Power Plus Heat with Reliability, Efficiency
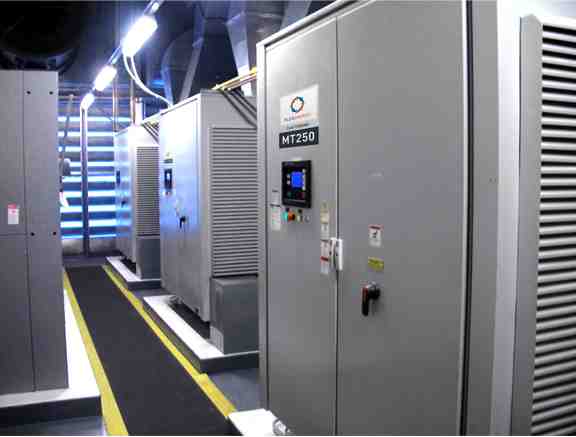
It’s a great idea: Generate your own electric power for use in your plant or on your campus, and use byproduct heat for space heat, water heating, process heat, absorption cooling — almost any thermal application. If you have surplus electric capacity, it can be sold back to your utility. That’s the promise with combined heat and power (CHP) installations, and one attractive option is microturbines. These are sometimes called “aeroderivative” turbines, reflecting their design ancestry as auxiliary power generators for aircraft. But in recent years they have carved out their own improved designs and flexible roles.
Growing in Size and Flexibility
Today’s North American commercial microturbine products were initially introduced in the 30 kilowatt (kW) size class. They have since been supersized to 60, and today 200 or 250 kW scale. One U.S. manufacturer also offer multiple turbine packages with coordinated controls and enclosures so they operate as a unit rated at up to 1,000 kW (1 MW). Beyond this, multiple packages can be combined for total capacities of 5 MW and more.
Byproduct heat is extracted from the turbine exhaust at temperatures of 600° F or higher. Because all of the waste heat is present in the exhaust gas stream, it is relatively simple to direct this waste heat through a steam generator to make steam to support or supplement various comfort and process applications. A microturbine can provide hot air, steam, or hot water for various industrial applications, or can also supply thermal energy to absorption chillers for building or process cooling.
A leader in the U.S. microturbine industry is Capstone Turbine Corporation, headquartered in Chatsworth. California. Capstone sells microturbine units in the 30, 65 and 200 kW class worldwide, as well as multiple turbine assemblies with capacities in multiples of megawatts. Aaron Tasin from Capstone was recently a presenter at a Technology and Market Assessment Forum sponsored by the Energy Solutions Center.
Green Energy Solution
In his presentation, he emphasized that microturbines are a green energy solution for several reasons. First, they typically burn either natural gas or a waste byproduct gas from a digester, solid waste site or from a petroleum production site. Any of these fuels have smaller carbon footprints than most utility electric generation sources. Secondly, because the microturbine produces both electric power and hot water or steam, it more fully utilizes the fuel energy used.
He reminded conference attendees that in large part, because of development of vast reserves of natural gas in shale formations, the U.S. now has a 100+ year supply of natural gas in the ground, plus a large potential for methane production from reclaimed landfill gas, and from agricultural and municipal wastewater digesters. He indicated that world reserves of natural gas are three times those of petroleum.
Efficiency To 85%
Tasin suggested that a microturbine installation that fully uses the thermal byproduct has a total efficiency of 85% compared to 58% or less for systems that use utility electric power plus an on-site boiler. Further, he emphasized that natural gas as a fuel has much lower emissions than the typical utility mix of coal, oil and some nuclear generation. Combine the lower initial emissions with the lower total energy input, and there can be no argument that this is truly a green solution.
Tasin noted that with thousands of turbines installed in locations around the world serving many types of heat and electric loads, microturbine technology is in the mainstream and an attractive solution for many types of users. He indicated that typically owners size their installation to meet their thermal requirement, and use all or as much of the electric output as possible and if there is a surplus, sell it to their interconnected central-station electric utility. “In this way, they get the full benefit of both the thermal and electric output.”
Serving Critical Winery Load
An example of an industrial load served with Capstone microturbines is Vineyard 29 in the Napa Valley of California. Here two 60 kW machines provide power to the plant for daily operations, plus heat for building heating in the colder months and to supply an absorption chiller for cooling in the hot months. The units run parallel with utility electric service, but can pick up load in the event of an outage during the critical grape harvesting period.
FlexEnergy manufactures microturbines for use in industrial, institutional and commercial settings. This company acquired Ingersoll Rand Energy Systems in 2010 and is headquartered in Irvine, California, with a worldwide spare parts depot at that location. Gas turbine production and assembly is done at its plant in Portsmouth, New Hampshire.
Wide Range of Applications
According to company spokesperson Su Anne Huang, the current product is the Flex Turbine MT250, a 250 kW-rated unit with broad applications for industrial and institutional users. Huang notes, “In most of the installations we’ve done, owners want to take full advantage of the thermal output of the machine. Generally we recommend that the unit be sized for the expected thermal load.”
She points out that FlexEnergy turbines meets all current and upcoming emission standards, and the Flex Turbine MT250 was the first combustion technology ever to meet the California Air Resource Board (CARB) 2007 emission standards. No exhaust catalyst treatment is required, and the NOx output is less than 5 ppm. The product has integral heat recovery and can be used for a wide variety of industrial applications that require hot air, hot water, steam or chilled water.
Medical Center Reduces Demand Charges
An example of an institutional user of microturbines is a recent addition to the John Muir Medical Center in Walnut Grove, California. This 324-bed acute care facility chose three Flex Turbine MT250 units, for an installed capacity of 750 kW. The goal of the project was to reduce utility electric demand charges, increase power supply reliability, and provide an economical source of domestic hot water for facility demands. The 2011 installation generates 3.3 million Btu per hour of thermal energy for water heating and meets rigorous CARB emission requirements. The medical center’s goal was a system with high reliability and minimal maintenance.
Is it Right for You?
Is there a gas turbine in your future? If you have natural gas service and a need for both electric power and thermal energy, it might well be the best solution. Your engineer should be able to help you calculate the potential costs and savings. Small gas turbines are in the mainstream, and can be a great solution for reducing costs and using fuel resources more efficiently, while reducing emissions and lowering your contribution to greenhouse gases. Give it some thought.