This example of a manufacturing plant, lab and office building power distribution project walks through the electrical engineering decisions
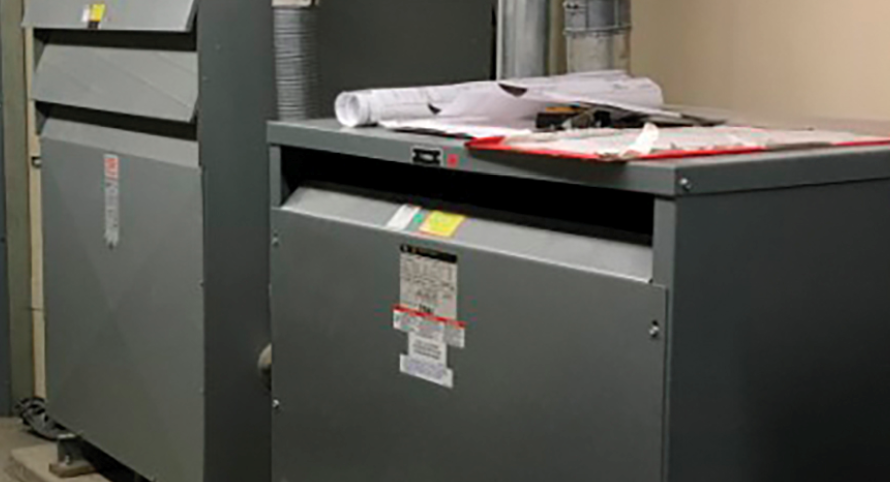
An equipment manufacturing company has procured an existing building with 277/480-volt wye service to open a new office for its business. The company manufactures and tests specialized, sensitive electronic equipment for the health care industry. It is opening a new location for its operations and plans to use 80% of the space and power capacity with a requirement to allow for at least 20% growth in the next few years.
Project scope consists of standard commercial office space as well as a portion of laboratory and manufacturing. The owner’s required power allowances are: 10 volt-amperes per square feet for office, 25 volt-amperes per square feet for lab and 20 volt-amperes per square feet for manufacturing areas. Upon receiving floor plans, the areas are 14,000 square feet of office, 8,000 square feet of lab and 120,000 square feet of manufacturing.
Lastly, all office and lab spaces will need 120 and 208 volts single-phase distribution, manufacturing requires a 70/30 split of 277/480 volts (single- and three-phase) and 120/208 volts (single- and three-phase), respectively. From this information and criteria, the connected load power allowances are determined:
- Offices (120/208 volts): 10 volt-amperes/square feet x 14,000 square feet = 70 kilovolt-amperes
- Laboratory (120/208 volts): 25 volt-amperes/square feet x 8,000 square feet = 96 kilovolt-amperes
- Manufacturing (277/480 volts): 20 volt-amperes/square feet x 120,000 square feet x 0.7 = 1,680 kilovolt-amperes
- Manufacturing (120/208 volts): 20 volt-amperes/square feet x 120,000 square feet x 0.3 = 720 kilovolt-amperes
The next stage is to select transformer capacity sizes. Office spaces can be served from a 75 kilovolt-amperes transformer based on the next standard size of transformer and the calculated connected load. However, the owner’s requirements are to account for at least 20% growth for future. Once the growth amount of 1.2 for the office space is factored in, we arrive at 84 kilovolt-amperes. This connected load will need to be serviced by the next standard size, 112.5 kilovolt-amperes.
The laboratory space requires 115.2 kilovolt-amperes (with the 20% growth included) and will require a 225 kilovolt-amperes transformer. Manufacturing will similarly require a 1,000 kilovolt-amperes transformer to service its 864 kilovolt-amperes (with growth accounted) connected load at 120/208 volt distribution.
Now that loads are accounted for, general locations in the building can be considered. There are many means and methods to determine appropriate transformer locations and distribution, so one design philosophy described here. The building layout is rectangular. Overall dimensions are 200 feet wide by 655 feet long, with a second story at the building front that will house offices and laboratory spaces.
Because the labs and offices reside in the same area, consolidation of the lab and office loads to one transformer are considered. This will give a combined connected load of 166 kilovolt-amperes that can be serviced by a 225 kilovolt-amperes transformer.
One larger combined transformer allows for space and cost savings. Instead of two rooms at either side of the building with associated feeders, the single larger transformer can be centrally located. In this scenario, with the labs and offices on two floors that are relatively small, the transformer is placed at grade level to avoid potential structural impacts.
Distribution for the manufacturing floor requires additional consideration. With the 120/208 volt demand spread throughout the floor space, transformers must be arranged to avoid excessive voltage drop. With a 600-foot-long run and assuming somewhat uniform distribution, two locations are planned — one at 200 feet down and another at 400 feet. This will cover the manufacturing floor and will allow the load to be split for the manufacturing area to 360 kilovolt-amperes, allowing two 500 kilovolt-amperes transformers to service either end of the manufacturing area.
These loads are only rough estimates, but allow the design team to prepare and allocate floor space. Once demand factors (if any) are applied, the sizes may be revisited and sized accordingly.
Lastly, the specification of the transformers is considered. Because this is an indoor and controlled environment, dry-type ventilated transformers will be used. To reduce cost, the windings for the transformers will be aluminum instead of copper. At the office and labs, harmonic mitigating transformers are considered due to the sensitive nature of the equipment in the facility. This selection also will help increase power quality and reduce inefficiencies, in the form of harmonics, introduced from the multitude of AC/DC power supply transformers common to modern computers and electronics.