Critical process often goes overlooked, underappreciated.
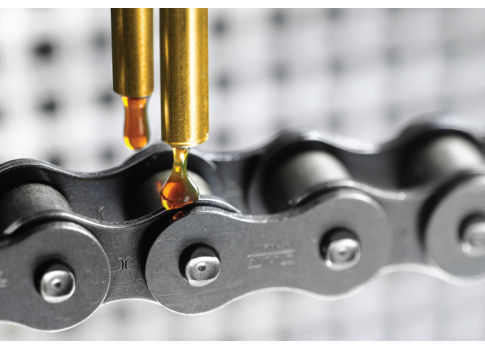
Plant engineers often fail to incorporate correct lubrication into system processes and do not realize its critical importance until something goes wrong. Lubrication is frequently one of the last things considered for project budgets when, in reality, it is one of the most crucial aspects to a system’s lasting functionality and integrity. Despite this fact, the lubrication process is commonly regarded as less important and overlooked when designing a system.
While this may seem like a simple oversight on the part of many plant engineering professionals, it is in actuality a widespread cultural norm to neglect and look down upon the lubrication process. This unfortunate situation often results in malfunctions that could have been avoided given a regular maintenance schedule and the willingness of plant managers to address the lubrication process correctly and to value the stability and reliability it brings to a system.
Lubrication is so integral to the success of so many plant processes that it is difficult to imagine it being overlooked, but the reality is that many have developed the habit of not placing this valuable process on their priority list for scheduled maintenance.
Below are several issues that negatively impact this culture of lubrication in industrial applications. These issues concern the industrial field as a whole as well as individual plant employees and managers. If improvements are made in each of these areas, plant managers can expect their process failure rate to drop significantly, their employees to have higher job satisfaction and their budget projections to be more accurate due to a lack of unforeseen maintenance requirements caused by inadequate lubrication.
Complacency
Lubrication has been referred to as a “guerilla trade”— it is sometimes perceived as mysterious, can conjure unpleasant sights and smells in the imagination, and is not a welcome topic of conversation for some. This is one reason that it is not properly addressed on a regular basis. This attitude of complacency has been adopted by many and has caused a lack of knowledge among industry professionals regarding the importance of lubrication, proper methods, procedures and having dedicated personnel.
A common result of this widespread attitude of complacency is the lubrication system often being the first thing to be blamed when a system malfunctions. Because many do not understand the workings of the lubrication system, they are not educated enough to make an informed judgement on what may have actually gone wrong with the system components. Their inclination is to blame the aspect of the process that is the most undesirable or about which the least is known; which in most cases is the lubrication system.
Additionally, in terms of regular maintenance, lubrication is often one of the lowest priorities despite playing what is arguably the biggest role in terms of overall system functionality. This, again, is due to this culture of complacency that exists toward lubrication.
Take for instance the hydroelectric dam in Folsom, Cal. that utilizes large, bearing-operated spill gates to maintain its reservoir. On July 17, 1995, the hydroelectric plant was temporarily shut down so the flow of the nearby American River could be maintained using a spill gate on the dam. As the gate was being opened, the axis point seized due to excessive friction, causing the load to be redistributed and the entire spill gate to buckle under the stress. As a result of this failure, nearly 40% of Folsom Lake was released towards San Francisco Bay, even causing some salmon and striped bass to incorrectly change their migration patterns.
An investigation later revealed a number of ways that the dam’s engineers had ignored their responsibility to properly lubricate the bearings prior to the failure. First, the maintenance staff had considered implementing a new lubrication system five years before the failure but later decided against it. Had they put this new system in place, the spill gate failure most likely would not have occurred.
Records also uncovered after the incident showed that the regular maintenance and lubrication schedule was steadily decreased throughout the life of the dam due to budget limitations, causing the bearings to slowly fall out of repair. Finally, the plant maintenance team did not use the correct lubricant in the first place, choosing to use a lubricant that was insufficiently water-resistant and that allowed water to enter the bearings and cause corrosion which eventually led to the spill gate failure.
Several conclusions about dam maintenance in general can be drawn from this example, but in terms of the culture of lubrication, the message is clear. The engineers responsible for the operation of this dam did not consider lubrication to be an important part of the spill gates’ ability to function. They were complacent in implementing a regular schedule of maintenance and lubrication and were ignorant of the correct type of lubrication to use, a combination which resulted in a massive system failure.
Lack of employee appreciation
Lubrication technicians are tasked with climbing into the dark, dirty places within plants that must be accessed and lubricated in order to keep all of the systems properly functioning. Their job, essentially, is to keep the machines going using a combination of knowledge, expertise and resources provided to them by their employers. In turn, employers are tasked with respecting the opinions of the technicians when it comes to lubrication requirements and not disregarding or ignoring their recommendations.
Providing insight and advice is an important aspect of a lubrication technician’s services for a plant, as companies often have false information on lubrication applications and the technician may be the only one with the training to provide the correct solution.
The previous paragraph is a depiction of a healthy relationship between an employer and a lubrication technician—one that is unfortunately not always realistic. What lubrication professionals often experience is a lack of respect and appreciation. This lack of employee appreciation towards lubrication technicians has negatively impacted the culture of lubrication throughout the industrial world for some time.
Exclusion from budget
As an extension of their attitude of complacency, plant managers will often completely overlook lubrication requirements when planning their budgets. Despite owning multi-million dollar machines that rely on regular lubrication to function, there are companies that do not even consider this requirement in their list of necessities for plant operation. This can lead to catastrophic results including the loss of millions of dollars in equipment, time and plant output.
When considering lubrication, plant engineers need to recognize the importance of the process and place it just as high on their list of priorities as other essential system processes. The cultural perception of lubrication as dirty and unnecessary needs to change, starting with the individual, in order for plants to ultimately operate at a higher level of efficiency and productivity.
Kevin Smay serves as technical specialist, lubrication applications & systems for Valin Corporation. He has more than 25 years of experience in the lubrication system application industry.