Asset and fleet management systems aid in optimizing fleet operations, assist in reducing maintenance costs and enhance equipment utilization through effective data utilization.
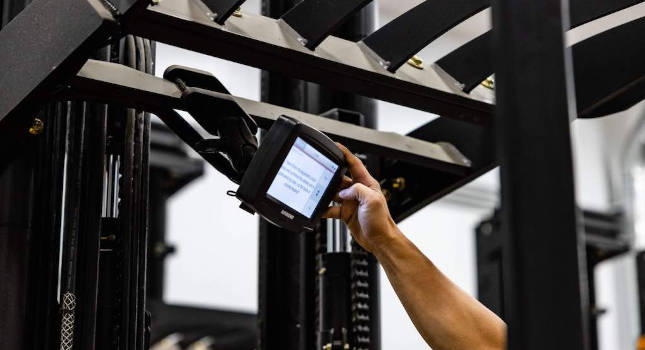
Learning Objectives
- Understand the difference between fleet and asset management systems.
- Learn how to get everyone on the same page in terms of objectives and priorities and developing a shared plan.
Fleet and asset management insights
- Fleet and asset management systems have been around a long time and offer many benefits for their users, which can now be augmented with data-driven systems.
- A data-driven approach allows companies to simplify operations, reduce safety incidents and effectively manage and monitor their workers and other resources.
In today’s evolving industrial landscape, asset and fleet management systems provide an accessible entry point into data acquisition. By offering valuable performance data, these systems aid in optimizing fleet operations, assist in reducing maintenance costs and enhance equipment utilization, making them a critical tool for optimizing productivity, profitability and equipment and asset utilization across a range of industries.
For businesses seeking to improve operational efficiency and maximize returns on investments, the seamless acquisition and integration of telematics-based data into these systems allows for real-time insights into fleet performance and equipment utilization. Thanks to powerful reporting functionality, facility managers and operators now have the opportunity to harness real-time actionable data, extract valuable trends and make informed decisions for their businesses.
The difference between asset and fleet management systems
For organizations ready to take their first steps into data acquisition through telematics, the choices — and even the language — can seem overwhelming, starting with the terms themselves: fleet management and asset management. After all, isn’t an equipment fleet technically an asset?
Yes and no. While some operations and suppliers use the terms interchangeably, asset management applications often allow for maintenance tracking and history, maintenance cost analytics, remote service dispatch, automated work order generation and more.
Fleet management applications may collect usage data on individual vehicles and operators, helping managers identify opportunities for improving productivity. Fleet management systems also may include features such as vehicle access control, location tracking, impact reporting or compliance checklists.
Whether the terms themselves are used separately or interchangeably, data is the critical deliverable of fleet and asset management systems. Collection of real-time machine and operator performance data enables advanced reporting, allows detailed, customizable analysis and facilitates effective, data-driven decision-making.
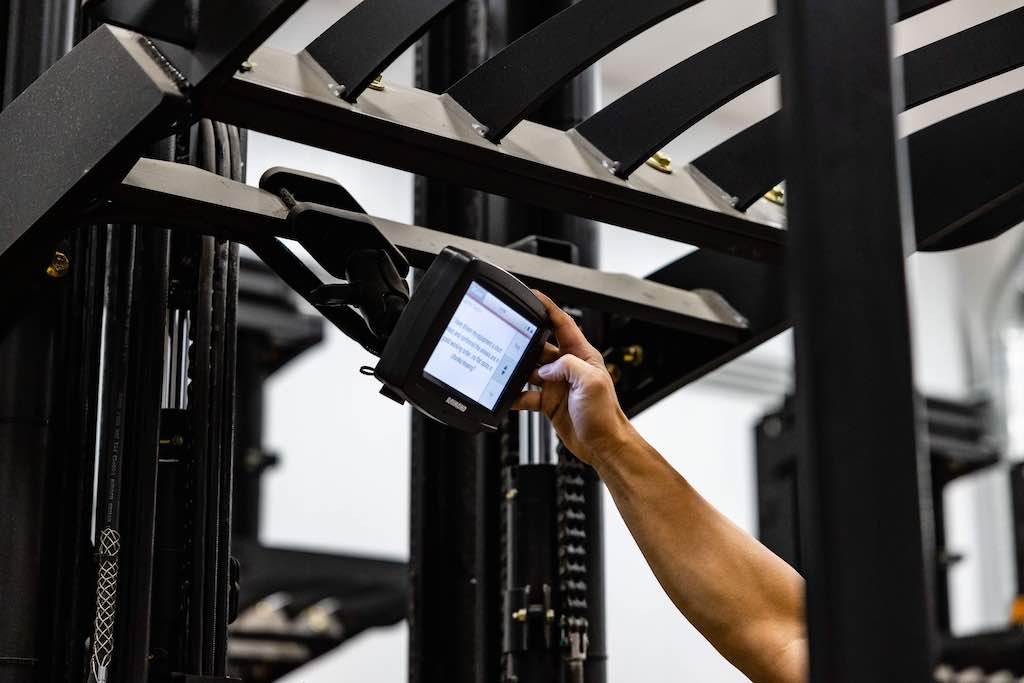
Using the material handling vehicle as a data source
The material handling vehicle is no longer just a lift truck. It is now seen as the operator’s cockpit — and the manager’s data source. A multitude of advanced technology options can be layered onto traditional base lift truck offerings, including tools to assist operator productivity and security and to provide facility managers actionable, data-driven insight into vehicle and operator performance.
Through continuous tracking and analysis of maintenance, service and material costs, managers gain a comprehensive understanding of operational trends. The integration of battery data — such as charging times, intervals and transit durations to charging stations — gives managers the visibility and granularity necessary to optimize equipment usage, minimize downtime and enhance productivity. In total, a comprehensive fleet management system can effectively monitor and optimize battery performance, decrease incidents, simplify asset maintenance management, optimize labor resources and deliver on key performance indicators (KPIs).
Making data the foundation for future functionality
In addition to helping managers identify opportunities for improvements in vehicle, operator and cost efficiency, the information gathered today will serve as the foundation for emerging and future technologies. Predictive analytics, for example, may require several years’ worth of performance data to function to its fullest potential.
The payoff, however, may easily justify the effort and cost by allowing facility operators to analyze different “If I optimize this, what happens to that?” scenarios. They also can determine whether a facility can take on additional workload with the existing fleet, labor and infrastructure; and to predict equipment maintenance or service requirements more accurately.
Three steps toward data acquisition effectiveness
The benefits of data acquisition may be clear, but the journey can be fraught; and while every operation is different, general guidelines can help keep things moving in the right direction.
First, engage with the information technology (IT) group as early as possible in the process. Even simple variables like the locations of Wi-Fi repeaters within a plant or warehouse can have significant impact on the functionality of a telematics-based system. Second, take data security seriously. A compromised data source could easily undo years’ worth of information-gathering efforts. Third, engage a reputable equipment and telematics supplier that will take the time to understand the business and operation.
A comprehensive telematics system is a critical component of any data-gathering initiative and can enable the insights necessary to visualize improvements and to optimize the organization to meet increased productivity and profitability demands.
By collecting data, businesses can drive productivity and continuous improvement across operations by:
-
Simplifying asset management and maintenance
-
Reducing incidents
-
Optimizing labor resources
-
Effectively managing and monitoring components such as batteries
-
Turning actionable data into results that reduce costs, improve efficiency and empower data-driven, future-proof decision-making.