The IIoT has helped to pave the way for Industrie 4.0, which refers to the next wave of the industrial revolution.
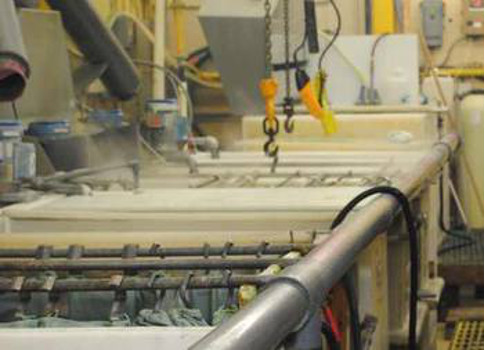
It is all about connectivity. Now more than ever the industrial plant model has become heavily reliant upon the connectivity possibilities between equipment and the automation that it can provide. The future digital plant revolves around the idea of connecting machines to work faster, more efficiently and in collaboration with one another.
There are a few new components of the digital plant that have helped to launch this new idea of an Industrial Internet of Things (IIoT) that encompasses where the future plant is headed. It is important to understand the Internet of Things (IoT) before looking at the way it is integrated into the industrial plant model.
Internet of Things
The Internet of Things (IoT) can be defined as the way that physical components are connected and networked together through the use of an Internet connection. The components that are connected together over the use of wired or wireless Internet connections are then able to utilize software that is specifically written for the products.
Typically, the IoT concerns consumer products like wearable technology and smart home devices. These devices are created with a distinct purpose in mind. For example, a "smart" thermostat is made and programmed with a purpose that has already been established by the manufacturer, and the consumer sees the need for the connectivity within his or her home. All of the programming has been completed with products that operate within the IoT, and it is done with the end consumer in mind. After these devices are purchased, there is nothing left for the consumer to do except install and power it. The IoT is focused on the convenience it provides consumers.
Machine-to-machine communication
The Industrial Internet of Things (IIoT) is focused heavily on improving plant efficiency and productivity. Machines that are connected together in the Industrial Internet of Things are able to collect large amounts of data and provide an analysis of the output so that changes can be made to ensure the machines are working more efficiently and are more easily monitored. While the primary driving point of the IoT is that it allows consumers to connect things, the IIoT allows plants to connect machinery in order to provide data that is more accurate and useful when optimizing system output. This is critical because adoption of the IIoT is becoming more readily available due to the affordability of processors and sensors that help to facilitate, capture and access information in real time.
Through the structured connectivity within the IIoT, machines are able to communicate with one another and even work together. For the last 20 years, automation manufacturers have had the ability to connect controllers to each other which effectively means machines are talking to each other. This concept of machines sharing information and working together is commonly referred to as Machine-to-Machine (M2M) communication. With M2M communication, sensors can be added to machines so that they are then able to send alerts when machines are not running optimally. For example, if a motor is taking more torque than it should, a connected M2M plant will be alerted to the issue and implement the proper protocol. Where the IoT typically connects machines to objects or people, the IIoT allows machines to communicate on a more precise and productive manner.
Benefits of the IIoT and M2M
The IIoT has provided the production business benefits that have not been previously available. One of the most prominent benefits that the Internet of Things provides is the ability to improve the efficiency of the plant production. The IIoT has improved operational efficiency through predictive maintenance.
Plants that had previously taken a less stringent maintenance schedule are now able to prevent large maintenance problems because the machines within the IIoT are connected and providing constant, real-time feedback on production. The more connectivity between machines that a plant implements, the more it will save thanks to scheduled and predictive maintenance-certainly as compared to a "run until it fails" maintenance model.
The IIoT has also changed the way that we look at information. The technology within plant manufacturing has not significantly changed, but the fact that the machines are able to connect with one another and provide larger amounts of data is where the IIoT and M2M allows the manufacturing world to make advancements. Companies are now able to take the large amounts of data that M2M communication provides and analyze it. After analyzing the data, engineers can make the necessary changes to the production line and machinery in order to optimize the efficiency and output of the system as a whole.
Another benefit with the IIoT is that the machines involved in the production process do not come with a preprogrammed set of instructions or software. This allows engineers to take the components of the plant and program them to the individual needs of the plant. The effort that needs to go into the installation and programming of the systems may be more than that of the components that fall within the consumer IoT, but the final product that the IIoT provides is significantly more precise and customized to the end user (e.g., the manufacturing plant).
Looking ahead
The IIoT has helped to pave the way for Industrie 4.0, which refers to the next wave of the industrial revolution. Industrie 4.0 has allowed companies to conceptualize and even implement systems that are then used in a factory that is completely run through connectivity and considered to be "lights out".
Industrie 4.0 is where automation and industrial trends are headed. By adding sensors to specific areas of already highly connected factories, the information is available in real-time and also, in some instances, self-correcting. There are a handful of companies that have implemented these strategies and seen the benefits of a lights-out factory, but the concept is far from perfected. Companies are investing heavily in research that will indicate how to make lights-out factories more accessible and affordable.
While there are not many lights-out factories currently in operation, the IoT will allow for further research to be done and advancements to be made towards creating factories that will optimize the connectivity options that are available.
-Corey Foster is application engineering manager for Valin Corporation.