Honeywell study touts better understanding of eye wash safety solutions
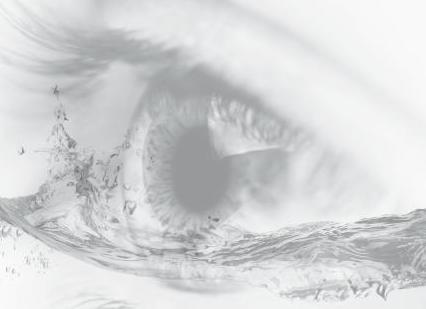
In its recently-released whitepaper, Honeywell Safety Products announced the results of a comprehensive study on eye wash safety practices and procedures in the event of an accident. The paper also looked at industry awareness on the subject of eye wash safety, including the prevailing American National Standards Institute’s (ANSI) standards (ANSI Z358.1).
Plant Engineering discussed the study’s finding and the issues around eye wash safety with Kelly Piotti, senior product manager for emergency eyewash, Honeywell Safety Products.
PE: Leaving aside the ANSI standard for a moment, what’s the No. 1 mistake manufacturers make when it comes to eye care?
Piotti: The No. 1 mistake manufacturers make is having insufficient eyewash—either the wrong type for the hazard or too few stations within a plant.
PE: How much of the issue of eye wash safety is top-down management, and how much is peer-to-peer enforcement? What are the challenges in each one?
Piotti: It is a little of both. Sometimes emergency eyewash is overlooked due to cost constraints, and that’s a top-down problem. Other times it is due to a lack of understanding of the standard, either at the top or among peers. For instance, some safety managers feel that if they have one station per a certain number of square feet then they are in compliance. In reality, the number of stations should be based on the number of hazards located in the area and the distance between each hazard and an eyewash station.
Eyewash must be located within a 10-second walk from the hazard with no obstructions, including stairs. In each case, a basic understanding of the safety standard is the key to promoting proper eyewash implementation, and it’s extremely easy to meet compliance with today’s variety of portable stations.
PE: Beyond strategies, the Honeywell whitepaper cites a difference in the eye wash solutions themselves. What are some of the things to be aware of when working with different eyewash solutions?
Piotti: The first step to safe flushing is to ensure you are using an FDA-approved product that meets all good manufacturing processes for ophthalmic use. Saline is manufactured for many different purposes, [and] when it comes to the eyes you want to make sure it meets ophthalmic standards. This will aid in a faster recovery and ensure there are no additional complications, such as those caused by contaminants or harsh flushing conditions.
Another type of flushing fluid to be aware of [is] those claiming to neutralize chemicals. Safety managers should be aware of the types of chemicals they are intended to neutralize, as the fluid could adversely react if used to treat eyes injured with chemicals beyond their intended use.