Digital data consistency is beneficial for consistent processes in control cabinet construction.
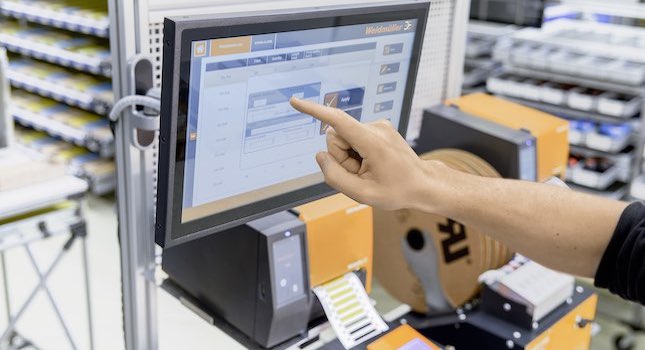
Control Cabinet Insights
- When it comes to manufacturing control cabinets, manual intervention should be minimized due to human tendencies toward errors.
- Digital data consistency helps create a standardized documentation, which can be created almost automatically.
Important phases in the manufacturing process of control cabinets are the design and manufacture. In view of growing challenges, these phases consume important resources in the control cabinet construction industry. During the design phase, half the time is spent on project planning and the preparation of circuit diagrams.
Designers planned the control cabinet on the PC and then printed circuit diagrams and parts lists for use in the workshop. There, the data was manually entered at the workstation, which is a major source of error due to typos. Control cabinet manufacturers need to check the dimensions and cable quantities, which ends up prolonging processing times.
Fewer manual processes reduce errors
To prevent these errors from occurring, manual intervention should be kept to a minimum. This can be done by digitally capturing and transmitting data – starting from order intake and project planning. By ensuring end-to-end digital management of the process, efficiency and productivity can be increased, saving time. This is because data can be exchanged via defined interfaces between the E-CAD software used in the design of control cabinets and computer-aided engineering (CAE), product data management/product lifecycle management (PDM/PLM) or enterprise resource planning (ERP) systems.
In this way, the current data from the design department is available in digital form across all work steps. This data consistency not only simplifies engineering through to assembly, but it also the complete documentation in the individual production steps to spare parts management.
Improved quality thanks to consistent data
Digital data consistency enables faster time-to-market and increases security in the manufacturing process. This can be a competitive advantage. If everyone involved in the process chain can access the same current data, certain sources of error – such as typos or changes that have not been transferred – can be completely avoided. Manual input is reduced to necessary entries, such as starting the next program step on the machine. A study by the Institute for Control Technology at the University of Stuttgart showed consistent digital data management can increase efficiency by up to 43%.
Digital data consistency, which ranges from incoming orders to the finished products and logistics, facilitates a standardized documentation, which can be created almost automatically. Despite a shortage of skilled workers and increasing time pressure, processes can be accelerated and quality requirements fulfilled simultaneously. If a customer encounters a problem, it is easier for the after sales service to react to it. They can access the documented data and retrace the cause of a problem.
Conclusion
Digital data consistency is the basis for consistent processes in control cabinet construction, allowing for efficient, fast and high-quality production – even for batch sizes of one. In addition, users not only save material but also time.