If two incompatible greases are mixed with each other, the thickeners can react chemically and turn into a hard cakey solid with no lubricating properties. If a change in grease is required, the original grease may need to be removed completely from the bearing before introducing a new grease. Bearing and lubricant manufacturers can assist in determining if two greases are safe to use with each other.
The issue of viscosity
Viscosity is the most important property of oil. Viscosity is the thickness of the oil, or the oil’s resistance to flow and shear. An oil’s molecular structure determines its viscosity. Oils with higher viscosities have larger molecules. Mineral oils are distilled from petroleum and contain natural molecules that vary in size and structure. The average size of these molecules determines the oil viscosity. As mineral oils age, their molecules change in size and shape, reducing the viscosity over the service life of the oil. In synthetic oils, the molecules are artificially made, making them very consistent in size and shape due to the manufacturing process. Synthetic oils offer superior lubricating properties over mineral oils and can tolerate significantly higher operating temperatures. Other attributes include resistance to oxidation and thermal breakdown resulting in longer oil life. Oils with lower viscosity ratings are thin, and flow through bearings and pump equipment more easily than thicker oils. Where heavier oils are used to support heavy loads, they also add drag to rotating equipment.
Choosing an oil with the correct viscosity for an application is very important. The film thickness has to be sufficient at the actual operating temperature to separate the metal surfaces and support the bearing loads. Since oil viscosity decreases with increased temperatures, the initial film thickness has to be thicker at startup to allow for this decrease in viscosity. At higher bearing speeds, a thick oil will increase drag and may not be pulled through the loaded zone on the bearing. Choosing the correct viscosity for cold or hot temperatures and high shaft speeds is a must. Bearing and oil manufacturers can determine oil viscosities for a specific application.
Understanding friction
The main purpose of lubrication in bearings is to separate metal surfaces, support loads, and eliminate or minimize wear. By developing a layer of oil between the rollers and raceways, oil actually can separate the moving components, fully supporting the bearing loads and preventing wear. In addition to viscosity, the surface finish of internal bearing components plays a critical role regarding lubrication and wear.
When viewed under a microscope, the finely ground surfaces of raceways have peaks or high points referred to as asperities. Ideally, an oil film separates moving components and prevents these surfaces from contacting each other. In reality, varying degrees of separation occur depending on bearing types, oil viscosity, loads and speeds. They are referred to as boundary friction, mixed friction and fluid friction.
In boundary or thin film lubrication, the film thickness is not sufficient to separate metal surfaces and metal to metal contact occurs. Loads are supported by the surface asperities rather than the oil film. Friction is at its highest level, resulting in wear, heat and premature failure. Some special designs, such as journal bearings, are designed to operate within a boundary film type of lubrication. As the journal rotates against a softer material, the softer asperities break off and react with oil and heat to form a protective film layer that supports the loads and significantly reduces wear. This type of bearing is limited regarding loads and speeds. For roller bearings, boundary film lubrication must be avoided.
In fluid film friction, the two surfaces are separated completely. The film thickness is sufficient to prevent metal to metal contact, and fully supports the bearing load. In hydrodynamic lubrication, the actions of the rotating components pull oil into the load area between the rollers and races, maintaining the film thickness. This type of bearing will experience wear only when stopped or started.
In mixed lubrication, the two surfaces are supported by the fluid film thickness, but slight contact between surfaces asperities occur. In elastohydrodynamic lubrication, actions of the rolling elements pull oil into the contact area between the roller and raceway. The contact area between rollers and raceways is typically very small due to the dissimilar geometries of the two bodies. As oil is pulled through this area and pressures get extremely high, causing the oil viscosity to increase. The forces exerted in this area cause the two bodies to deform elastically and create a linear or parallel area where the oil flows through, creating separation and supporting bearing loads.
When properly lubricated, rolling bearings operate within elastohydrodynamic film lubrication, but due to high loading conditions, they also fall into mixed boundary friction, meaning there is slight contact with surface asperities. In time, this slight wearing will cause the bearing to spall and fail. This type of failure defines a bearing’s L10 life. Due to many variables, developing and maintaining an elastohydrodynamic condition in rolling bearings can be a challenging task.
Oil and contamination
Moisture and solid particle contamination is a major contributor to oil/bearing failures. When solid particulates mix with the oil, they will be pulled in the load zone of the bearing. The high pressures and loads will drive the particles into the races, causing pitting and eventually spalling. Moisture absorbed by oil will cause the oil viscosity to deteriorate, severely affecting the oil’s ability to separate and lubricate.
Bearings used in environments exposed to significant contamination or moisture may require frequent grease intervals to clean and maintain the quality of the oil in the bearing. Measures also can be taken to protect the seals of the bearing from exposure to contamination and water. Any type of grease fitting should be cleaned before attaching a grease gun. If present, dirt or sand can be pushed through the fitting as new grease is added.
When equipment is idled for extended periods, the bearings may remain stationary during this down time. After operating, the bearing internals typically will be coated with a thin film layer which can evaporate over time, providing minimal protection against corrosion. If the lubricant contains any type of moisture, the races may experience corrosion, specifically between the contact areas between the rollers and races.
Any time equipment is shut down for long periods, pack the bearings 100% full with new grease. This provides clean oil at its full film thickness to prevent corrosion. It also is advisable to rotate the bearings periodically to redistribute the oil within the bearing.
Determining a lubrication schedule for bearings depends on many factors, and each application has its own set of demands. Understanding that lubrication is used to flush or clean bearings, prevent corrosion or possibly remove heat is critical in determining an adequate lubrication regime. Bearing and lubricant manufacturers can assist customers with these recommendations.