These 10 essential steps after receipt of an arc-flash-incident energy analysis will help enhance personnel and equipment protection, and help support compliance with NFPA and OSHA standards.
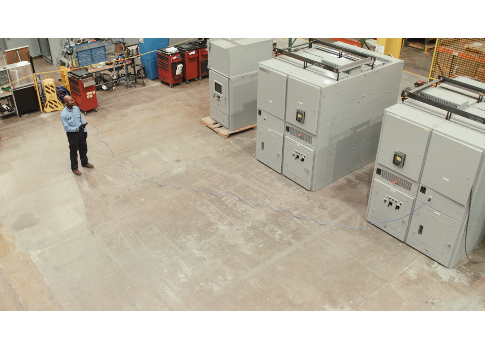
Plant Engineering will present a Webcast on October 22nd that will discuss changes in NFPA 70E for next year. To register for the Webcast, click the link HERE.
Increasingly, facilities across the country are engaging engineering firms to perform an Arc arc-flash-incident energy analysis for their electrical system, as outlined in the 2015 version of NFPA 70E, Standard for Electrical Safety in the Workplace. Per NFPA-70E-2015, an arc flash risk assessment is a "process that identifies hazards, estimates the potential severity of injury or damage to health, estimates the likelihood of occurrence of injury or damage to health, and determines if protective measures are required."
An arc-flash-incident energy analysis is the first step in this process that will quantify the incident energy that will be released during an arc flash event at each location in the electrical system. The results of the incident energy analysis are printed on an arc flash label for use by the qualified electrical worker to determine the appropriate personal protective equipment (PPE) to be worn while performing energized electrical work.
Establishing a culture that actively supports electrical safety involves more than an incident energy analysis. Avoiding the dangers associated with arc flash and shock hazards require conscious decisions and commitments by everyone, from the maintenance electricians and operators all the way up to environmental health and safety (EHS) and facility managers.
Following these 10 essential steps after receipt of an arc-flash-incident energy analysis will help enhance personnel and equipment protection, and help support compliance with NFPA and OSHA standards.
Step 1: Read the Report.
The executive summary will describe the major action items associated with the analysis. In addition to recommendations pertaining to arc flash, the executive summary also will have details regarding over-dutied equipment and recommendations for protective device settings.
Step 2: Evaluate Safe Work Practices.
Energized work should be the last choice when it is not feasible to de-energize the work location due to equipment design or operation limitations. When energized work is necessary, there should be a specific safe work procedure in accordance with OSHA CFR 1910 Subpart R or Subpart S and NFPA-70E-2015.
Step 3: Determine Qualified Employees.
Per OSHA regulations, it is the employer’s responsibility to determine not only who is qualified to work on energized electrical equipment, but also to outline the qualifications.
Step 4: Determine Acceptable Hazard Levels.
The arc-flash-incident energy analysis report may identify locations with a high arc-flash-incident energy level. In some cases, it is not feasible to mitigate the arc flash hazard at all equipment locations in the facility. Prioritize by reviewing operational goals and identifying locations where interactions with the equipment are frequent and prolonged.
Step 5: Implement Recommendations.
Work with your power-system engineer to develop a plan to mitigate the hazards identified in "Step 4." Also, implement recommendations for over-dutied equipment and protective device settings that may have been identified in the report.
Step 6: Train Personnel.
Invest in appropriate training for electricians, maintenance personnel, site safety teams, and facilities management teams. All of the results and recommendations in the report could be wasted if no one understands how to use PPE correctly or read an arc flash label. The training should assist site personnel with answering the following questions:
- Who is qualified to work on electrical equipment?
- Is my day-to-day operation going to be affected by our renewed focus on electrical safety?
- What do I need to do to ensure my team is working safely?
Step 7: Apply Arc-Flash-Hazard Warning Labels.
Per NFPA-70E, electrical equipment that is likely to require examination, adjustment, servicing, or maintenance while energized shall be field-marked with a label containing: (1) the nominal system voltage, (2) the calculated arc flash boundary, and (3) the available incident energy and working distance as calculated by the arc-flash-incident energy analysis.
Step 8: Order PPE.
In the 2015 edition of NFPA-70E, there are no standard PPE categories based on calculated incident energy. In development of the electrical safety policy, a PPE system needs to be implemented based on the incident energies calculated. Table H.3(b) in NFPA-70E offers guidelines for selection of arc-rated clothing and other PPE when incident energy exposure is determined.
Step 9: Verify Electrical Equipment is Properly Maintained.
NFPA 70E-2015 sections 205.3 and 205.4 require that electrical equipment is properly maintained and documented in accordance with the manufacturer’s instructions and applicable codes and standards. The electrical equipment owner, or their designated representative, is responsible for maintenance and documentation (205.3). NFPA 70E-2015 130.5(3) states that "condition of maintenance" must be considered for the overcurrent-protection device used in the arc flash risk assessment. Improper or lack of maintenance of an overcurrent-protection device can lead to an increased operating time, which could result in higher arc-flash-incident energy than the values determined by an arc-flash-incident energy analysis. If the incident energy for an actual arc flash event is higher than the incident energy calculated by the arc-flash-incident energy analysis, the electrical worker may not be wearing sufficient PPE.
Step 10: Manage the Performance of Equipment and Safety Policies.
A culture of continuous improvement focuses on removing stagnation and implementing evolving processes and procedures. Use this opportunity to ensure that equipment continuously operates at peak performances, and to ensure safety policies and procedures are updated and reviewed on a regular basis.
An incident energy analysis is a critical part of an overall risk assessment. Although the analysis provides important information for personnel and helps comply with the NFPA 70E standard, it does not estimate the risk associated with the work being performed. The risk associated with performing energized electrical work will vary based on the work being performed, condition of the equipment, and many other factors that are best determined by a qualified worker. Facility managers and qualified personnel need to take the next steps and determine the protective measures that are required and support a workplace culture that actively supports electrical safety.
Scott Brady, PE, is Eaton’s Western region manager for the technical application support team. Garrett Hamilton-Smith, PEng, is a power-systems engineer at Eaton. Nick Jackson, PE, is district operations manager at Eaton. Adam Reeves is a power-systems engineer at Eaton.