IMTS 2024 exhibits will emphasize automation and integrated solutions and will demonstrate automated solutions for computer numerical control (CNC) machining, additive manufacturing, robots and more.
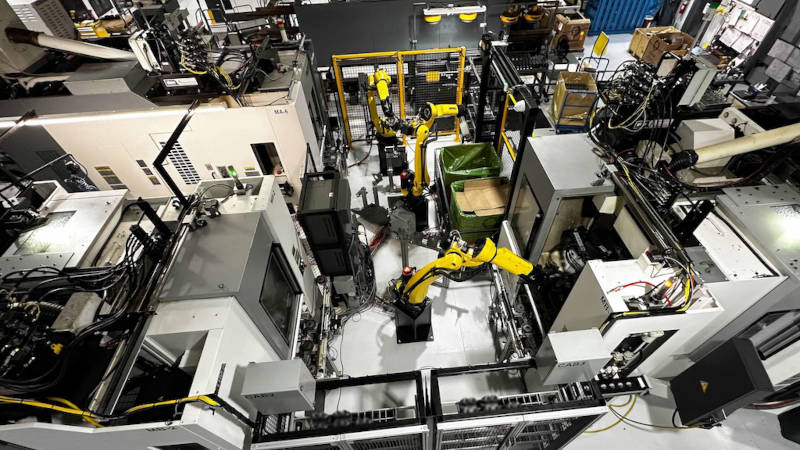
Automation and manufacturing insights
- IMTS 2024 will highlight automation solutions to enhance workforce productivity and business profitability, featuring robots, cobots, CNC machining, vision systems, and AI-driven technologies.
- A significant shift toward capital-intensive and labor-efficient manufacturing is evident, with a 12% increase in capital utilization per labor unit from 2017 to 2023, driven by automation.
- IMTS 2024 emphasizes additive manufacturing’s role in improving supply chain resilience, offering solutions for in-house production and reducing dependency on uncertain international suppliers.
IMTS 2024 – The International Manufacturing Technology Show offers contract manufacturers, job shops and original equipment manufacturers (OEMs) the opportunity to explore thousands of solutions to address workforce, quality and efficiency issues.
IMTS 2024, held at McCormick Place in Chicago on Sept. 9-14, will feature the new Automation Sector, accelerated by SPS – smart production solutions in the North Building, which features companies specializing in robots, collaborative robots (cobots), motion control, data management, and automation integration. Exhibits throughout IMTS also will demonstrate automated solutions for computer numerical control (CNC) machining, additive manufacturing, vision systems, metrology, tooling, workholding, abrasive machining, gear generation, parts handling and cleaning and other manufacturing technologies.
“Automation is omnipresent at IMTS because exhibitors know industry needs automation technologies to leverage worker productivity and boost business profitability,” said Peter R. Eelman, chief experience officer, The Association For Manufacturing Technology (AMT), which owns and produces IMTS.
Ian Stringer, vice president of data strategy at AMT, said, “The push toward greater adoption of industrial automation is influenced by an aging workforce and geopolitical uncertainties that have increased defense spending and led to a revitalization of the U.S. supply chain.”
Stringer noted capital intensity (the amount of capital utilized per unit of labor) has surged almost 12% from 2017 to 2023, according to the March 21 economic news release from the Bureau of Labor Statistics. According to Stringer, this figure “is solid evidence” of a significant shift toward more capital-intensive and labor-efficient manufacturing processes facilitated by the automation solutions shown at IMTS 2024.
“From reshoring initiatives and workspace optimization to production capacity and workforce shortages, multiple issues are often at play when companies are looking to invest in automation technology,” said Doug Burnside, vice president of North American sales and marketing for Yaskawa Motoman. “For smaller companies, collaborative palletizing and welding are two easy options for first steps into automation. The systems deploy rapidly and have user-friendly pendants.”
Cobots, machine vision and AI
Collaborative robots (cobots) are a true workforce multiplier and will be demonstrated in conjunction with tooling and workholding, welding, metrology, machining, part handling, and scores of other applications at IMTS.
According to Will Healy, global industry leader – welding at Universal Robotics (UR), a cobot can arrive on a loading dock in the morning and be assisting with production by noon because cobot providers have “a hyper focus on simplifying the cobot integration experience and improving the cobot operator experience.”
Today, machine operators (not robot programmers) can program and staff multiple pieces of equipment, boosting machine utilization numbers and shortening changeover time between parts.
With these factors, shops can now run more parts per machine with overnight runs or lights-out manufacturing, boost shop competitiveness, and help company leaders win new business.
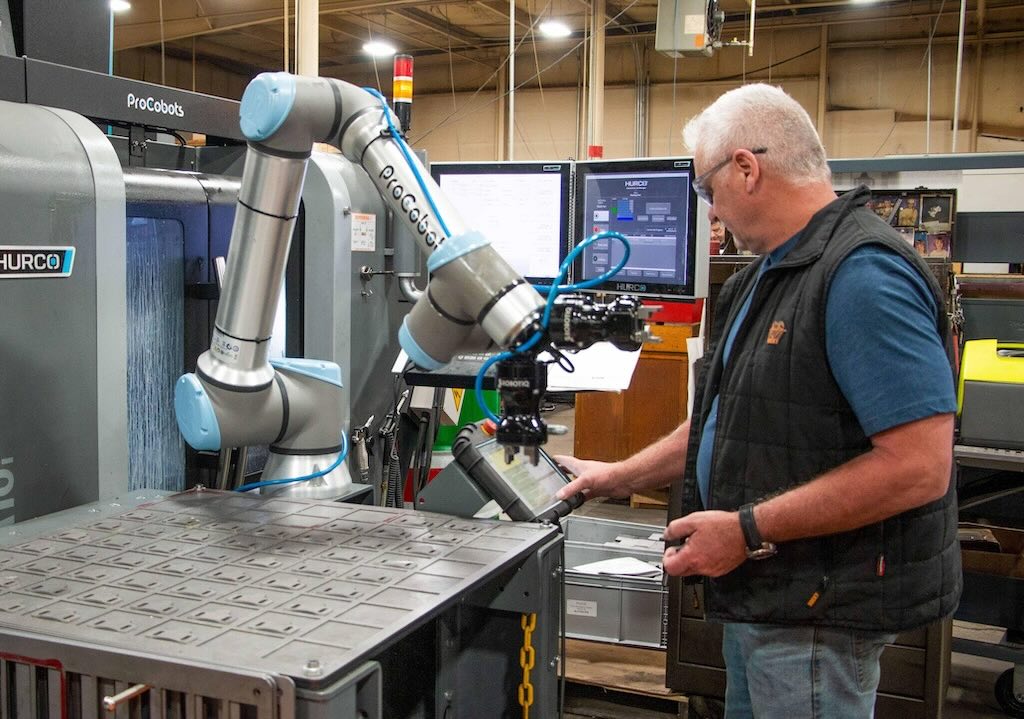
“At IMTS 2024, conversations will center around how artificial intelligence and cobots come together to bring new levels of usability and productivity to the shop floor,” Healy said. “As an example of applications that were challenging to automate in the recent past, we will demonstrate how a UR20e cobot can pick a wider variety of parts with an unprecedented reliability.”
This advance occurred through a partnership between UR and Siemens that utilizes Siemens’ deep learning-based vision software, called SIMATIC Robot Pick AI, and Zivid’s M130 3D camera.
Generative AI innovation
As manufacturers embrace automation, they also need to explore the transformative power of generative AI. Google Cloud delivers AI and machine learning solutions to unlock untapped potential and drive innovation through data-driven insights and intelligent automation. Google Cloud can help IMTS visitors understand where and how to apply AI to product design, research, production, supply chain, customer service, and other manufacturing processes.
System solutions
As part of the increase in automation, exhibitors in the Metal Removal Sector will demonstrate production cells (e.g., not just stand-alone products) and collaborate with other exhibitors to deliver turnkey solutions.
“You simply can’t talk about the advances in automation and machining without talking about them together, and IMTS is where everyone comes together,” said Scott Harms, president of MetalQuest Unlimited. “For example, at IMTS 2022, we committed to the machining and automation strategy used to fulfill a new contract in a conference room above the OKUMA booth, where our FANUC representative was also present.”
At IMTS 2022, advances in vision systems were central to MetalQuest’s purchase decision, which featured three horizontal machining centers and three robots. A robot equipped with FANUC’s 3D vision-based bin-picking technology picked out parts that had been randomly dumped into a bin. The first robot then presented the part to the other robots, which then loaded them into the HMCs.
“That’s pretty cutting edge, even for a system integrator,” Harms said.
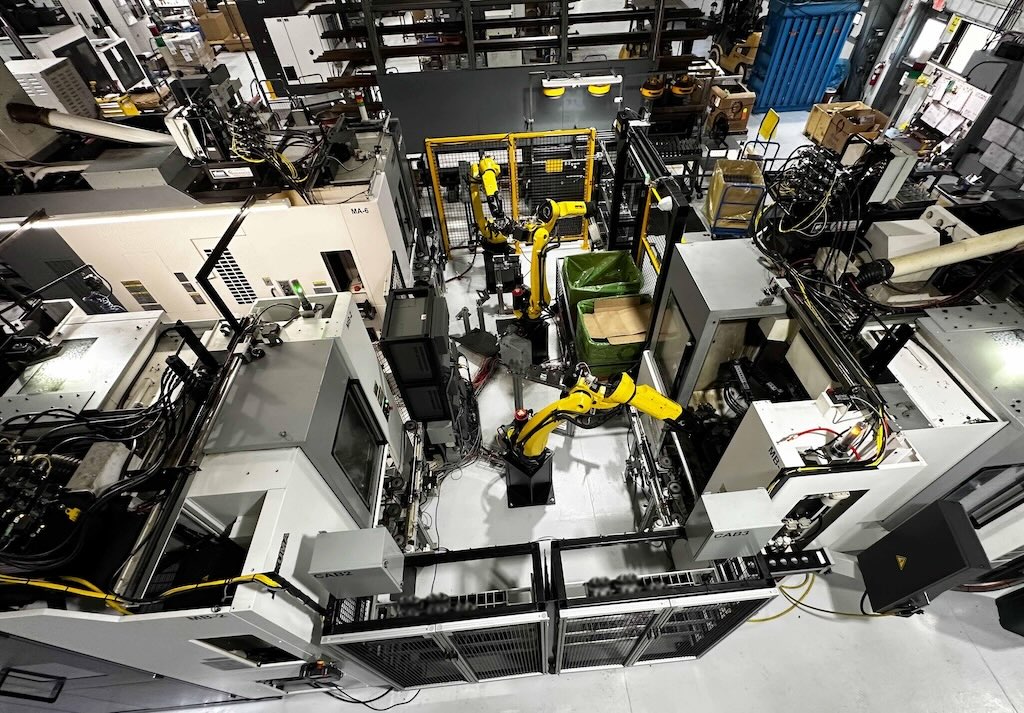
Quick wins
For automation without the expertise of a third-party system integrator or a that won’t drain on limited internal resources, HM Manufacturing selected a Turn-Assist robot from RoboJob USA.
“This new robot aids our Okuma lathe in more capacity and allows for larger production runs,” said Nicole Wolter, HM Manufacturing president. Her company has purchased almost every machine in its operation as a result of attending IMTS. “Being able to see the technology, meet people, and ask questions is how we stay up to date.”
To keepFor making chips while loading and unloading parts, Chad Sesing, vice president and plant manager at JTD Enterprises, was “impressed by automatic pallet changers from Midaco and how they easily adapt” to their his company’s current Haas machines.
“We were able to purchase one and install one on our Haas VF-2SS,” he said. “We were glad we could see it in person at IMTS to understand how it would benefit us.”
For applications requiring extended unattended run time, pallet pools may be the most efficient automation solution, as was the case at Olson Custom Designs.
“One of our customers launched a new product that ramped up very quickly,” said co-owner Brian Olson. “We were able to put in a Kitamura Supercell-300G 5-axis horizontal machining center with a 20-station pallet pool on the floor and ramp up our production to meet their needs.”
Once fully loaded with material, the cell can run for 35 hours unattended.
In control
While pallet pools provide capability, advanced machine controls ensure accuracy and consistency during unattended runtime.
“The TNC7 control will help end users to feel confident in automating their process,” said Gisbert Ledvon, vice president of marketing at Heidenhain. “This year at IMTS, we will demonstrate tool quality and tool life monitoring features using the TNC7’s integrated tool table database.”
Heidenhain also will demonstrate the TNC7’s component monitoring and process monitoring capabilities. Component monitoring can detect events such as tool breakage or excess force on the spindle. Process monitoring captures the data for a sample path and compares subsequent paths to this reference; deviations are graphically displayed, so operators can pinpoint the location.
Additive manufacturing builds robustness
Additive manufacturing (AM) is inherently an automated process, which is especially helpful to large-scale metal additive technologies such as directed energy deposition (DED), which can replace forgings, castings, and tooling. These products typically come from overseas with lead times of six to 18 months, which AM can shorten to a few months or weeks.
Melanie Lang, co-founder and CEO of Formalloy Technologies, believes the trend of adding AM equipment to move work in-house is growing and will continue.
“The last few years opened our eyes to the instabilities in our supply chain,” Lang said. “We can’t take delivery times for granted; the true country of origin for our products remains uncertain; and some sources are subject to geopolitical issues. Fortunately, we can apply technology to solve those problems.”
Jacob Sanchez, an automation industry analyst, content creator, and IMTS 2022 attendee, noted that IMTS 2024 will reflect the extent of automation’s integration into key manufacturing processes such as AM.
“Exhibitors in the Additive Manufacturing Sector, accelerated by Formnext, are a great resource for finding end-of-arm tooling, inspiration for custom workholding, and other ways to keep equipment running 24/7,” he said. “IMTS puts you in an automation mindset because you can find automation in all the exhibit halls.”