Automation can help optimize industrial operations, as noted at ROKLive, a recent conference on industrial operations, maintenance, engineering, and enterprise-wide solutions automation, linking operational technology (OT) and information technology (IT).
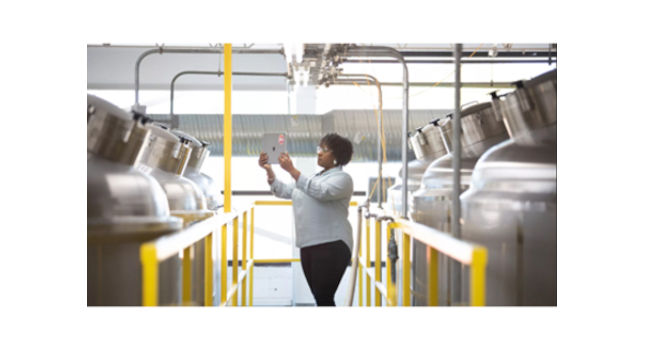
Learning Objectives
- Automation helps manufacturers expand when skilled workers are unavailable.
- Digital transformation tools can help.
- AI and virtual reality help with optimization and training.
Advice about how automation can help optimize industrial operations was available at ROKLive 2022, a June 13-16 conference from Rockwell Automation and newly acquired Plex Systems, covering industrial operations, maintenance, engineering, and enterprise-wide solutions automation linking operational technology (OT) and information technology (IT). Information below was summarized from 125 ROKLive2022 session descriptions.
1. Build an effective cyber resilience strategy: With cyberattacks causing unplanned downtime, contributing to supply chain shortages, and leading to ransomware attacks, manufacturers need to build a cyber-resilience program, according to Brian Deken in the session, “Cybersecurity Peer Exchange: Building an Effective Cyber Resilience Strategy.” To do so, Deken said, develop the right balance when considering preparation, process improvement, technology investment and risk mitigation. Manufacturers can prepare to respond to threats that extend beyond their organization, often targeting their vendors and supply chain, Deken said. Attention to defense-in-depth (DID) cybersecurity, networks and infrastructure can help enable devices to protect themselves from malicious attacks focusing on authenticity, integrity, and confidentiality, said Roch Mikolajczyk and Jack Visoky in two sessions, “CIP Security Advanced Session: Experience the Effect of Security on Your Control System” and “CIP Security Advanced Session: Experience the Effect of Security on Your Control System.”
Understand control system readiness to apply new cybersecurity technology. Learn how introducing additional security measures impacts control system performance and operational productivity. Industrial network security, modern software tooling and innovative hardware solutions bring device security to the control system. Careful migration steps can ease introduction of security to the plant floor.
2. Original equipment manufacturers (OEMs) can achieve better profitability, productivity, and customer satisfaction. OEMs involved with engineering, information technology, automation management and operations management understand that project timelines have shortened and speed to market is paramount. Tolerance for unmitigated design and commissioning risk has all but disappeared. Cybersecurity threats, workforce productivity and skill gaps require ongoing vigilance. Leveraging digital transformation can help OEMs move past the tipping point to achieve new revenue streams and customer satisfaction, according to Stephen Pulsifer, Rockwell Automation, and Rob Ponsonby and Daniel Seger in the session, “OEM Peer Exchange: Achieving Better Profitability, Productivity and Customer Satisfaction.”
3. In water and wastewater applications, water sustainability initiatives are driving use of smart automation for industrial users and water utilities. Acceptance of digital transformation in the water industry is increasing as water and wastewater treatment plants become integrated into smart cities and manufacturing to address the sustainable use of water. Digital transformation is crucial for sustainability in water operations, according to Kelvin Hurdle and Ali Rose, in the session, “Water Wastewater Peer Exchange: Water Sustainability Initiatives Drive Smart Water Adoption for Industrial Users and Water Utilities.”
4. Sustainability and environmental, social and governance (ESG) are increasing in importance for manufacturing. Smart manufacturing software for manufacturing execution systems (MES), quality management systems (QMS) and supply chain planning (SCP) helps sustainability and ESG initiatives, which, in turn, helps manufacturers save money, provide purpose, and attract talent, explained Gerry Abbey, Plex Systems, in the session, “The 2022 State of Smart Manufacturing Report: Key Findings.” MES software is more powerful, has more capabilities, and embraces smart manufacturing to support the 4th industrial revolution in all its forms, added John Clemons, Maverick Technologies, in the session, “Today’s MES: Embracing the Technology of Smart Manufacturing.”
5. The supply chain crunch continues to squeeze operations management for food manufacturers. In addition, frequent new recipes, new packaging and new restrictions require that food manufacturers are constantly reinvent business processes frequently. Upgraded software helps with supply chain pressures, new product development and market growth, suggested Ara Surenian, in the session, “Navigating the Supply Chain Crunch.” Using recipe management software can tighten control of inventory and improve quality and share critical information among systems, added Pat Welsh in a “Recipe Management Integration” session.
6. Real-time operations visibility helps with continuous improvement initiatives. Smarter analytics and data management tools help those in information technology and operations management gain actionable insights into a line, plant, and enterprise-wide operation. Tools include self-service, interactive storyboards used to explore manufacturing data and improve productivity and efficiency without relying on information technology (IT) resources or expensive data warehouse infrastructures, explained Amanda Thompson and Victoria Bruce in the session, “Achieving Continuous Improvement with Real-time Operations Visibility.”
In addition, digital insights help maximize asset utilization, said Ashley Reyes in the session, “Maximizing Your Asset Utilization with Digital Insights.” Asset data is just data until the right platform is in place to apply it. Turn data into insights to make better, more informed decisions about assets to improve overall performance and reduce risk. Track and analyze data from the production environment to develop the right plans and strategies and make data-driven decisions that help drive the most critical business outcomes.
7. Enable remote operators to increase workforce productivity. Remote operators help operations management, information technology and automation management. Physical location availability challenges manufacturing, but even with regulations on safety and safe distancing, productivity can increase, according to Kris Dornan, Al Letourneau and Tom Jordan, in the session, “Visualization: What’s New and What’s Next.”
8. Capture operational process data for better analytics and data management. Those in IT, engineering, operations and management can benefit from historian software “to gain supervisory control, performance monitoring and quality assurance,” explained Paul Haikal. The session, “Capture Operational Process Data with FactoryTalk Historian,” explained that manufacturing historian software quickly captures operational process data from multiple sources while scaling from machine to enterprise, he said.
9. Artificial intelligence (AI) applied in automation is helping enterprises to increase autonomous operations. Digital transformation helps companies augment legacy control strategies with prescriptive machine learning capabilities to achieve greater production throughput and yields, said Mithun Nagabhairava in the session, “The Autonomous Enterprise: How AI is Advancing Automation to Autonomy.”
10. Digital transformation is making manufacturing smarter, just in time. Adversity in the form of skilled worker shortages, supply chain disruption, and risk mitigation are challenging the norms of manufacturing. New and upgraded technologies are helping companies resolve these ongoing challenges, said Gerry Abbey, in the session, “The 2022 State of Smart Manufacturing Report: Key Findings.”
11. Drive higher margin with operational rigor and data visualization. A suite of manufacturing solutions helps govern operational behavior and increase the accuracy, output, and visualization of data to increase margins, drive more efficient operations, and automate business processes, explained Jodi Hunt. Achieving manufacturing objectives while planning digital transformation requires modern, secure machine control with increased uptime, quality, and cost efficiency. A well-planned visualization system can enable growth and efficiency today, while preparing a plant for the flexible operations and analytics of the future, said Sue Burtch and Kim Kyanka, in the session, “Achieve Your Modernization Objectives with Centralized Visualization.”
12. Transform production with the digital twin. Manufacturing leaders across industries are embracing digital twin solutions as a core part of a digital transformation strategy, said Leo Moran and Brian Ding, Kalypso, in the session, “Transforming Production with the Digital Twin.”
13. Virtual commissioning uses 3D emulation software to make digital engineering more productive. Software can help develop and debug control code before automated equipment is even built. Connect a programmable automation controller to a 3D digital model of the equipment using emulation software. Simulation can reduce investment risks, improve time to market and increase understanding using a virtual reality immersive experience, said Tyler Phillips, Rockwell Automation, and Antoon Lane, in the session, “Virtual Commissioning Using Emulate3D Software Demonstration.” Digital workers using augmented reality tools for procedural information, to replace outdated manuals and prepare a new generation of workers, said Hector Jimenez, in “A Day in the Life of a Digital Worker: Augmented Reality Use Cases.”
14. Simplify lifecycle management of assets. Do you know when assets are near the end of life? When they need patching? What assets, versions, series, and software are in the plant? Keeping the system current has never been more important, but the scale of that task continues to grow in size and complexity, said Dave Rapini. Software helps manage assets as a service that can be included with the latest process control software, in Rapini’s session, “PlantPAx System ID: Simplify Management of Your Assets Lifecycle.”
15. Process automation software can combat the skilled workforce shortage. Manufacturers globally are finding it harder to find skilled workers, leading to unfilled jobs and high training costs. Tony Kaczmarek, Plex vice president of product management, explained how automating processes can help fill the worldwide shortage of skilled manufacturing labor, in the session, “Combatting the Skilled Workforce Shortage with Process Automation.”
– Edited by Mark T. Hoske, content manager, Control Engineering, CFE Media and Technology, [email protected], using information from Plex Systems and Rockwell Automation.
KEYWORDS: Automation, digital transformation, cybersecurity
CONSIDER THIS
Are you using advanced, automated digital tools to improve manufacturing operations?