A manufacturer can have safety and productivity at the same time.
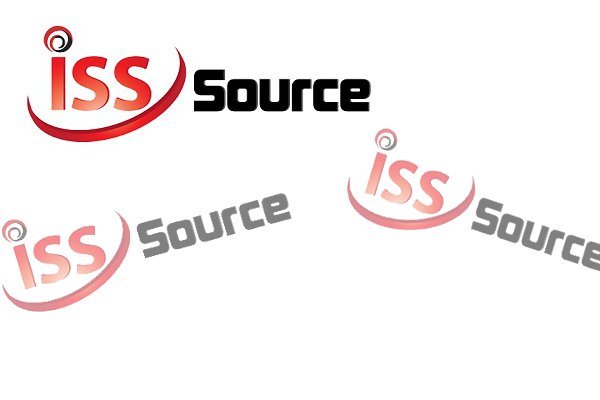
A manufacturer can have safety and productivity at the same time. That is not a concept of living in a fantasy world; if manufacturers are smart in using the proper technology and empower an enlightened work force, they will work and produce product in a safe environment which will mean they are producing more product devoid of unplanned shutdowns, said presenters during the Rockwell Automation Fair 2011’s Safety Automation Forum in Chicago.
“There are opportunities in safety,” said Steven Eisenbrown, senior vice president of strategic development at Rockwell. “When talking about safety and productivity five to 10 years ago people thought it was mutually exclusive. Good operating companies do all things well. Safety is integrating into mindsets and cultures and that is then ingrained into operating parameters,” he said.
What companies need to do to achieve quality safety and productivity is to develop a safety culture, perform safety assessments and invest in technologies and services, Eisenbrown said. Talking about creating a safety culture is easier said than done; there are challenges.
Three solid challenges are cultural challenges, business structural challenges and procedural challenges, Eisenbrown said.
Some issue are obvious, but when you look on the procedural area, you always have to see if safety and operations are on the same page and making sure they are on the same page on common goals.
One of the ways to reach those common goals is to work with everyone on the culture and not force it down people’s throats.
“When we coach people, they realize safety is about them,” said David Sarkus, industry veteran and author of five books talking about the safety culture. “The human element is such an important element.”
The idea of police workers compared to coaching them was the theme through Sarkus’ presentation. Coaching allows for a greater give and take and more people respond favorable, versus policing or telling people what to do and not allow them to think.
Sarkus related a story a Ford Motors worker told him years ago, when the worker said Ford paid him for his arms and his eyes, but they could have his brain for free. The problem was, they never let him use it.
“Oftentimes we beat people into submission to make them work safer. If you listen to them, so many great things can happen,” Sarkus said. “We often forget about the human aspect of safety.”
That is not to say corrections should not occur because conflicts do come up in a normal workplace.
“Correcting is necessary. If you can’t get people to use the machines the way they are supposed to, we can’t get the most out of them,” Sarkus said. “We need to make sure we let our people work safely before we correct them.”
In the end, it always comes back to communication.
“Conflict resolution is vital; issues arise and they need to be resolved,” Sarkus said. “Conflict needs to be resolved for clarity. Your supervisors need to clarify their vision for safety every day.”
Hale is the editor and founder of Industrial Safety and Security Source (ISSSource.com). You can reach him at ghale(at)isssource.com.
Edited by Amanda McLeman, Managing Editor, Plant Engineering and Control Engineering.