Key factors may be underestimated or overlooked if an electrical engineer takes an overly narrow view of the project or makes unrealistic assumptions instead of doing thorough research. A holistic approach, on the contrary, considers four key strategies during the planning process.
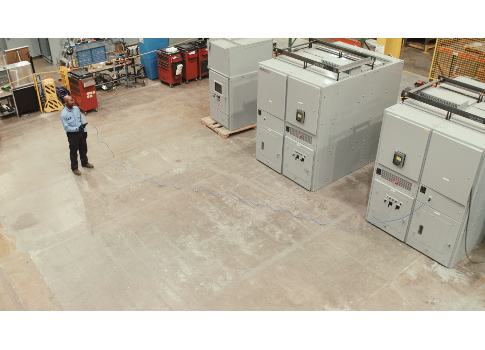
All projects, no matter the scope and objective, share certain key electrical challenges that can be addressed during the planning phase. In a new research and development facility requiring redundant power and emergency generation capacity for a small glass furnace, good planning will lead to having in place before it becomes a liability to the schedule. Another project with a different goal, such as fast-tracking an upgrade from an ungrounded Delta system to a grounded wye in a large manufacturing facility, can also be accomplished through careful pre-planning.
Effective planning starts with electrical engineers identifying safety and reliability requirements, including requirements for redundant power and emergency generation systems. Developing accurate load calculations is another part of the early phase. Taking these measures ensures budget adherence and enhances plant safety, reliability, and productivity. Yet, it is often surprisingly hard to capture the data required for effective project planning.
Key factors may be underestimated or overlooked if an electrical engineer takes an overly narrow view of the project or makes unrealistic assumptions instead of doing thorough research.
A holistic approach, on the contrary, considers four key strategies during the planning process:
- Reviewing and confirming electrical design, testing, and energy efficiency information
- Creating a simple and straightforward process flow diagram for estimating new project needs
- Knowing the goal of the project
- Being realistic about costs.
Review and verify
The ability to produce accurate and detailed information significantly contributes to the electrical engineer’s understanding and to the success of the project. The engineer should gather information such as an up-to-date single-line diagram of the power system, process control drawings, periodic system test records, and energy-monitoring data or electric bills.
Any discrepancies between the single-line diagram and the actual power system must be highlighted because changes resulting from renovations, expansions, upgrades, and maintenance may not have been revised on the original diagram. Verify the accuracy of the single-line diagram or have the electrical engineer perform a field inspection, especially if he or she has not recently worked with the company or at the specific plant.
An electrical engineer with a holistic perspective will also want to confer with the mechanical and process controls engineers for the project to get a wide-angle view of the project’s key characteristics.
Understanding the existing conditions is critical to planning any kind of addition or modification to a facility; and, while it can be tempting to rush this process, a solid baseline will help avoid costly and time-consuming changes later in the process. Make the early investment of due diligence during the planning phase to make life easier later in the process, where poor planning usually leaves its mark.
A simple process flow diagram
Ideally, the process and instrumentation diagram (P&ID) comes with a technical operational narrative that defines the precise needs of the system. The two documents are crucially important. Without accurate information, electrical engineers often default to oversizing the electrical system to avoid potential operational problems, such as a system that is incapable of starting a large motor.
Unnecessary oversizing wastes capital dollars. A properly sized electrical system balances capital cost with reliability, and achieving this balance requires judgments based on accurate information.
Unfortunately, some electrical engineers do not always seek clarification and confirmation of the design intent of the process as a whole. To design an optimal system, the electrical engineer should be asking questions to understand the process they are supporting. For example, if the process flow diagram shows two 50-hp pumps, a good electrical engineer proactively seeks to understand if both will be running at the same time or if one is a backup that will cycle on and off, using less power than the continuously running pump.
The sizing of the mechanical system and, in turn, of the electrical system has a considerable impact not only on the project’s capital cost, but also on operational costs and reliability. Motor starting requires six to eight times the amperage of the running load, and the power system must be sized to handle it. The total impact varies with the design of the mechanical system and its operating pattern just as it varies with the design of the electrical infrastructure.
For example, ten 10-hp motors or one 75-hp motor combined with one 25-hp each total 100 hp. However, the operational effect of starting a 10-hp motor is considerably less than that of starting a 75-hp motor. In this example, the electrical system would likely have to be larger (and more costly) for the 75-hp scenario than for the 10-hp scenario. The motor sizing and numbers would still be determined by the mechanical engineers and types of equipment needed, but the electrical engineer must know this detail to properly size the system. Simply noting the need for a 100-hp process load is not enough information.
Know the project goals
The project goal and operational model provide the context for the numbers from the facility calculations and contractor quotes.
While this seems obvious, the problem is that often the contractors, and sometimes even the engineers, focus more on the design maximums and how things are going to fit together than on the operational model. For example, if multiple production shifts will operate around the clock, 365 days of the year, the infrastructure must support more backup production equipment, emergency and standby equipment, and power to assure reliability.
Key considerations
The following are some key considerations that inform a cost-effective electrical design.
Load factor. How much equipment will run and how hard? For example, a 100-hp motor running continuously but only loaded during a portion of the time, never off, may be running at 120 amps fully loaded; or it might ramp down during non-peak production and run at 60 amps some of the time. If there are many of these motors, the load factor must be calculated because of the cumulative effect on the sizing of cables, transformers, and circuit breakers. If the plant has two 200-hp motors in one area that require upsizing the electrical system, then the equipment that feeds these motors must also be upsized. Following this strategy to its logical endpoint—the power substation—the entire electrical infrastructure may end up being larger and more expensive than originally thought.
Maintainability. The engineer has to know whether the line can be periodically shut down for maintenance or whether it must be running continuously. Will equipment troubleshooting and maintenance be performed by skilled staff or outsourced to a contractor? Some equipment requires more hands-on operating knowledge to monitor the multiple parameters that determine when to perform regular maintenance.
The knowledge needed includes hours of operation, load current, how hard it is being run, number of operations on a circuit breaker, etc. Some types of equipment are designed for many thousands of operations while other types require maintenance after a hundred. Equipment that needs more frequent maintenance may cost less upfront, but a more costly piece of equipment will reduce long-term maintenance costs.
Existing spare-parts inventory, training, and purchasing agreements. Using brand A rather than brand B equipment can generate significant capital savings. However, an existing plant may already have an extensive inventory of spare parts for brand B and a fully trained staff with considerable operating experience. Perhaps there is also a purchasing agreement for brand B. In the case of a plant addition, it may be a good value-based decision to select additional brand B equipment if it is comparable. However, one may come to the opposite conclusion for a greenfield project.
When an engineering firm has broad electrical engineering experience in a range of industries, the firm adds value in the form of a transfer of knowledge from one project to another. At the end of the day, an engineer with a holistic approach can offer perspectives that make a project successful and save the client time, trouble, and money.
A. Thomas Nestor, PE, is a senior engineer at SSOE Group, a global engineering, procurement, and construction management firm. He has more than 40 years of power engineering expertise, mostly in the glass industry, including his work as an engineer at three glass companies. He can be reached by at [email protected].