Physical characteristics include consistency, mechanical stability, oil separation, water resistance and low-temperature flow
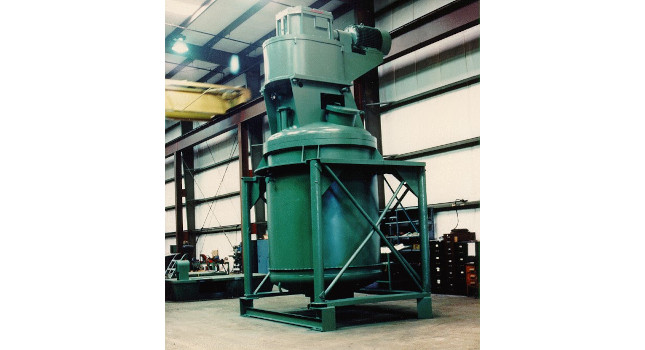
Lubricating greases are complex products, consisting of a lubricating fluid, performance enhancing additives and a thickener. The lubricating fluid can be mineral oil, synthetic fluid of various types or even processed vegetable oil. The viscosity of the fluid can range from very low (ISO 10 or less) to very high (ISO 6800 or higher).
Additives are added to grease to provide or enhance various performance properties. The third component of grease, and the one that sets grease apart from fluid lubricants, is the thickener. Multiple types of materials have been used to thicken oil to make grease, with the most common thickeners today being the soaps (salts) of long-chain fatty acids and alkaline earth metals. The reaction of fatty acid with alkali is known as saponification. The thickener is the component of a grease that produces consistency. This, in other words, is the stiffness characteristic of grease.
The thickening of greases
As stated, the most common grease thickeners are the simple and complex soaps. Simple soaps are formed by the reaction of a single fatty acid with a single alkaline earth metal. Complex soaps are formed by the reaction of both a long chain fatty acid and a shorter chain difunctional acid with an alkaline earth metal. The most common metal forms used are the hydroxides of lithium, calcium and reactive aluminum compounds.
Other thickeners used to make grease include polyurea (a reaction product of amines and isocyanates), calcium sulfonate, organophilic clay, fumed silica and polytetrafluoroethylene (PTFE). As with the soap thickened greases, polyurea thickener requires a reaction to be carried out under prescribed conditions. Calcium sulfonate thickener also requires controlled processing to produce a stable grease. The other thickeners require dispersion into the lubricating fluid to produce a grease.
Manufacturing greases
In the case of soap thickeners, polyurea and calcium sulfonate, considerable processing is required to produce the thickener and then produce the finished grease. Multiple steps of oil and thickener component addition, mixing, heating, cooling, are required to form a thickener that produces a grease with the desired characteristics.
Grease can be manufactured in many types of equipment, including open (atmospheric) kettles, closed (pressure) kettles, Stratco Contactors and continuous manufacturing units. Mixing configurations, heating/cooling media and age of the equipment all vary considerably.
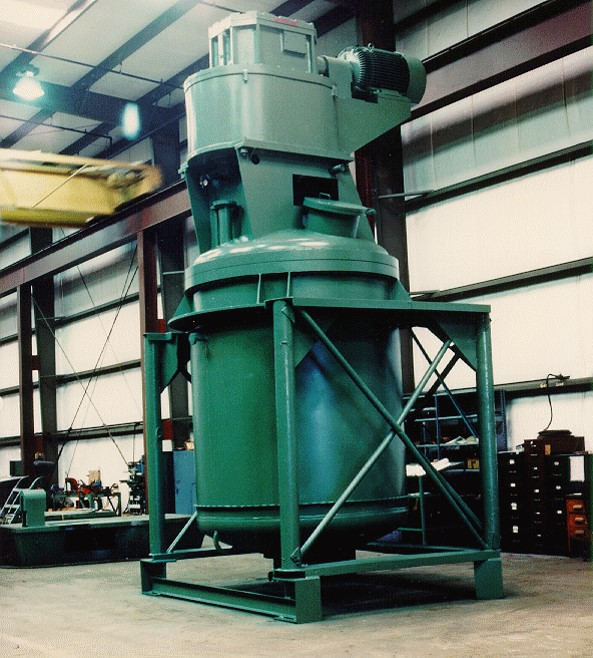
In all cases of manufacturing, process variables must be maintained to produce the desired thickener and finished grease. It the case of open kettles, pressure kettles and the Stratco Contactor, the time-temperature profile is of utmost importance. The proper temperature must be reached, in the prescribed time period, for the reaction to occur correctly. In addition, the temperature differential between the jacket and the batch, the rate of addition of fluid, the order of addition of the additives, the severity of homogenization, among other process variables, can all affect the outcome of the manufacturing process.
In the case of the continuous process, the maintenance of process variables such as temperature, pressure, differential pressure and flow rates all affect the properties of the final product. Each variable must be maintained in steady state during the course of manufacture to produce a grease with consistent properties.
The importance of grease specifications
Since there are so many variables in the manufacture of grease, which can actually override the formulation itself, specifications are critical to ensure consistent performance. Specifications typically include many of the physical characteristics that are affected by the manufacturing process, such as consistency, mechanical stability, oil separation, water resistance and low-temperature flow. Each of those properties is affected by the concentration of the thickener in the grease, and in turn by the manufacturing process variables. With proper control of process variables, the grease will meet the requirements of the specification and provide the desired performance.
The NLGI High-Performance Multiuse (HPM) grease specification includes tests for many of the properties affected by thickener formation and concentration. It is imperative to control the process variables when manufacturing grease to produce consistent product from one lot to the next, so as to consistently meet the specification requirements. The HPM specification provides for a product with good all-around performance for many applications.
When the application has more extreme operating conditions, a product with a higher level of performance may be needed. The HPM specification has accompanying “tags” that represent enhanced performance in certain areas. Greases carrying the WR tag have improved water resistance, while the LT tag indicates performance at low temperature and the HL tag is designed to provide higher load carrying capability.
The key to the HPM certification is that the specification is more extensive and challenging than typical grease specifications and requires validation of performance by NLGI through independent quality certification and testing agents. Thus, grease specifiers can feel confident in the quality of HPM certified greases.