Four programmable relay logic settings that will improve protection and add value
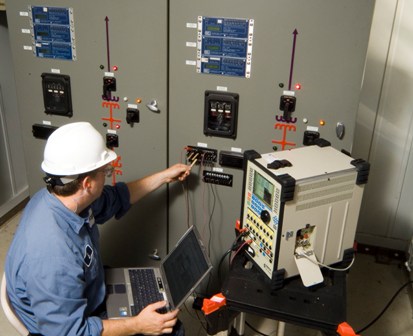
In the event of an electrical system fault, the protective relay system isolates the affected components while maintaining stability within the rest of the grid distribution system. Many utilities and industrial facilities are replacing aging electromechanical and solid-state relays with new generation microprocessor-based relays that deliver many benefits including self-testing and diagnosis, reduced maintenance, simplified regulatory compliance, arc flash mitigation, event recording and reporting capabilities, and improved protection.
While microprocessor-based relays have vast potential functionality, many of the relays’ capabilities and advantages often go unrealized. This happens for a number of reasons, including:
- Lack of owner awareness: Custom relay configuration has only recently become an option.
- Simple oversight: Owners may overlook the need for relay customization and programming during the estimating, bidding, and specification processes.
- Lack of knowledge and expertise: Engineers may not have the skill levels needed to program relays, or the designers and installing electricians may be unfamiliar with the relay’s capabilities.
- Complexity issues: Custom programming can sometimes cause the system design to become overly complex. For simple applications, the effort needed to configure all the available features would not be worthwhile.
Unfortunately, relay capabilities have outpaced industry skill levels. Often a relay is installed as a direct replacement for aged or defective equipment and the subsequent logic programming is performed by personnel unfamiliar with the new equipment. Improperly programmed relay logic can lead to a wide range of protection system problems. For example, inappropriate logic settings can lead to repeated system misoperation, nuisance tripping, unplanned shutdowns, and production interruptions becoming a source of frustration for asset and facility managers. In these cases, managers often revert to the default logic settings just to keep the system running. While this is a tempting quick fix to a frustrating situation, this practice can ultimately result in even greater costs if the equipment is not adequately protected.
The key to leveraging the full range of microprocessor-based relay capabilities and optimizing system protection is to work with integration engineers that have the expertise to properly configure each relay to meet the utility or facility’s unique objectives. They consider the many differing needs of owners, engineers, utilities, and equipment manufacturers and then balance those with the requirements of local jurisdictions and industry standards (JCAHO, MSHA, NERC, FERC).
Within this framework, integration engineers begin to apply power system studies, such as short circuit, coordination, arc flash hazard, motor starting, and load flow analysis, to customize protection for each application. Ultimately, the relay system is easy to use, reliable, and only as complex as needed.
While project requirements will obviously be unique for each facility or utility that upgrades to microprocessor-based relays, there are at least four programmable relay settings that every facility should consider to improve their protection scheme and add value to the system.
1. Self-monitoring and diagnostics
Simplification of the control system through the reduction of necessary components and single points of failure is a tremendous benefit which can be further compounded by adding real-time monitoring and failure alert functionality. However, these benefits can only be realized if custom logic has been programmed and tested.
The reduction of necessary hardware components can be accomplished when previously installed hardware (e.g., 86 lockouts or 62 auxiliary timing relays) is emulated with customized logic programmed in the relay. For example, an 86 lockout relay previously installed as hardware can now perform the exact same functionality through operator interaction with the front panel display of the protective relay. Through the reduction of separate hardware components, the number of single point failures decreases, thereby increasing the robustness and reliability of the electrical system.
After all of the possible hardware components have been moved into relay logic, self-monitoring and diagnostics provide a means to alert the operators of system component failures prior to an entire system failure or misoperation occurring. Previously, the only way to determine whether or not the system would function as intended was through manual testing, often requiring a complete system shutdown.
2. Event-recording capabilities
Microprocessor-based relays offer built-in event recorders, capable of capturing and time stamping event information at one millisecond resolution. Following a fault, the relay can reproduce a report summarizing the sequence of operations prior to the event. Information collected by event recorders can include trip sequence, the amount of time a breaker was open, where the fault occurred, nature of the fault, pre-fault conditions, and power quality monitoring waveform. These details expedite troubleshooting and can help operators more quickly identify the root cause of a fault. Ultimately, faults are cleared quickly and safely, minimizing costs and downtime.
While event recorders are powerful tools, their output is only as good as their input. Integration engineers need to identify all elements that should be recorded in the event of a fault. However, it’s important to remember that event recorders have limited data capacity and will begin dropping old data from the file once that capacity is reached. Therefore, some elements should be left out of the event recorder depending upon how often they toggle. Best practices call for the engineer to structure the high-speed data capture for trips, abnormal voltage, or currents to aid in event analysis during future trip investigations.
3. Arc flash mitigation capabilities
Many microprocessor-based relays include an optional protection feature for arc flash detection. This feature can immediately respond to arc flash incidents by detecting a combination of excess light and current. The feature can help workers avoid devastating injury and prevent costly equipment damage.
To determine if this relay feature is needed in a specific environment, protection engineers can complete an arc flash hazard analysis to identify the potential for and location of possible arc flash hazards. Such an analysis may include recommendations to utilize microprocessor-based relays for additional arc flash protection. In these instances, the arc flash mitigation capabilities should be programmed into the protective relay, using logic to instruct the relay to immediately interrupt the circuit if developing arc flash conditions are detected.
4. Motor/generator protection features
Most industrial facilities, wastewater treatment plants, manufacturing facilities, and refineries operate a large number of motors, some of which cost tens of thousands of dollars. Large motors are expensive to repair or replace and lead times are long. Each motor can be effectively protected by one microprocessor-based relay. However, the features within the relay must be programmed correctly, per the motor manufacturer’s specifications and mechanical load, taking into consideration dynamic response of the facility’s power system.
Some motor protection relays allow for limiting the maximum starting time or maximum starts/hour to allow for adequate cooling of the motor during high-current, low-speed operations. Often, this function is underutilized or misunderstood and is either disabled or set to a value that does not adequately protect the motor. To take advantage of this function, protection engineers perform motor starting and load flow studies to determine the maximum motor starting times that can be expected under the most restrictive conditions. Relays are then programmed to prevent damage but still allow for adequate start times without nuisance tripping.
The installation of microprocessor-based relays isn’t “plug and play.” Relying on default logic can provide a false sense of security that may not be revealed until after severe equipment damage or unplanned outages have occurred.
Utilities and industrial facilities frequently make a critical mistake when upgrading to microprocessor-based relays by failing to customize the relays’ built-in programmable logic, thus forfeiting the relays’ ability to properly protect the electrical system. With the help of an experienced protection and/or integration engineer, utilities and facility owners can identify the features and capabilities within each relay that should be leveraged. By investing in proper relay logic customization and programming, facilities ensure optimum protection for their electrical systems and simultaneously realize the full value of their upgrade investment.
Steve Nollette is a supervising engineer for Emerson Network Power’s Electrical Reliability Services.
Key Points:
- Changes in equipment and in electrical systems require expert installation of protective relays systems, but this often does not take place.
- Simplifying the control system control system is a benefit, but can only be realized if custom logic has been programmed and tested.
- An arc flash hazard analysis can identify the potential for and location of possible arc flash hazards. If found, that also can be programmed into the relay.
- The installation of microprocessor-based relays isn’t “plug and play.” Relying on default logic can provide a false sense of security that may not be revealed until after severe equipment damage or unplanned outages have occurred.