Cable quality and usage are factors in making the best choice during installation.
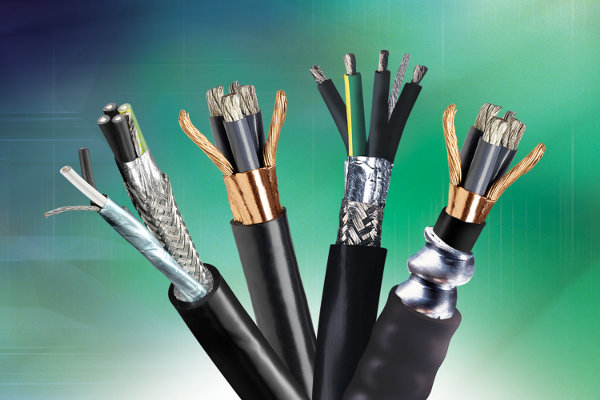
Variable frequency drives (VFDs) make practical and environmental sense for both discrete manufacturing and process plants. VFDs allow the speed of a 3-phase ac electric motor to be altered to meet variations in demands (such as temperature, pressure, or force) from, for example, a pump, fan conveyor belt, or lathe.
VFDs reduce waste—of both material and energy. They can control motor speeds to within 0.1% tolerance to reduce scrap. They also offer significant energy savings: at half maximum speed using a pulse width modulation (PWM) VFD, a motor consumes roughly one quarter of the energy required to run at full speed. In addition, VFDs reduce wear-and-tear, resulting in lower maintenance costs and longer motor life.
When choosing components for a VFD system, one carefully selects the motor and drive components based on the operating requirements, which typically include the load, torque, speed, and power required. Cabling requires no less thorough evaluation. The entire VFD system (drive, cable, and motor) needs to be matched for a successful operation.
VFD cabling considerations
VFDs require purpose-built cable to address the sensitivities of a VFD system, which fall into four categories: noise emissions, voltage reflections, overvoltages, and corona discharge.
Noise emissions: The transistors in PWM VFDs that switch rapidly to accommodate an abrupt speed change in a motor can have a downside—the generation of unwanted noise in the drive system cable and in the drive itself. Absent purpose-built cabling, noise emission from a drive system cable can disrupt operations.
Voltage reflections and overvoltage: When the cable is not properly matched to the motor and VFD, voltage reflection can lead to motor and cable failure. Peak voltages of up to 2.5 times the nominal system voltage can be generated, causing havoc in the system.
Corona discharge: Cables in VFD systems are at risk from high voltage levels leading to corona discharge between conductors. This effect can damage not only the cable itself but also the motor, motor bearings, and the drive.
Because VFD systems have particular sensitivities that need not be considered when operating a simple ac motor, cabling choices will change. Questions to ask when choosing a VFD cable include:
- How does one minimize the effects of impedance mismatch between the cable and the motor?
- Is the cable properly matched to the drive and motor voltage and current requirements?
- Does the application require a design that is easy to seal as it passes through connection glands?
- Are there instrumentation and communication applications close to the motor, drive, and cable that need to be protected from noise emissions?
- Is the cable of suitable gauge and structure to support the length of the cable run and still avoid possible energy surges that can damage motor bearings or windings?
There is no one right answer for all systems; however, there are a few important considerations that will help in decision making.
Start with the grounding: Proper grounding helps overcome problems due to impedance mismatches and overvoltages. In addition, it keeps common mode currents from other devices and systems.
An insulated ground conductor, terminated both at the motor and at the drive, is supported by the shield surrounding the circuit conductors, which is tied both physically and electrically to the insulated ground at the point where the cable enters the motor housing or drive enclosure. To prevent openings in the shield where electromagnetic energy might radiate out, a coupler (a mechanical fitting with male and female components) can be threaded into the motor or drive enclosure housing, with the cable end passing through it.
During assembly, the portion of the cable jacket that lies inside the fitting is removed to expose the braid or the copper tape of the shield for mechanical contact. A conductive spring or gasket in the coupler touches both the housing and the shield in this exposed zone to complete the ground circuit.
A single ground wire with a large cross-sectional area of copper can provide low ground resistance from one end of the cable to the other to minimize ground loops and common mode current. However, if the gauge size is too small, there is a potential that energy can leak out and be conducted into adjacent instrumentation or communication circuits.
A “symmetrical design cable” uses three conductors for the ground. These are connected to the shield, so when they are terminated together at the ground lug on the motor case, the shield is automatically terminated.
Noise immunity: A properly shielded VFD cable can control noise whether it is from varying electric current or cable length. Belden’s research has concluded that shielding systems that include copper tape or combination foil/braid types provide a low impedance path for common-mode noise to return to the drive, and are therefore appropriate for VFDs. Foil shields alone are simply not robust enough to restrict the level of noise generated by VFDs.
Low dielectric constant: The dielectric constant is the property of the insulation that determines the amount of electrostatic energy that can be stored when a given voltage is applied. Low capacitance is necessary to eliminate voltage reflections from the motor back to the drive, thus the cable’s dielectric constant should have a low value.
For VFD applications, cross-linked polyethylene (XLPE) insulation’s low dielectric constant helps diminish noise and allows engineers to more closely match the impedance of the drive to the motor, ensuring a higher degree of energy efficiency and supporting longer cable runs.
Suppression of overvoltage: A thick XLPE insulation has a high impulse voltage breakdown rating that significantly reduces the risk of failure from reflected waves and voltage spikes, and offers lower cable capacitance. XLPE insulation has high temperature stability for VFD applications, as opposed to PVC, where localized melting of insulation may occur at higher temperatures.
Low risk of corona discharge: Thick XLPE insulation reduces the likelihood of either the cable or the motor voltage reaching its corona inception voltage or CIV (the point at which the air gap between two conductors in the cable, or between two windings on the motor, breaks down via electrical arcing). As opposed to PVC, XLPE insulation reacts to the high heat generated from corona discharge by forming a thermally isolating, charred layer on the surface of XLPE insulation in the cables, preventing further degradation.
Bonding: VFD cable requires a good connection between the shield and the ground conductors and the motor case or drive enclosure, and ultimately, to earth ground potential. Typically, bonding entails a mechanical connection involving a nut-and-bolt connection, though there are other possible methods. Appropriate bonding is needed to control the ground current and noise. The cable shield system should facilitate a simple, robust bonding connection.
Conclusion
When choosing VFD cabling, it is wise to balance the cost of failure down the road against the cost of doing it right the first time. Ask the right questions to ensure that the cabling solution matches the special needs of a VFD system.
Inadequate cabling could result in a ruined motor or drive, or both. Investing in the right VFD cables supports uptime and reliability of the VFD system as a whole, as well as protecting sensitive instrumentation and control systems adjacent to it.
Koditek is a product manager for industrial cables with Belden. Shuman is a senior product development engineer for Belden as well as a member of IEEE, BiCSi, ODVA, and TIA.