Applied Control Engineering Inc., is the 2021 System Integrator of the Year for the Mid-Sized System Integrator Category. Ian Burns, PE, president of ACE, discussed how the company is finding new ways to work with companies during the COVID-19 pandemic.
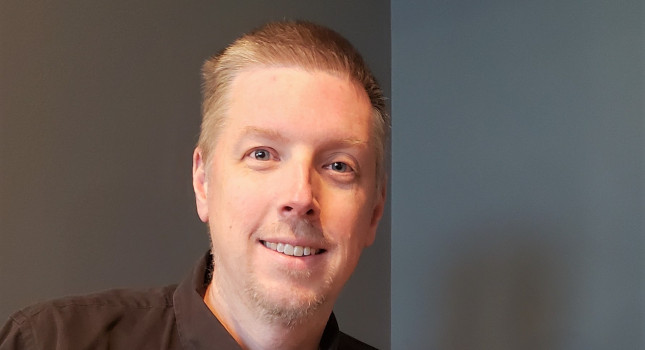
Applied Control Engineering Inc. (ACE) believes in helping its customers achieve enhanced productivity through automation. CFE Media spoke with Ian Burns, PE, president of ACE, about the company’s customer relationships and how ACE is finding new ways of working together and preserving its team approach when dealing with customers throughout the COVID-19 pandemic.
CFE Media: Congratulations on receiving the 2021 System Integrator of the Year award. Talk about what this kind of recognition means to you and your team.
Ian Burns: It is an honor to receive this award and it could not have come to us at a better time as Applied Control Engineering Inc. (ACE) begins to celebrate our 30th anniversary. The award is primarily a testament to our employees whose hard work has been an integral part of building the company we have today and will continue to be what drives ACE’s continued growth and successes into the future.
The original ownership of ACE also deserves a lot of credit and this award is as much for them as it is us. Thirty years ago, they set up a company with the idea that they could create an enjoyable place to work while helping its customers achieve enhanced productivity through automation. This remains a core tenet of our business today.
CFE Media: Talk about IT/OT convergence. Are end-users “getting it?” What is Applied Control Engineering doing to help ease IT/OT convergence anxieties?
Burns: The convergence of information technology/operational technology (IT/OT) traces its roots back to the early part of the 1990s when the first Windows-based machines started taking the place of proprietary consoles. As we moved through the early to mid-2000s, Ethernet communication started becoming a standard in programmable logic controller (PLC) and distributed control system (DCS) architectures, and single operator consoles started giving way to client/server implementations. It was then that cybersecurity concerns started to be raised. At that time, the plant floor either ignored the issue or relied on “air gaps” to protect the manufacturing space.
Now, with the advent of the Industrial Internet of Things (IIoT) and the requirements to get real-time contextualized data into the hands of key personnel, the demand is larger than ever for connectivity to the plant floor using standards that are easy to use and easy to commission.
Our customer base lies across a vast spectrum when it comes to the adoption of IT/OT convergence and cybersecurity. Generally, though, ACE has seen a much greater awareness and sophistication develop in this space over the last five years. Those that are demanding the data seem to realize that the data that they are consuming is only one side of a double-edged sword when it comes to cybersecurity.
ACE has done the following:
- Implement good OT design in projects by specifying proper hardware, network design and configurations. User requirements for data access and a system architecture are critical first steps for a project. Using the requirements, we can start fleshing out the system architecture to implement a network design that meets the customer’s needs and cybersecurity requirements after which we can select the proper hardware and then configure it properly.
- Bring OT knowledge to plant personnel who may not be aware of what OT means. Many good automation professionals are focused on solving the problems of keeping their plants running and haven’t had the chance to become experts in the IT/OT convergence. By having experts who can help bring them up to speed, we have helped them enhance their skills.
- Train IT professionals in the world of OT. Whether that be formal training, working out the IT/OT interface requirements or just sitting down during a project and helping the channels of communication between IT and OT, being able to speak to both sides places us in a situation to help the customers.
- Develop and implement standard operating procedures (SOPs) for maintaining the OT space including patch management, antivirus, white listing, network intrusion and authentication and authorization. By having these SOPs, IT sees that OT is not that different from what they know and that there can be commonality for both sides.
CFE Media: What are some of the effective ways your customers are using IIoT technology in manufacturing?
Burns: IIoT carries such a broad meaning for individuals in manufacturing. That data might be useful for a plant manager, a reliability engineer, process engineers or even executives. If you don’t know your audience, you aren’t going to be able to make sure the right data is presented in the right way. The information a reliability engineer needs from IIoT is different than the information an executive needs even if it is based on the same underlying sensors and data.
Some of the creative ways our customers are using IIoT technology in their manufacturing environments include:
- Determining causes of downtime within production lines. This information lets them figure out where to allocate resources. Those resources might be training time for operators, maintenance effort to ensure breakdowns do not happen in the future or engineering resources to redesign the production line.
- Gathering information about chiller and boiler performance to optimize usage of the assets and reduce operating costs. By collecting information around these assets, our customers are performing regular optimization calculations to determine the right load for the assets and whether to bring additional assets online.
- Adjusting temperature setbacks in unoccupied rooms during evening and weekends and presenting those savings to not only plant management but also to the operating staff so they can see the savings that can be realized through changing their behavior.
CFE Media: How are you working with your clients to facilitate their continuing operations during COVID-19? How engaged are they on this journey?
Burns: COVID-19 is one of the most transformative challenges we have faced in recent history. It has challenged many of the beliefs we have held regarding how we run a business and how we execute our projects. If we must find a silver lining in the pandemic, it is probably that we have found new ways of working together and preserving our team approach when dealing with customers and working to meet their needs.
Something that has not changed is that communication continues to be the cornerstone of our successes. Virtual meetings and acceptance tests have replaced in-person communication with our customers and new levels of flexibility and vigilance is required when onsite to ensure the safety of others.
Like many integrators out there, we have had several onsite support and commissioning activities derailed by a COVID-19 exposure. In every instance, we have been able to work with our customers to retool the plan, reset expectations and get the project back on track.
CFE Media: Relating to the previous question regarding COVID-19, how has remote monitoring and/or remote automation applied to the way you engage with your clients?
Burns: ACE has been using remote access since the 1990s to provide remote support to our customers. Gone are the days of dial-up and 33.6k, but the principle remains the same. Prior to COVID-19, remote access provided several advantages to the customer when it comes to their systems:
- Recovery from a downtime event: The faster a line or process can come back online, the less loss there is from a cost standpoint. With remote access, an engineer can be online with a system in minutes. When the cost of downtime is measured in dollars per minute, even the savings of a short trip to the site can be significant.
- Make small changes from anywhere: With remote access, small changes and feature enhancements can be made to a system that is down the street or four hours away.
- System review: A remote system review for the purposes of documentation or cost estimate for a system upgrade is becoming more common.
With the onset of COVID-19, there was an amplification of these advantages. Customers who had remote access were able to get support even during the first couple of months when lockdowns were prevalent and travel restrictions were enforced. We had several instances where ACE provided remote startup support while a minimal team operated as boots on the ground.
Customers that did not have remote access, for reasons of security policy or a lack of technology were in a different situation. In some cases, we saw customers re-evaluate policy and methods put in place to grant access (temporarily). ACE also helped several of our customers implement new methods for remote access over the last six months.
Finally, we have seen an uptick in the usage of information portals and projects involving bringing real-time plant floor data to the cloud. Sometimes this involved additional reporting while other times our customers wanted to be able to easily see read-only process graphics, just as they could if they were in the plant.
CFE Media: In your opinion, what is the role of the system integrator in the digital transformation?
Burns: For digital transformation, the system integrator needs to be as much of a guide as an implementer. Technology in the automation space is moving extremely quickly and there are so many possible places our customers can spend their time and money; they need an advisor who can help guide them along that digital transformation journey. If they do not have someone to help them, they can become overwhelmed, lose focus and become paralyzed with myriad choices.
System integrators have a unique perspective because they have staff members who can specialize in separate areas of the digital transformation and not be limited to what a single person knows or can handle. Not only does the digital transformation include IIoT, but also includes digital twins, analytics, artificial intelligence (AI), robotics, additive manufacturing and other technologies. By bringing to bear a team of experts, the system integrator can listen to the manufacturer’s needs and then pull the best solutions from multiple suppliers together to meet those needs.
CFE Media: Applied Control Engineering faces the same workforce development challenges as others in the manufacturing sector. Talk about your programs to meet this challenge, and also talk about the young people entering this industry. What are their expectations, and how can system integrators have greater success in attracting and retaining these workers?
Burns: For ACE, employee retention and a highly skilled and engaged workforce are critical components of long-term viability and a significant portion of our competitive advantage. We have a three-prong approach to help us achieve greater success in both attracting and retaining top talent:
- Culture: We begin by introducing prospective employees to our company culture during the interview process. We want those entering our workforce to know that their voice is heard and valued and that they also have a good understanding of the career opportunities that are available to them within the company.
- Communication: It is obviously important to have methods and means of communication from management to engineering and between engineering and sales and so on. We also know from experience that some of the best ideas that can be implemented can come from the newest employee. As ACE has grown, we have found this to be more of a challenge. Very recently and in response to the pandemic, ACE started introducing town halls where employee questions are discussed in an open forum.
- Career development: It is important to provide training opportunities and make room for engineers to be challenged by the work they have. Training opportunities include formal training, opportunities to be mentored by a subject matter expert or lunch and learn sessions with our distributor and manufacturer partners. Growth, as part of career development is something that is important to all our employees, as well as new recruits.
The key to success is to continuously review what you are doing, measure how effective it is and take steps to make improvements. We have found that there is always room to do better.
CFE Media: Talk about a recent customer success. What were some of the things you learned in success with the customer?
Burns: Customer success takes on many different forms, whether it is a huge return on investment on a capital project or if it is just letting the plant automation engineer sleep through the night without receiving a call about a problem in the control system.
One project we recently finished was for a customer modernizing its control system in a chemical plant with 15 reactors and associated processing equipment. The modernization took almost five years from the initial project conception to finally removing the last bit of the obsolete DCS. It was very much a digital transformation for the site and ACE was there to help them along the entire journey.
The site had an aging workforce and a new site control engineer partway through the project. To help address the aging workforce and capture the operator’s knowledge, we held extensive testing through the process and let the operators try out little bits of the control system. It was at those regular sessions when the operators would pose new scenarios and we were able to add in additional features to account for situations the previous control system had not handled gracefully.
The customer knew it needed to transform the way the automation system worked. ACE was able to introduce industry standards such ISA-88 and ISA-101, a digital twin for operator training and system checkout, updates to its virtualization structure, enhanced reporting and new recipe flexibility.