Researchers have strengthened their absorbing foam material to make lighter and stronger helmets, which can help soldiers as well as people working in hazardous conditions.
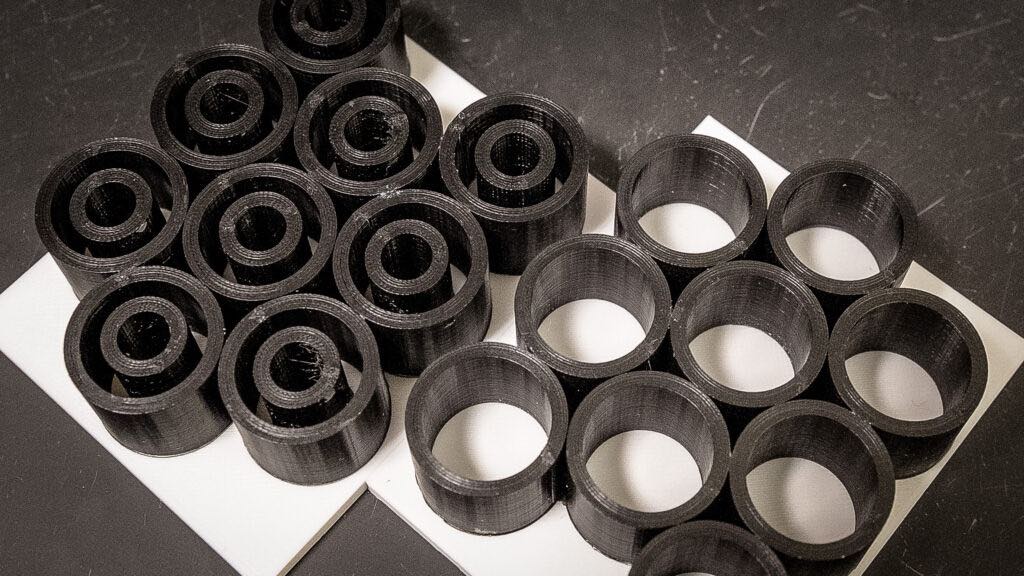
Personal protective equipment (PPE) insights
- UW-Madison engineers developed an ultra-shock absorbing foam material to improve helmets in 2022. Now, they’ve reduced the density and the weight of their foam material while retaining much of the material’s exceptional properties.
- While it certainly helps soldiers in their day jobs, it also can help workers who operate in dangerous situations where they are at risk of being hit on the head or subject to potential blunt-force trauma. It will be a useful personal protective equipment (PPE) tool.
In November 2022, University of Wisconsin-Madison engineers announced the creation of an ultra-shock-absorbing foam material that could dramatically improve helmets.
The researchers’ material, an architected, vertically aligned carbon nanotube foam, can absorb significantly more energy from impacts than the foam currently used in U.S. military combat helmet liners. It also exhibits much greater strength and stiffness.
As a helmet lining material, the researchers’ foam holds tremendous potential for helping to mitigate, or even prevent, concussions and other traumatic brain injuries, according to Ramathasan Thevamaran, a UW-Madison assistant professor of mechanical engineering who led the research.
Now, Thevamaran and his team have discovered a way to greatly reduce the density, and thus the weight, of their foam material while crucially retaining much of the material’s exceptional properties. The team detailed its advance in a paper published online in the journal ACS Nano.
“Typically, materials with a higher density will have better mechanical properties. So, it’s very challenging to achieve superior mechanical properties in a material with a low density,” Thevamaran said. “For example, think of a piece of solid metal. Poking holes in the metal would reduce its density but also cause its properties to severely degrade.”
To achieve this breakthrough, the researchers tailored the design of their vertically aligned carbon nanotube foam to have unique structural features across multiple length scales. Their material has a novel architecture that consists of closely packed thin concentric cylinder structures at the micrometer scale, with each cylinder made of many carbon nanotubes, which themselves have a concentric cylindrical structure in the nanometer scale. These structures give the material its outstanding properties.

In this study, the team investigated a variety of design parameters and discovered the internal gap between the concentric cylinders plays a key role in determining the material’s overall properties. They varied the material’s density by changing the internal gap, and then observed how those changes induced different types of deformation in the material when compressed. Ultimately, the researchers discovered that increasing the internal gap, up to a certain point, led to better structural stiffness at low densities.
“In this work, we achieved a desirable linear scaling between properties and density in vertically aligned carbon nanotube foams designed with our unique architecture,” Thevamaran said. “We were able to create that linear scaling by tailoring the gap between the concentric cylinder rings. This allowed us to simultaneously improve our material’s damping capacity and energy absorption efficiency while also allowing the material to be extremely lightweight.”
The researchers are patenting their technology through the Wisconsin Alumni Research Foundation (WARF).