Provide insight, accountability to your operation one step at a time.
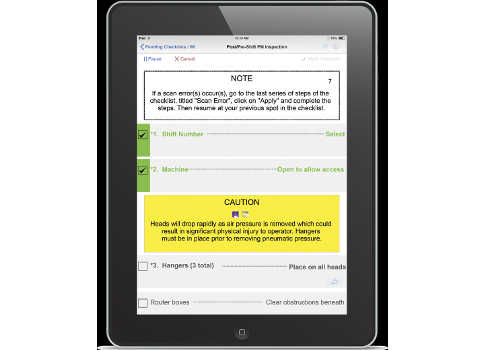
In manufacturing, getting the job done right the first time and every time is a must. Many plants try to implement the latest and greatest process efficiency fad, but experience fatigue and failure when sustained results are not being realized. It is no wonder these attempts by management to instill a positive operational change in their business have only a 30% chance of success.
Throughout the manufacturing process, critical tasks are routinely performed with experiential or tribal knowledge: a culture of "I think" rather than "I know." Great procedures exist, yet it is people who ultimately operate manufacturing plants. Memories fail and moods swing. Human factors can cause even the most experienced operator to have a lapse in judgment or decision-making.
Senior management is coming to grips with the challenges they face when dealing with human factors, such as psychological and physiological threats from daily life in and outside of work, that serve as key ingredients to most accidents and productivity losses. Safety has been the target, but falling short of that mark puts manufacturing organizations closer to an inevitable accident (unless extremely lucky). Striving for perfection positions an organization further up the performance ladder where safety is inherent, and farther away from a potential accident.
The "checklist culture" One way an organization can prevent human error and sustain efficiency gains is by instilling a checklist culture. Applied with rigor, checklist operations leverage four key attributes for success: process reliability, verifiable compliance, best practice capture and operational insight. Here are four detailed checklist processes, along with real-world results they helped to achieve.
1. Process reliability: Tasks are completed correctly the first time, every time, substantially decreasing the amount of rework necessary, improving customer satisfaction by reducing back orders and delivering products in their expected condition on time.
A site manager stated that in 25 years at his facility, he never had a week without at least one item left on the dock. When an item is left on the dock it requires someone to search the plant to find it and then to schedule a separate truck to deliver the missing items to their waiting customer. Through use of the checklist, the plant achieved its first week ever without a single item left on the dock, and they have been able to repeat this success consistently.
2. Verifiable compliance: Enables leadership to target very specific steps of a given process for improvement thereby increasing worker accountability, identifying process deviation, and enhancing quality assurance.
For one plant, compliance with the company’s periodic inspection report program at the completion of 2015 was as low as 10% in some departments. After two months implementing a checklist program, quality inspection compliance increased to well over 90%. Additionally, leadership at the plants now have the ability to see which individual shops are complying at the highest rates and which ones are complying the least. Accordingly, they are also able to recognize top performers while providing mentoring to the individuals and shops that need it most.
3. Best practice capture: Identifies and captures best practices in operations that can be replicated across plants and process lines, increasing production efficiencies.
Another plant was having serious problems with the start-up times on some of its lines. Following each weekend, start-up times required one hour of unplanned downtime every Monday morning. To determine root cause, they executed the start-up checklist and analyzed the resulting data with their line leads and operators. During a brief brainstorming session, they quickly recognized that the condition in which the machine was left the previous Friday was causing multiple delays getting the line running on Monday.
Plant management developed a second-shift shutdown checklist to be run on Friday afternoons that included proper cleaning of equipment and the draining of air lines. The result was they were able to reduce the start-up time from one hour to six minutes. They calculated the value of this one checklist as follows: three product lines, totaling 27 workers at $661.50 labor per week resulted in an annual savings of $33,075 in wasted labor cost, and increased capacity by 102 units per week. They have since replicated this best practice to the other production lines in the plant and the company is planning to transfer this best practice to all similar plants.
4. Operational insight: Uncovers real-world plant data to help identify and correct root causes for non-productive time, improving delivery schedules and saving costs.
At another manufacturer, the time to load trucks and ship product was becoming a problem. Despite their best efforts they could not reduce their average time to load the trucks and back orders were driving up costs. By reviewing the data captured by plant’s checklist application in use, they found that 57% of the time trucks were idle and waiting for product to arrive at the shipping dock. Additionally, 83% of the time waste was due to a specific product. They initiated problem solving and root cause analysis activities that led to the implementation of a one-piece flow model so that product was manufactured in sequence of truck. As a result they reduced truck loading time by 25% (From 4.25 hours to 3.25 hours), reduced wait times by 43%, and ultimately reduced backorders by 44%. The estimated annual savings was more than $125,000.
Change the culture, too
While a proper checklist culture and its attributes can deliver sustained results, it cannot be done in a vacuum. It is imperative the checklist be designed with a plant’s leadership team and its company culture/behavior taken into consideration.
Leadership must be heavily involved to guarantee operational checklists align with current business objectives, yet subordinate insight and feedback should also be leveraged to ensure any new processes coincide with and not detract from the existing company culture.
Further, trust is irreplaceable. Communal discipline allows supervisors and their subordinates to follow a standardized set of company-based procedures, written by boots-on-the-ground professionals with real-world experience, rather than a chain-of-command hierarchy based on experience learned 20 years ago from a manual, or worse, the previous supervisor.
Teamwork is a by-product of reliability and consistency. A checklist culture is a reliably consistent team of individuals who communicate with each other across the enterprise in familiar language and operate in near perfect rhythm to complete assigned tasks—precisely, safely, and efficiently.
Checklist development
The goal of a checklist culture is not to supersede procedures. The basis of checklists is to assist users while executing tasks derived from approved procedures. Every time. Verified. They include the minimum essential steps and link specific hazards and mitigation actions directly to a job’s actual steps. Checklists act as a crosscheck to prevent common sources of human error, such as forgetting procedural steps, doing steps out of order, a failure to recognize risk associated with actions, direct mutual support or external quality assurance (QA) for critical steps, and others.
Successful checklist development also must include real-time and specific notes, cautions, and warnings that alert users prior to performing individual steps. Notes should highlight an operating or maintenance procedure, technique, condition, or statement considered essential. Information contained in notes may also be safety related. Cautions should highlight an essential operating or maintenance procedure, practice or condition which, if not strictly observed, could result in damage to or destruction of equipment or loss of data. Warnings should highlight a breach of maintenance procedure which, if not strictly observed, could result in injury to or death of personnel or long-term health hazards.
Checklists should only be written to mitigate human error for an operation’s most critical, high-risk tasks, where failure is not an option. They should not be written for every job task during the extracting, processing, and manufacturing lifecycle.
As evidenced by the examples above, instilling a sustained checklist culture in the manufacturing industry will move organizations from an experienced-based culture, merely aiming for safety, to a knowledge-based culture performing standardized, precision operations. Implementing simple checklist tools makes it easier for crews to use standard procedures to increase productivity and create environments where safety is a short-putt result of doing the job right, every time.
Jim Weynand is chief revenue officer for Check-6.