Find the right application to match the motor need and know the conditions for using a variable frequency drive (VFD).
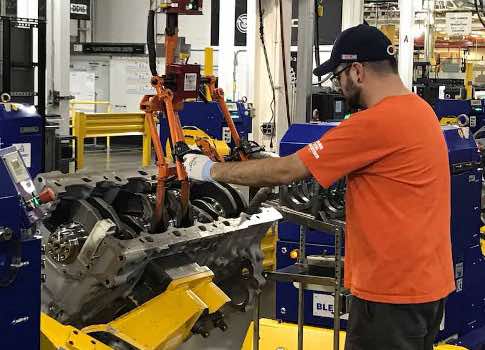
Inside of plants today, ac motors are becoming the industry standard. Many plants are shifting to ac motors from hydraulic motors and in some cases dc motors when powering heavy loads, which were more popular in the past. This shift can be attributed to a variety of reasons and most have to do with cost. AC motors are more compact and require less maintenance than a hydraulic motor or a dc motor with brushes. Couple this with the more expensive hardware associated with a hydraulic motor, and it is apparent why more plant managers are moving to ac motors inside of their operation.
With cost being a driving factor, operators need to have more precise control over the ac motor. They need to be able to optimize its use so that there is not unnecessary, wasted energy. It is important to understand the practical applications of a variable frequency drive (VFD) to an ac motor.
Among the questions to be asked:
- When is a VFD beneficial?
- Under what conditions should a VFD be used?
- What’s the difference between a VFD and a soft starter?
Understanding the answers to these questions will maximize the use and minimize the cost of operating an ac motor in a plant setting.
Full voltage starters, soft starters, and VFDs
There are several ways to power and control an ac motor. In addition to a VFD, one could alternatively apply a full voltage starter or a soft starter. The most basic motor control involves utilizing a full voltage starter. With this approach, full voltage is applied to the motor and it ramps up to maximum speed as quickly as it can.
The problem operators run into with a full voltage starter is the inrush of current can be up to seven times the full load current of the motor. For a very short period of time, a very high in rush of current is applied to the motor and its control components. If a large motor needs to do a frequent amount of starting and stopping, it can wear out equipment faster and be a costly burden on the facility’s utilities.
In contrast, a soft starter eliminates this burden by reducing the load and torque output to the motor. This approach allows the motor to ramp up at a speed that is determined by a setting on the soft starter itself. An operator can set a specific ramp-up time, and from the time it is turned on to the time designated, the motor runs at full speed. This allows reduced current inrush, reducing the risk of premature failure and additional burden on the facility’s utilities. Soft starters are ideal for applications where speed ramping and torque control are critical components, and in piping systems where fluid changes speed rapidly to avoid pressure surges.
A VFD takes this concept a step further by allowing the operator to always control the inrush current and the speed of the motor. The VFD can control the motor both during the start/stop cycle and throughout its runtime. A VFD is necessary where complete speed control is required and a key concern is energy consumption. A soft starter will be the less expensive option, but in large horsepower situations, savings can be realized over time with a VFD.
Basic VFD applications
Flow control is one of the most common applications of a VFD inside of a plant setting. The ability to change the speed of a pump to control flow is paramount. System conditions will often require a reduced flow rate. Dampers and valves often are used to accomplish this reduction, but this strategy does not help energy conservation. Conversely, a VFD can control flow rate while at the same time optimizing the energy required to do so.
There may be a situation where an operator needs to run the motor at less than maximum speed at certain times of the day, but then crank it up faster at other times. This is the real driver with the popularity of VFDs in today’s environment: saving energy and reducing operational costs. If an operator is simply looking to run an ac motor at a constant speed that is less than the motor’s full speed rating, a gearbox can be used. However, if an application is such that it is a variable torque load, a VFD is a fitting solution.
On a very basic level, for example, imagine an ac motor is used to run a fan on a cooling tower. The faster the operator wants the fan to run, the more horsepower and energy it will require. Due to the external environment shifting throughout the day, temperatures may cool. Because of this, perhaps the fan only needs to run at a speed that is less than what was required during a hotter part of the day. Costly energy is being wasted by running it at full speed when the task can be accomplished at a lower level.
Additional benefits
In addition to cost savings due to energy conservation, most VFDs will allow the operator to set different parameters to limit torque. This is done by limiting the output current on the motor. This desired outcome is completely driven by process. There is a need to protect whatever it is that the motor is driving, and many pieces of equipment in the plant setting have mechanical limitations. Because of this, exceeding these limits by over torqueing can lead to heavy damage or costly malfunction.
Most VFDs are manufactured to be extremely flexible so they can be configured to use the inputs and outputs (I/O) that are integrated into them. These I/O can be used for any number of different functions, including start/stop functionality, direction change, constant speed selection, macro selection, speed adjustment, etc. Additionally, VFDs’ analog outputs can be configured to provide feedback to the plant control system for parameters, including power consumption, actual speed, frequency, torque, etc. If a process changes, for example, and it now needs to be run at a different speed, the plant control system can adjust the signal to the drive’s designated speed input.
In the case of flow control, VFDs have evolved to the point where many of them can be integrated with a pump right out of the box using a pre-defined macro. In this case, a flow meter would connect directly to a drive’s analog input. An operator may adjust the desired flow remotely and the drive will maintain that flow by executing an internal PID loop. Some drives allow the operator to set up flow schedules and may also be set up to bring additional pumps online as demand requires.
A VFD’s built-in I/O is not the only way to control a drive. Many drives offer flexibility that allows for a variety of different communications protocols that can control the VFD from most manufacturers’ controllers. All standard protocols are available for most VFDs. This allows the operator to have bi-directional communications with one communications cable as opposed to multiple wires.
Why is this important? By utilizing a single cable, as opposed to multiple wires, installation costs are kept at a minimum and a much larger amount of data can be transmitted. This data does not just apply to advanced control, but monitoring as well. Typically, operators are looking to monitor the speed, torque, current, and temperature of the drive. Far more data can be communicated over this one cable than a VFD’s built-in I/O can accommodate. When a situation calls for multiple pieces of data, involving numerous I/O, many VFDs today can handle the requirement.
Finally, the maintenance benefits are a major part of the appeal of effectively utilizing a VFD for an ac motor in a plant’s operation. Maintenance costs can be lowered significantly due to reduced wear and tear on the equipment because of controlled starts. Additionally, in cases where applying a VFD to a motor eliminates the need for dampers and valves, the maintenance costs of those pieces of equipment can be eliminated as well.
VFDs are continuing to gain popularity in the industry as the different benefits they provide grow, most of which will be associated in one way or another with cost and energy savings.
Kevin Goodsell is an engineering manager at Valin Corporation.