A bioplastics company contracted a system integrator to retrofit a brownfield plant to make Nodax polyhydroxyalkanoate (PHA)-based resins, adapting existing on-site batch controls.
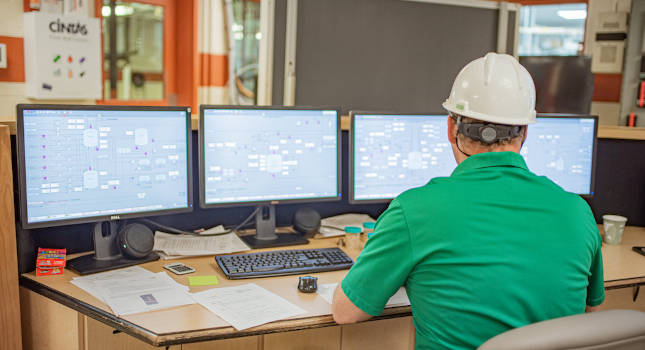
Learning Objectives
- Danimer Scientific partnered with Hargrove Controls + Automation to help them bring their R&D laboratory process online by retrofitting an existing facility in Kentucky.
- A lack of documentation and technical challenges caused problems during the retrofit process.
- There was also high demand for the company’s resin product, which caused additional challenges for meeting the deadline.
System integration batch control retrofit insights
- Danimer found an existing facility that could be retrofitted to make PHA resins for biodegradable plastics. The company purchased an 88,000-sq-ft brownfield plant in Winchester, Ky. to convert into the operating facility to repurpose and retrofit the facility.
- Retrofitting automation caused challenges because the existing documentation was inadequate and the existing equipment was not what it appeared to be when the design was created.
- Pandemic-altered equipment lead times were also a challenge for the project as existing batch control system was redesigned for the new application. Often design was modified to address equipment availability.
Danimer Scientific is a bioplastics company focused on the development and production of 100% renewable and biodegradable plastics and adapted brownfield site to upscale a lab process into a full manufacturing plant, adapting existing batch controls. Made from Nodax polyhydroxyalkanoate (PHA)-based resins, these compostable polymers can replace single-use plastics in sustainable products. The product has garnered widespread interest in the greater food and beverage industry as a replacement for traditional plastics such as straws, chip bags, single-use water bottles, etc. which end up in a landfill and can take over a hundred generations to degrade.
System integration, control design: Moving from pilot to production facility
Early in the development of the company’s patented new biodegradable plastic technology, Danimer Scientific partnered with Hargrove Controls + Automation to help upscale an R&D laboratory process and a small pilot line to a production-scale manufacturing facility.
“When we first partnered with Hargrove in 2015, we started working on making a production-scale facility for PHA, and we were the only ones doing this,” said Daminer Scientific’s COO Michael Smith. “The information didn’t exist on how to turn this laboratory hypothesis into a manufacturable process.” The system integrator helped“develop the technology and basically invent a new process. We were ‘writing the book’ for the world’s first PHA plant. We relied heavily on Hargrove for the design and automation functionality for a future greenfield facility’s design. We knew roughly how we wanted to make the product, and didn’t know what it was going to cost.” The system integrator “designed a facility so we could start raising money.”
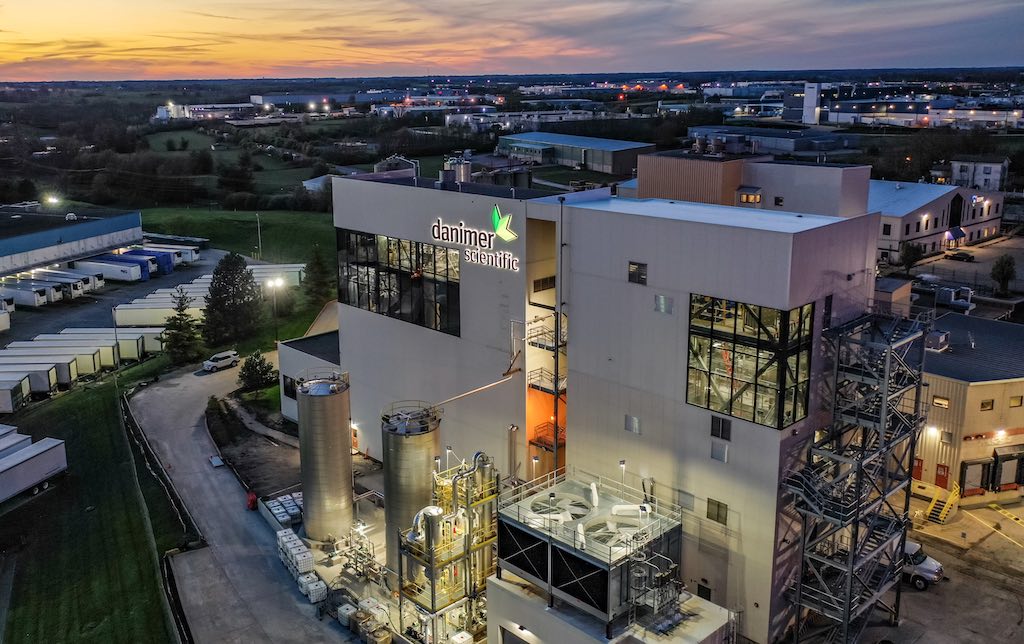
Danimer found an existing facility that could be retrofitted to make PHA. The company purchased an 88,000-sq-ft brownfield plant in Winchester, Ky. to convert into the operating facility to repurpose and retrofit the facility.
“We are so excited about what we make and what we do, and our company culture is to charge ahead, because this solution is so needed by the world. We aren’t a typical manufacturing company as we initially didn’t have an engineering group on the inside.” The manufacturer relied on the system integrator to guide the process, Smith said.
Full-scale challenges: Supply chain, automation scope, 4000 I/O
This project held many challenges. As the first operating facility for this product with no full-scale pilot, the team needed a solid plan with buy-in from all key stakeholders. In addition, the project needed to meet the budget demands of a startup technology company and navigate pandemic-induced supply chain issues.
The phase 1 retrofit total investment cost (TIC) was $55 million, for a total project TIC of $175 million. The automation scope had more than 24,000 human-hours and over 4,000 input/output (I/O) points. It also included narratives and specifications, multiple complex batch operations developed for upstream and downstream processes, tying new equipment into the existing facility, skid package interfacing, wireless network development, historian, site support, commissioning and operator training.
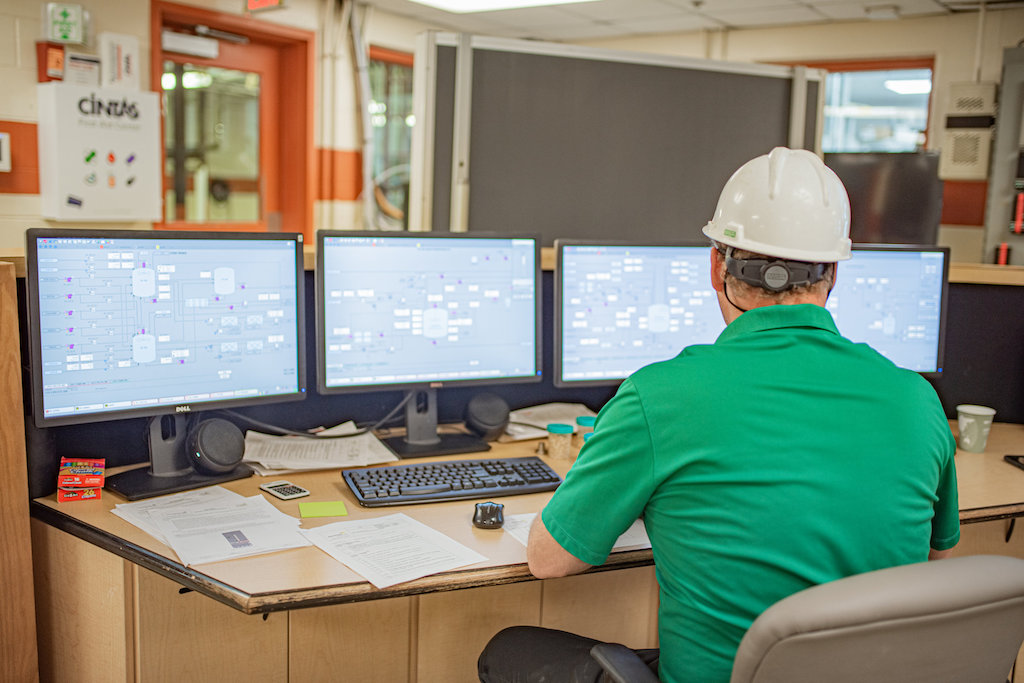
Retrofit design offers technical challenges: DCS, HMI
The facility is controlled by a distributed control system (DCS) batch system upgraded to the latest operating system and includes a human-machine interface (HMI) rebuild and operator interface. There is a plant-wide data historian which gathers information from the DCS. There are nearly a dozen third-party skids integrated together into the DCS, which was a significant part of the effort. Many of the skids are on the finishing unit, which takes the output of the clarification and sends it to the centrifuge, dryer, and pelletizer.
“What made this project challenging from a technical standpoint is that it’s a hybrid process,” said Joshua Payne, operations leader at Hargrove Controls & Automation. “It’s a mix of biotech, pharmaceutical, and life science technology mixed in with the heavily batch-oriented processes of a chemical plant.” The system integrator has a life science-focused group and is one of the largest engineering companies in the U.S. chemical space.
Payne continued, “Hargrove helped Danimer with due diligence on the Kentucky facility, making sure it was feasible to buy and use for their process. We engineered the conversion of the facility and engineered the automation.”
The existing facility had a batch control system, which was reused for the new application, said Alan Polk, technology & innovation leader at Hargrove Controls & Automation.
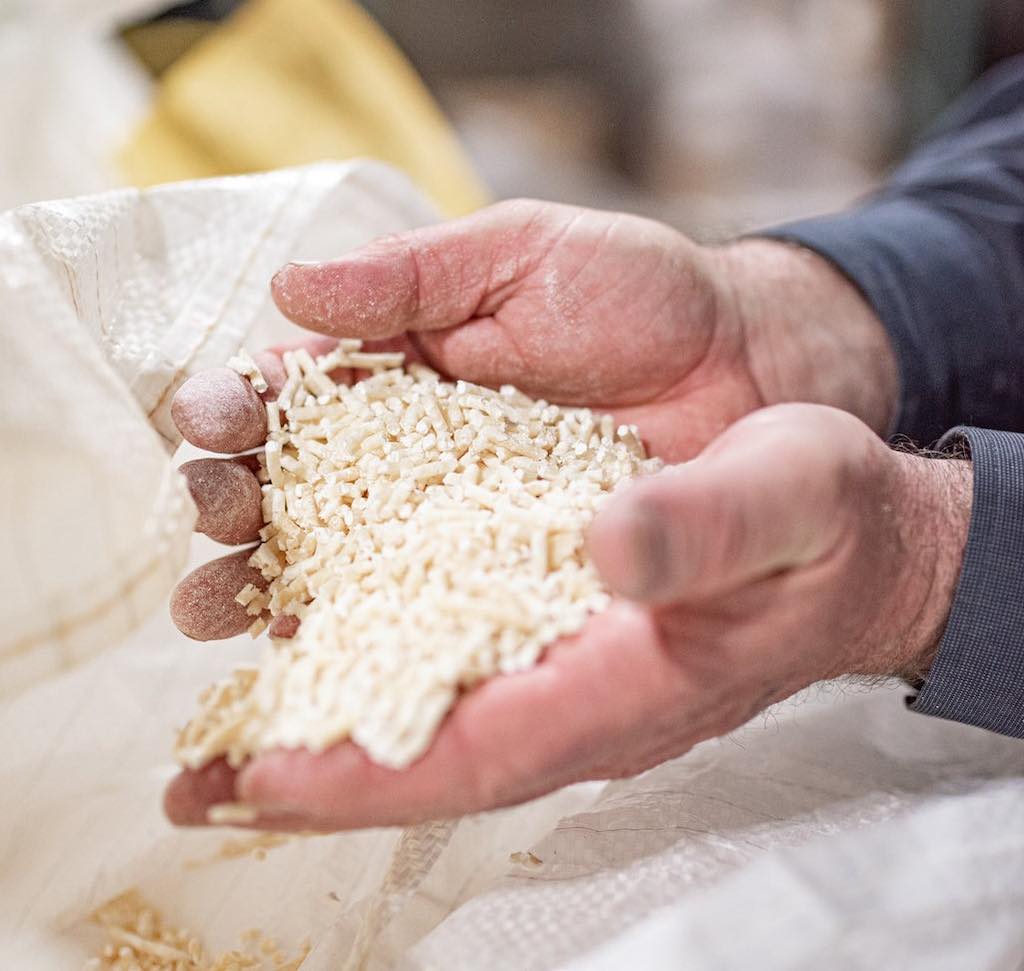
Integration, expansion, PLC palletizing
The system integrator’s efforts mainly focused on the fermentation and clarification parts of the original process, which included three small fermenters, clarification/purification, dryers, and a programmable logic controller (PLC) skid-based pelletizing system. Because of increased customer demand, Danimer decided to expand the new facility by tripling the capacity. This required more fermentation and down-stream processing equipment. The system integrator was asked to bringin two additional large fermenters, each more than twice the size of the original units, nearly tripling the fermentation capacity.
As expected with a retrofit project, Polk noted there were several technical challenges while bringing the Kentucky facility online. “Many of the project’s challenges were from turning an R&D process from a laboratory environment into production scale. The selected facility had been mothballed, so the existing documentation was inadequate and the existing equipment was not what it appeared to be when the design was created,” he said. “Further, we were trying to engineer a capacity increase on a system that was in an unknown state and had undocumented changes.”
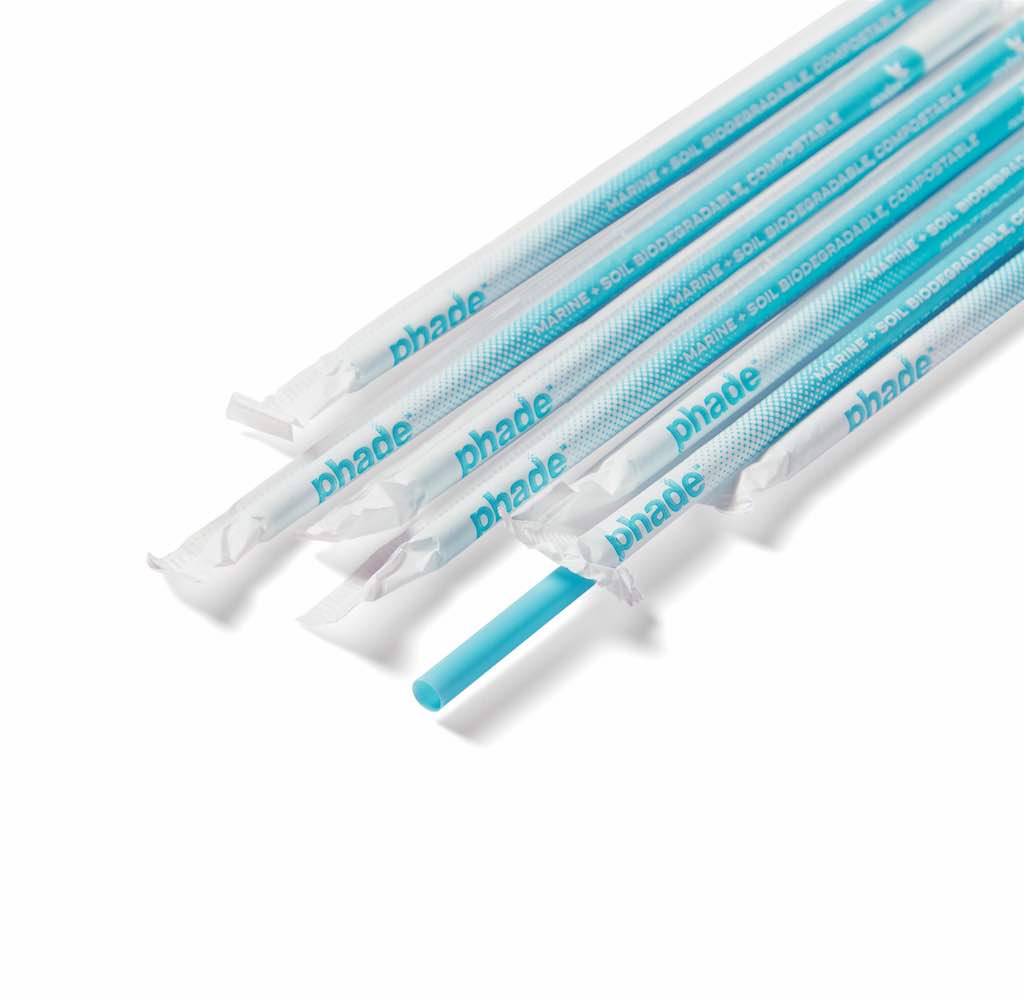
Process improvements, researching, testing, modifying
Polk noted the fermenters were operating without automation. “They were operating manually in a first-of-its-kind process,” Polk said. “This is a new process that no one has ever run before, so Danimer scientists were often making modifications. For example, the Danimer maintenance team may re-pipe something and add a couple of new valves. Danimer continually improved the process to increase yield and production.”
Polk said engineering continued on a triple-increased capacity project while Danimer was researching, testing, and modifying, while the system integrator ensured new changes were successfully incorporated into the design. The team “stayed agile and continued to both move the design forward and implement the process improvements.”
Pandemic-altered equipment lead times were also a challenge for the project. Oftentimes design was modified to address equipment availability.
“The team on this project was already agile, and the pandemic just added in another layer. Despite these challenges, the team never stopped. They kept moving forward, kept seeking out solutions, and kept Danimer on track to production,” Polk said.
System integration project, safety, quality
Bringing the Kentucky facility online was a very schedule-driven project, which was a constraint as well as motivator.
Payne said, “We’re going to do everything to get this done as quickly as is reasonably possible while maintaining our safety and quality standards.” Project included efforts to keep the design lean and costs low, while developing control schemes using good control theory integrated with equipment knowledge and use of emerging automation technology in the first PHA plant.
Karen Griffin, PE, is vice president of Hargrove Controls + Automation. Hargrove Controls + Automation is a CSIA certified member. Edited by Chris Vavra, web content manager, CFE Media and Technology, [email protected].
MORE ANSWERS
Keywords: chemical manufacturing, system integration
ONLINE
See additional system integration stories at https://www.controleng.com/system-integration/
CONSIDER THIS
Have you done a retrofit project at your facility and what were the results?