They can’t all be right, yet many of us may have used one of these rules (probably not the same one, either) with great success. Which one, if any, is correct? The answer depends on the application.
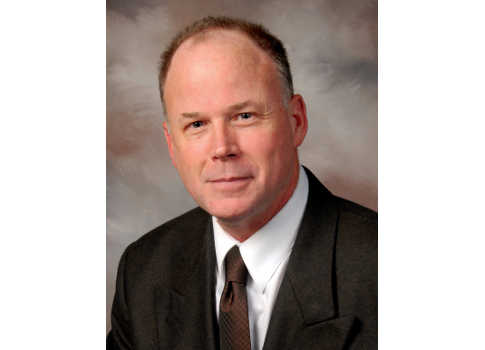
Note: Sleeve bearings are also known as babbitt bearings, white metal bearings, and plain bearings.
It’s fair to say that one’s outlook on life is colored by experience. A good example of this with sleeve bearing motors is the question, “What’s the proper clearance between a shaft and the sleeve bearing it rides in?” Chances are each of us has a rule of thumb for this, probably related to shaft diameter. Some of these may look familiar:
• One thousandth, plus 1 per in. of diameter
• Two thousandths, plus 1 per in. of diameter
• 0.0015 in. per in. of diameter
• 0.002 in. per in. of diameter.
Depends on application
They can’t all be right, yet many of us may have used one of these rules (probably not the same one, either!) with great success. Which one, if any, is correct? The answer depends on the application.
If your facility has slow-speed synchronous motors, you’ve probably seen some operating fine with more than twice the recommended clearance. Someone who works primarily with 2-pole petrochemical motors, however, knows they can vibrate when the bearing clearance is even slightly excessive.
One of the first questions to consider when looking at bearing clearance guidelines is whether the clearances are radial or diametral. The focus here is on diametral (total) clearance, because it can be determined by physically measuring the shaft and bearing diameters. Another reason to use diametral clearance: In operation, a horizontal machine rarely has the same radial clearance at the 12:00 and 6:00 o’clock positions.
Guidelines galore
To illustrate just how many different guidelines there are for this simple topic, I’ve combined the recommendations of five manufacturers and three other reputable sources into a single graph (see Figure 1).
The first thing to recognize here is that most horizontal electrical rotating machines use a cylindrical overshot bearing design, a term that describes the lubrication method (i.e., oil supplied by oil rings).
Considerations in sleeve bearing design
To understand why so many rules-of-thumb exist, it may help to review some basic design factors for sleeve bearing machines, starting with the relationship between power, torque and speed.
Torque (lb-ft) = hp x 5252 / rpm or Torque (N·m) = kW x 9550 / rpm
It follows that the higher the torque (lower speed and/or higher hp/kW rating), the larger the required shaft diameter, and the heavier the rotor, the bigger the bearing must be. Additionally, the faster the speed, the smaller the allowable journal diameter must be, and the longer the bearing, the greater the clearance required to get the oil out.
In order of importance, the major factors that influence sleeve bearing design therefore include:
• Weight to be supported
• Peripheral speed of shaft journal
• Viscosity of lubricant
• Operating temperature.
Designers of electrical rotating equipment generally keep sleeve bearing load pressure around 145 psi (1 Mpa), as compared to 580-725 psi (4-5 Mpa) for internal combustion engines. Some older motors used even lower bearing load pressure, so vintage machines sometimes have a larger bearing than modern motors with similar characteristics.
Excessive weight can distort soft babbitt, so bearing cross-sectional area increases proportional to the load. Higher hp/kW ratings mean more torque and hence require a larger shaft diameter. Peripheral speed increases with the rpm, or when the shaft diameter increases. For hydrostatic, cylindrical overshot bearings (the sleeve bearings most common to electrical machinery), the upper peripheral speed limit is approximately 6,000 ft (1,830 meters) per minute. Higher speeds require special designs, starting with 2-lobe, then 4-lobe bearings, as well as special lubrication methods (see Figure 2).
Sleeve bearing lubrication on most rotating electrical machinery is supplied by oil rings, which requires a minimum speed of around 25 to 30 ft (7.5-9 meters) per minute to deliver sufficient oil to the bearings. Be very cautious when an application (such as a VFD) significantly alters the original design. A force-lubrication system may be required, or even hydraulic jacking, to lift the shaft onto an oil film before starting.
When the peripheral speed limit restricts journal diameter, the designer must increase the length of the sleeve bearing. That brings us to the ratio of bearing length to diameter (L/d). For reasons of economy, the preference is for a 1:1 ratio–e.g., a bearing with a 3-in. bore diameter and 3-in. length.
There are drawbacks to a proportionally longer bearing. As the L/d ratio increases:
• Less oil flow exiting the bearing = higher bearing temperature
• Shaft deflection = diagonal contact with ends of bearing
• Longer machine = higher production costs.
The longer and heavier the rotor, or the more flexible the shaft, the more shaft deflection should be expected. Shaft deflection may force the designer to increase the clearance between the sleeve bearing and journal. Longer bearings also require longer shaft journals, which in turn require longer bearing brackets and larger machines.
The viscosity of the oil is less of a factor than the supported weight and peripheral speed, although one the designer must consider. The OEM manual specifies the recommended oils for the machine so, unless bearing design modifications have occurred, it’s usually best to stick with the recommended lubricants. Sometimes, a 2-pole machine may benefit from a lower viscosity oil, but such changes should only be made in consultation with the OEM or service center and even then with caution.
Vertical machines: Why are they different?
To begin with, on a vertical machine the same spindly shaft and heavy rotor does not cause shaft deflection as it would on a horizontal machine. While the shaft rests on the bottom of a horizontal bearing, it hangs more-or-less centered in the vertical thrust bearing, so there’s no radial sag to worry about.
In addition, guide bearings for vertical sleeve bearing machines are not the cylindrical overshot design, so they require much less clearance than bearings on horizontal machines with similar journal diameters. As long as there is sufficient radial clearance for the oil film, the vertical guide bearing needs no additional clearance. Contact the OEM or your service center for guidance.
Labyrinth seals
For labyrinth seals, the best rule of thumb is that clearance should be a little more than the bearing clearance. The closer the seal is to the shaft, the better it will seal. Of course, if it touches the shaft both may be damaged, typically resulting in rapid increases in temperature and vibration levels (especially axially on the end that is rubbing). Rather than determining labyrinth seal clearance from the shaft diameter, it’s better to work from the sleeve bearing clearance. A good guideline that several manufacturers use is 0.002 – 0.004 in. (0.05 to 0.10 mm), with more radial clearance than the bearing. Obviously for a given shaft diameter, the labyrinth seal clearance for a vertical machine can be set closer than for a comparable horizontal machine.
Conclusion
There are lots of sleeve bearing clearance tables in circulation, some of which are for specific types of motors–e.g., low-speed synchronous motors–and should never be applied universally. In broad terms, several principles apply:
• Low-speed motors can operate with more clearance
• Longer bearings require more clearance
• Vertical sleeve bearings require less clearance
• Hermetic motor sleeve bearings require tighter clearance
• Labyrinth seals should be as close as possible, without contacting the shaft.
About those rules of thumb: If you’ve had good success with one rule for the motors in your plant, watch out for different types of sleeve bearing machines. Examples would include 2-pole versus low-speed machines, a significantly different length/diameter ratio, or vertical machines. In those cases, contact the manufacturer or your service center for help.
Chuck Yung is a senior technical support specialist at the Electrical Apparatus Service Association (EASA). EASA is a CFE Media content partner.