USC Viterbi researchers created a control algorithm that allows quadruped robots to adapt to unknowns in their environment, making them better-suited for delivering packages and other items in warehouse and other areas. See video.
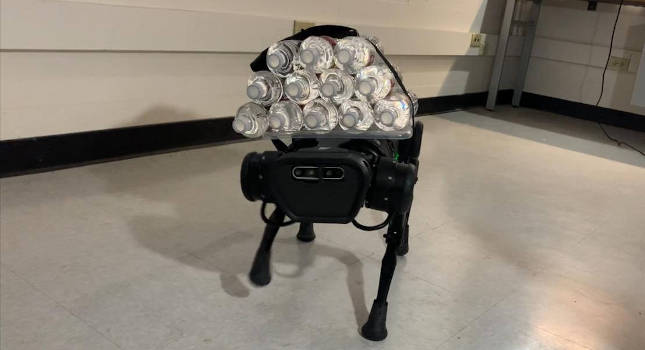
Increased package deliveries, especially in pandemic times, can put an undue stress on mail carriers and warehouse workers. But what if they could get help from some four-legged friends?
Led by assistant professor Quan Nguyen, USC Viterbi doctoral students Mohsen Sombolestan and Yiyu Chen created a control algorithm that allows quadruped robots to adapt to unknowns in their environment. Unlike their predecessors, these robots use an adaptive control model that can compensate for changes from the baseline, allowing them to move adeptly while carrying heavy weights and traversing sloped or uneven ground.
“We have no idea how the robot will interact with obstacles or with a force, like if someone pushes or pulls on it, or adds a weight,” Sombolestan said. “That is why we needed to amend the control framework, so the robot can operate smoothly in different conditions.”
Nominally, a four-legged robot—without any load—has been able to move across smooth terrain relatively well, as shown by this robot from Nguyen’s lab. This is because the environment is largely predictable and the robot can be programmed to move the same way every time. However, more realistically, a robot might experience different forces—a weight on its back, a push or pull from another object, a bumpy road beneath its wheels. These unknowns can be difficult to account for in real-time, and this is the problem the researchers worked to solve.
“The baseline or nominal conditions for the robot are compared with the real-life conditions the robot is facing,” Nguyen said. “The governing algorithm [which dictates how the robot operates] then calculates the differences between baseline and real-life metrics to correct for differences in force or weight. This allows the robot to adapt as it carries a package on its back or walks up an uneven path.”
Sombolestan said this control framework would be ideal for robots used in collaboration with humans, particularly in instances where load-carrying is required, like delivering packages and moving goods between spaces in a warehouse. This could be particularly helpful during busy periods, like after Black Friday, or even during situations like the pandemic, where online shopping has surged.
These robots can also be used in conditions that are too dangerous or difficult for humans to navigate, for instance in a fire or a natural disaster where emergency equipment or kits need to be delivered.
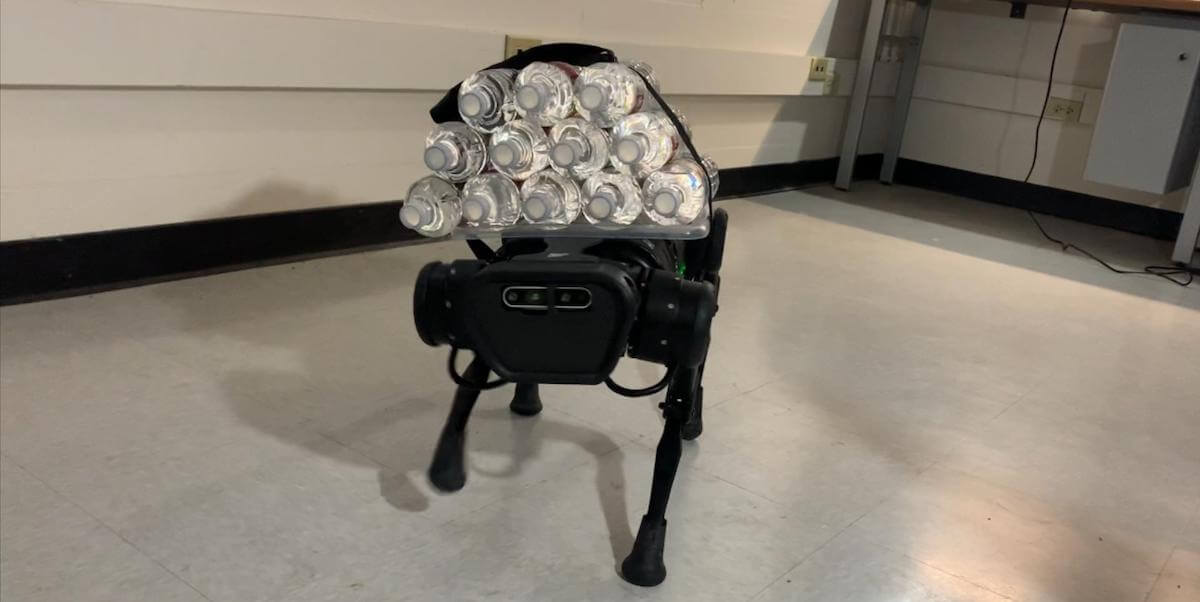
A robust locomotion system
“Even having a robot stand with a heavy weight on its back is a big challenge — and a big accomplishment,” Nguyen said.
To truly advance the robot’s locomotion, the researchers looked further. Instead of just settling for a robot that could stand up with a heavy weight on its back, they designed an algorithm that allows the robot to move around rough, uneven or even sloped terrain while carrying weight. The robot adjusts to its environment continuously, like an actual four-legged animal might.
The research team has developed advanced algorithms based on adaptive control to offer the following advantages: robustness to uneven surfaces, ability to manage friction within certain constraints and softening of impacts on the robot’s locomotion. The novel framework was validated in both computer-based simulations and in live hardware experiments. In both cases, a 26-lb. robot was used along with a 13-lb. load (water bottles that made up 50% of the robot’s weight). Standing on four legs, the robot was able to carry up to 92% of its weight—24 lbs. on its back.
Of course, there is room to grow. In future research, the researchers hope to account for weight in other directions, for example a force coming from behind or in front, like a massive gust of wind or guidance from a human hand. They will study how to make the robot jump or run with a heavy weight on rough terrain, as well.
– Edited by Chris Vavra, web content manager, Control Engineering, CFE Media and Technology, [email protected].