Connectivity improvements are poised to transform manufacturing
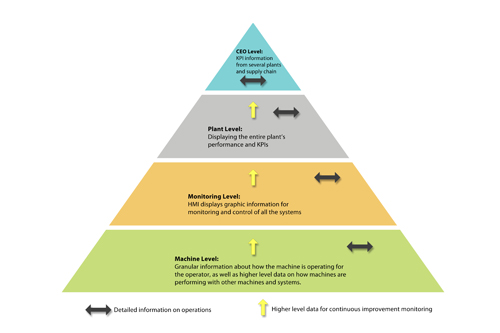
There is much speculation about how the Internet of Things (IoT) will usher in the next phase of automation. Proponents say it promises greatly increased productivity while lowering costs, but some plant managers and IT professionals are skeptical of the costs required to build smart systems and meet security requirements.
The good news is that many IoT implementations can be accomplished with the smart devices and advanced HMI already operating in many plants. Furthermore, the price of smart sensors and the networks that connect them to plant automation systems and the larger enterprise are rapidly decreasing, easing the way for new projects and modifications to existing systems.
While advanced machine-to-machine (M2M) communications and IoT may seem far off, these concepts are poised to change the face of manufacturing as much, if not more, than the introduction of networking and the Internet.
Automation systems are exceptionally good at gathering huge amounts of data, but this data isn’t usually extrapolated as context-based information and used to maximize productivity.
Today, affordable technologies exist to transform raw data into actionable information for a person in an office making a production decision, an operator reviewing trends, or an executive who needs marketing information. In advanced M2M and IoT implementations, machines and components can even automatically respond to data exchanged among them, resulting in increased uptime and productivity without unduly burdening plant operations personnel.
What is the Internet of Things?
The ARC Advisory Group defines the industrial IoT as "connecting intelligent physical entities, such as sensors, devices, machines, assets, and products, to each other, to Internet services, and to applications." It’s a concept that focuses on collaboration between machines, processes, and humans.
All plants generate huge amounts of data, but storing and analyzing it to make informed decisions has been a challenge. Fortunately, there are visualization and analytic tools available, and many manufacturers already have these functionalities in their advanced HMI but aren’t using them to the optimum extent. These tools are the foundation of proactive maintenance, logistics. and forecasting.
IoT-connected systems are expected to further optimize processes, increase efficiencies, and reduce expenditures. At a recent keynote address, Cisco CEO John Chambers predicted IoT can help manufacturers generate $3.88 trillion of value through higher revenues and lower costs over the next several years.
Of course, Cisco and other vendors aren’t disinterested observers, as any concept that involves networking is one that should be promoted in their eyes. Things look different from the manufacturer’s point of view, where investments can’t be made unless improvements will result.
Tangible benefits
One of the biggest advantages to an IoT system is the ability to see data in easy-to-understand views. Operators can view trend data on a particular machine to improve its performance. The same machine can also send data to the enterprise network. This data can be filtered and displayed on an OEE dashboard, helping plant managers get a clear picture of overall operations, and executives to interpret data sent from multiple plants for production forecasting. Presenting data in this and other related ways ensures that everyone sees the appropriate information without meaningless data overload.
In addition to helping people better use data, advanced M2M and IoT enable devices to interact with information from another device without the need for human interaction. This type of self-organized operation minimizes the lost time and materials that can result from unexpected changes in production (Figure 1).
For example, a bottleneck occurs at one part in the production line. The PLC sends data to conveyors farther down the line belt that a problem has occurred. The conveyors slow down but don’t stop, and automatically return to normal speed once the upstream problem is resolved. This type of machine-to-machine interaction may eventually lead to proactive maintenance that will extend the life of equipment, cut maintenance costs, and reduce downtime.
If a sensor detects a slight change in vibration on a machine, a deviance not large enough to trigger an alarm. An asset management and condition monitoring system connected to the sensor through an IoT network detects the change and sends an alert to maintenance so that the problem can be addressed before it causes equipment damage and downtime.
Condition-based monitoring has been appealing to plant managers and decision makers for some time; it just hasn’t been implemented by most manufacturers. Some are concerned about the cost of creating the associated IoT network. Fortunately, a good portion of industrial IoT architecture builds upon current installed technologies such as intelligent devices and digital networks, and other parts of the architecture can often be added at reasonable costs.
Difference between M2M and IoT
In some ways IoT resembles the more familiar M2M technology in which devices exchange information with each other. IoT is often associated with M2M communication in manufacturing, utilities, and logistics-but there are key differences between the two (Table 1). Most machines and processes have sensors, but they’re often only used to feed information to the PLC or controller, and are therefore functioning as silos and not connected to the larger operational and enterprise systems. M2M also typically involves a closed, hardwired network environment, which makes transmitting data to a larger enterprise network very difficult and expensive.
Unlike traditional M2M that relies on point-to-point communication, IoT systems provide data communication at the machine level as well as communications with business systems. IoT does this by using Ethernet and its standardized, open Internet Protocol network structure instead of the proprietary architectures found in many M2M communications.
Ethernet is a game changer for IoT because it allows multiple protocols to work simultaneously on the same network. So, a sensor with an Ethernet port can send data to a local controller, and also to higher level software platforms such as an HMI and an asset management system.
The use of standardized protocols at both the machine and enterprise level also enables easier remote access from a wide variety of devices, such as smartphones and tablets. This facilitates communication by streamlining it among machines that may come from different vendors.
The integration of device and sensor data with larger networks is the core of IoT as it provides the ability to view granular data at the machine level, as well as big data with analytics tools at the system or enterprise level.
Another important difference between M2M and IoT involves scalability. Traditional M2M systems have been hardware focused with proprietary architectures. IoT, on the other hand, is software centered, which eliminates the need for incremental, hardwired installations. Once the Ethernet network is in place, new devices can be easily integrated, and data can be transmitted and stored to large databases or even the cloud.
The emphasis on software in IoT brings fiscal advantages to companies. Software is much easier to install and access as compared to making changes at the hardware level, and it typically carries a much lower purchase price than hardware. Moreover, HMI software at the embedded level has become almost as sophisticated as PC-based SCADA software, and often uses the same protocols to enable easy networking.
How to implement IoT
Today’s smart automation environments use a standardized IP-centric network, enabling all devices to communicate at both the operational and enterprise level by leveraging open protocols. This allows companies to more easily capture, analyze, and create value from data. Moving to an IoT structure does require some investment for most businesses, but the advanced capabilities of IoT promise to transform manufacturing. Therefore, early adopters stand to gain a competitive advantage over their laggard competitors.
A huge installed base of legacy equipment and standards poses a challenge for many companies to develop an IoT network. Fortunately, high-volume semiconductor manufacturing resulting from consumer electronics demand has lowered the cost of IP-enabled sensors and controllers. This has also created a dramatic increase in processing power and storage further up the networking and computing chain, which is necessary for IoT.
Other prevalent factors in the adoption of IoT include the use of Ethernet and wireless networks. Ethernet and IP are poised to become dominant across manufacturing. Many of today’s sensors, cameras, and RFID readers use the open-standard Internet Protocol. Network protocols also have been developed to support the demands of industrial environments.
For example, the Open DeviceNet Vendors Association is an international association that manages the Common Industrial Protocol (CIP) designed for use in process control and industrial automation applications.
CIP is an open communications protocol, media independent and supported by hundreds of vendors worldwide. It’s designed to support the interoperability of machines and devices common to a manufacturing plant while providing connectivity across the enterprise. Along with those technical capabilities, EtherNet/IP, which is part of CIP, provides hardened hardware, ruggedized cabling, and other industrial-strength equipment.
A single network architecture
IoT is most effectively applied within the confines of a single industrial Ethernet network, with lower level device-type networks either subsumed into Ethernet or connecting to it through protocol converters. A standard Ethernet network based on IP also streamlines collaboration with suppliers and customers, improving logistics. Using Ethernet as the dominant networking technology fits the IoT model, and also simplifies operations.
Multiple networks consume more physical space, and managing these networks requires more workers who need to be trained on each system. Moreover, many of the proprietary protocols used don’t provide the scalability and flexibility necessary for growth.
On the other hand, there are risks involved with an integrated single Ethernet network, from both cyber and physical attack. However, these risks can be diminished by employing a multi-layered defense strategy that encompasses everything from physical security to internal firewalls to ensure only authorized users access certain data. Furthermore, having a standard network across the entire enterprise can decrease inconsistencies.
Moreover, Ethernet-based security measures are already implemented by IT departments in many companies, affording manufacturing and logistics automation and networking professionals an opportunity to borrow and learn from existing security practices.
IoT promises many advantages to manufacturers. The ability to view and analyze big data will help manufacturers optimize efficiency and cut costs. At lower levels, operators can improve plant performance, and maintenance teams can work proactively and more effectively.
Deploying a single, all-encompassing Ethernet network will improve data flow and lower maintenance expenses. Using an open protocol, such as IP, will help manufacturers offer more visibility to their suppliers and customers.
While IoT brings challenges and often involves replacing outdated equipment in some cases, the benefits of greater efficiency, reduced downtime, and improved operations are compelling and will present a positive return on investment in many applications.
Marcia Gadbois is vice president of the InduSoft business unit for Invensys.