Electrical and power systems have changed in many ways over the years and their impact is felt throughout the plant floor in many ways.
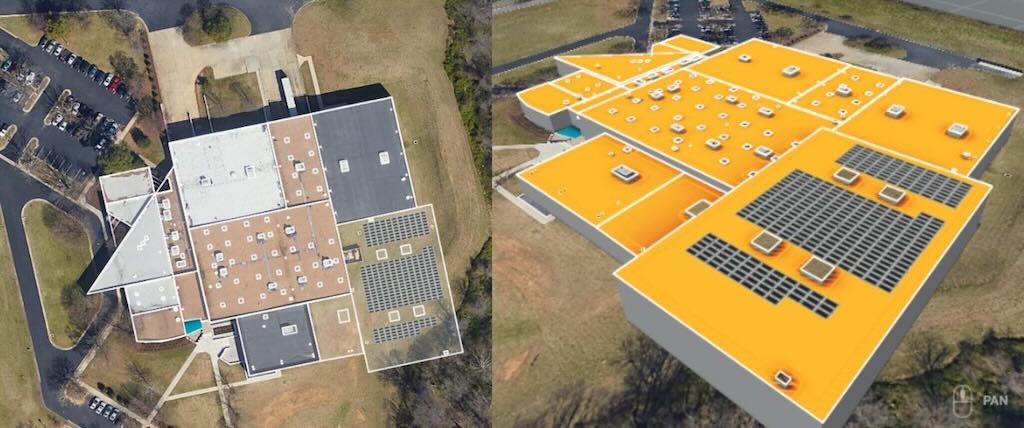
Respondents
- Ken Crawford, senior director of automation, Weidmuller USA, Richmond, Va.
- Scott Dowell, senior vice president and general manager, industrial and CIG, Wesco, Pittsburgh
- Marc Elliott, marketing director, Eaton, Wilsonville, Ore.
- Zack Mitchell, CHST, GSP, assistant corporate safety manager, Stellar, Jacksonville, Fla.
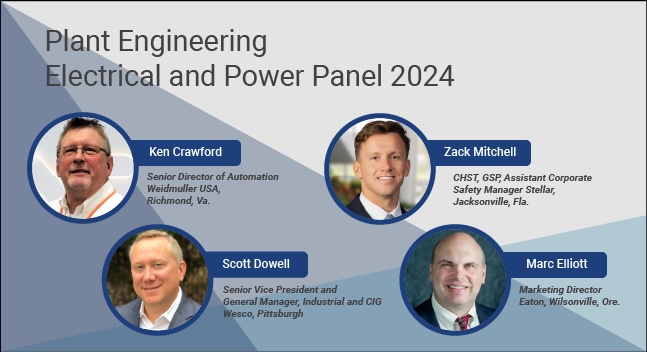
Question: What’s the current trend in electrical and power systems for industrial and manufacturing facilities?
Scott Dowell: Sustainability is one of the largest trends in electrical and power systems today, but manufacturers are increasingly looking to marry sustainable energy efforts with three key factors – safety, cost effectiveness and uptime.
Manufacturers have already been reporting on their efforts towards sustainability, sharing information on their carbon footprint or producing annual sustainability reports. Much of their focus today is on ensuring they are meeting the goals already established and figuring out how to get the right mix of power consumption needed to do the manufacturing process, in the most economical way possible, as they move forward.
To do so, they need to take stock of what power sources are available and what already exists. With an aging workforce that is headed into retirement, maintaining institutional knowledge is critical. For example, many plants are operating with aging equipment. Perhaps there is a dated electrical panel that is finicky due in part to a historically minimal maintenance schedule. Understanding the existing limitations as well as current and future power consumption needs helps to shed light on reliability and uptime, as well as one of the most pressing concerns – employee safety.
Following the COVID-19 pandemic, there is an increased awareness about the role organizations must play in keeping their employees safe on the job. Reevaluating the safety of the building and electrical equipment within, the plant floor infrastructure, and your employees is a must. For many this includes replacing aging electrical equipment and outdated electrical power systems. In tandem, as OSHA’s rules have continued to change, manufacturers must keep pace when it comes to electrical risk. In the past, you could conduct an arc flash study to evaluate and identify risks and that was considered sufficient.
Today, you must conduct the study, perform testing to ensure the equipment reacts appropriately in the event of an arc flash, as well as conduct regularly scheduled maintenance. Otherwise, that could be a serious violation. There is a lot of cost associated in these instances as organizations invest in updating equipment and mitigating safety concerns, but without it out they face substantial risk – financial and otherwise.
All of these efforts coincide with the demand for greater reliability of the power network itself. In a competitive global marketplace, uptime has never been more important. As such, manufacturers are exploring the power of data capture to glean better insights about system uptime. Today it’s possible to quickly gather digital data about everything that is happening on the plant floor and power systems are a primary source of information.
Solutions can identify how specific equipment and power systems are performing in certain instances and over time. By gathering that data in a continuous real-time cycle, manufacturers can identify areas of concern, prioritize new equipment investment, and improve their uptime. This directly impacts their goal of providing a manufacturing environment that is as sustainable, safe, and reliable as possible.
Marc Elliott: Industrials the world over are focused on safety, sustainability, efficiency and controlling energy costs. Electrical safety is a primary consideration, longtime focus and ongoing continuous improvement effort vital to achieving organizational objectives. Sustainability and environmental, social & governance (ESG) goals are driving the desire to integrate renewables, which adds complexity to energy systems. As electrification takes off, finding ways to drive efficiency and control energy costs is vital. The best energy is the energy you don’t use. At Eaton, we’re making sustainability gains with improvements to safety, electrical resiliency and cost in our operations and for our customers.
Question: Are you incorporating electric vehicle (EV) charging stations, and if so, what power pros and cons have you come across?
Ken Crawford: Yes, the distance to charging stations from the distribution point was lengthy, so a voltage drop was needed to be considered. The cost of trenching also was a factor as well as permitting. Chargers are consolidated into one area, which means all EV vehicles have to park in that area.
Question: Is your facility implementing microgrid or renewable power systems? Describe the project.
Ken Crawford: We are planning to install a 175 kWdc rooftop solar photovoltaic (PV) system, Utilizing 350, Trina Solar 500W Solar Panels. This system will produce approximately 218 MWh/year and has a maximum efficiency at >98.5% for inverter and 99.5% for optimizers. Installation is planned for late 2024. The system is expandable up to 650.5 kWdc, providing 845 MWh/year in the future.
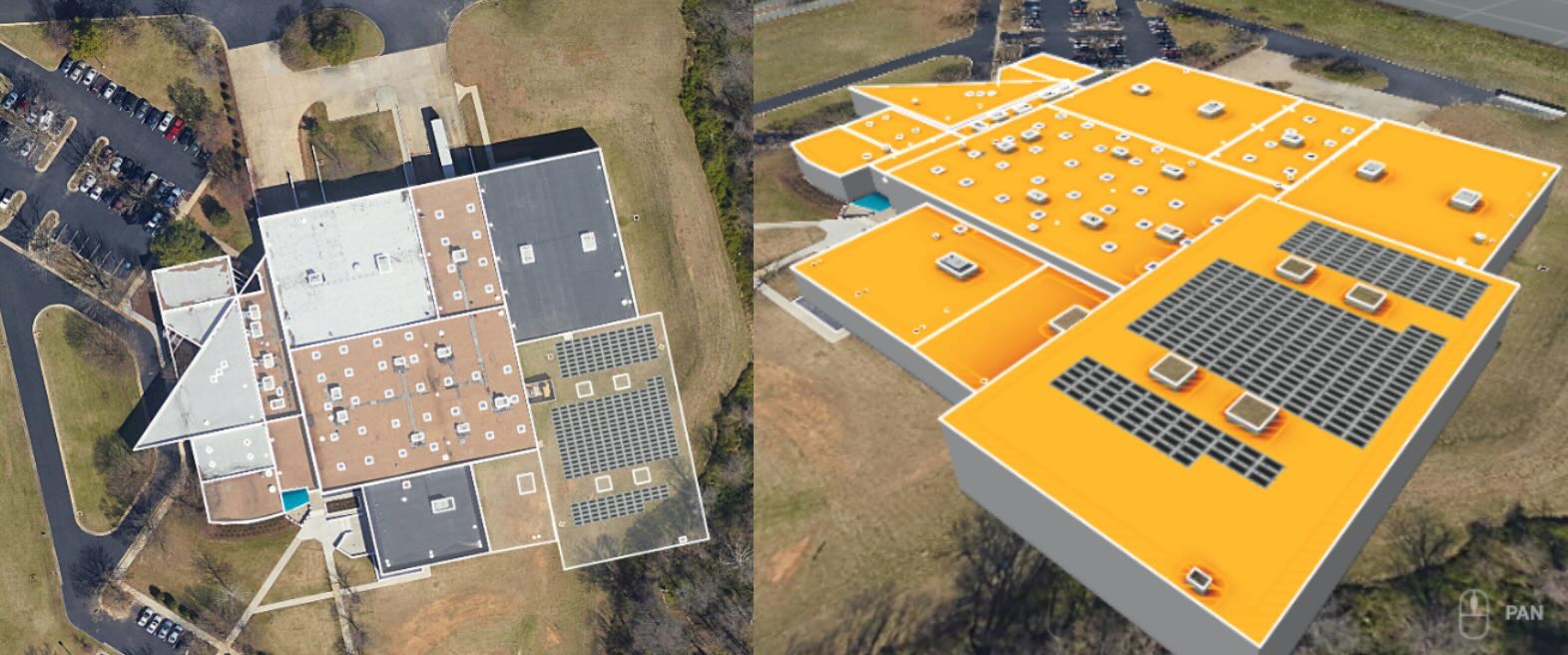
Marc Elliott: At Eaton, we have a longtime commitment to sustainability and are focused on accelerating the energy transition. We’re simplifying the safe integration of renewables — at our facilities and for customers. For example, a nearly decade-old solar installation at our Beaver, Pa., plant continues to provide reliable and clean power. In Puerto Rico, we’re building microgrids at manufacturing plants in Arecibo and Las Piedras. These clean energy projects will reduce emissions by 8,345 metric tons in the first year of operations, while strengthening resilience with the ability to withstand extreme weather emergencies.
Question: Tell us about a recent project you’ve worked on that’s innovative, large-scale or otherwise noteworthy. Please tell us about the location, electrical systems your team engineered, key players, interesting challenges or solutions and other significant details.
Scott Dowell: We’ve helped multiple manufacturers address their most pressing demands for energy sources. For example, one of our customers had the goal of becoming the first to market in their carbon capture venture. To do so they needed to have a test/demo facility supported by 15kv energy. Unfortunately, the project site that they purchased had an existing 35-year-old switchgear line up that had been out of commission for five years. Given their go-to-market plan, the customer could not wait for the new Switchgear line up as they faced a 70-week lead time. We were able to refurbish, repair, retrofit, test and re-engineer aspects of the switchgear in 12 weeks, saving them valuable time and supporting their primary business objective.
Question: What tips would you offer to someone tasked with ensuring the power system is flexible?
Marc Elliott: While there is no one-size-fits-all approach, flexibility requires greater control over infrastructure through digitalization and decarbonization strategies enabling more possibilities for affordably integrating energy sources. Microgrid systems are a powerful lever to increase resiliency and helping prepare for the unexpected by balancing where, when and how electricity is obtained.
Getting started requires an understanding of your goals and existing infrastructure; a power system study performed by microgrid experts provides vital insights on how to balance power demand, utilize existing assets, and plan for new onsite energy resources over time. Note an energy-as-a-service financing shifts microgrid investments from CapEx to OpEx.
Question: What power technologies within the manufacturing plant are you helping implement?
Scott Dowell: Wesco helps to implement power technologies from the meter all the way through each piece of equipment, to automate the entire power distribution system. From electrical safety programs to low voltage communications to cutting edge Industrial IoT (IIoT) applications, we understand the nuances of electrical power systems.
This is especially critical as the landscape for how to best stay safe on the plant floor continues to evolve. For instance, OSHA recently put in place a new requirement (70B) which targets electrical equipment maintenance and specifically electrical switching. Built off the standard from the National Fire Protection Association (NFPA), the goal is to ensure that electrical switching mechanisms aren’t just in place but truly work the way in which they were designed. It’s about protecting the overall safety of the systems as well as the employees who work with them. While 70B was already a recommended practice, the newly minted requirement reinforces the importance of identifying electrical safety risks on the plant floor.
As manufacturers evaluate how to best achieve electrical power safety in their factories, many come to us to help replace or retrofit older technology. Smart metering is one example. By leveraging sensors, IoT technology, and data analytics, we can identify how and when power is being consumed so manufacturers can in turn leverage power consumption outside of peak times to create a much more sustainable flow of power. A byproduct of the newer systems is better safety for the employees as they aren’t forced to contend with outdated and potentially dangerous systems.
Justin Mitchell: We oversee the implementation of electrical safety programs and standard operating procedures. As online grocery shopping continues to gain popularity across the nation, the need for additional storage space becomes increasingly imperative. To address this, we propose expanding the freezer capacity in our manufacturing plants. This will enable us to augment the existing square footage of the freezer storage facilities. In doing so, we will be able to provide our customers with the highest quality products while ensuring efficient and effective storage solutions.
Question: How do you educate and train personnel to promote a safety culture when working with electrical systems?
Justin Mitchell: In-house training is held on at least a monthly basis and is open to employees. Training materials are maintained up to date with current industry/OSHA standards and in compliance with company guidelines. All employees are required to undergo training on at least an annual basis.