Facilities that may have to deal with hurricanes should take necessary steps to ensure that employees are prepared and that the building can withstand the weather elements.
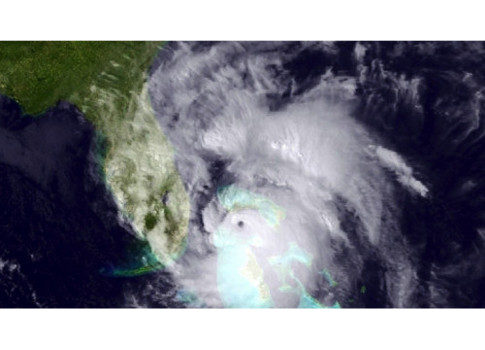
November marks the beginning of the end for the Atlantic hurricane season. The season officially runs from June 1 through November 30, and the East Coast has seen several major storms in 2016.
Thousands of people and businesses are still rebuilding from the effects of Hurricane Matthew. The major hurricane barreled up the southeastern coast of the U.S. in October 2016, leaving millions without power and billions of dollars in damage in its wake.
Even with warning systems and 24/7 access to weather tracking, hurricanes can be unpredictable.
Hurricane Matthew’s forecast track changed at the last minute as it approached northeast Florida. That shift of a few dozen miles can mean the difference between significant damage and catastrophic damage. This hurricane season may be coming to a close, but it’s never too early to prepare a facility for next year. It’s critical to establish an emergency plan to protect against these potential losses:
Flooding due to a tidal surge – the Federal Emergency Management Agency (FEMA) flood maps show areas vulnerable to tidal surges and flooding. Tidal surge flooding should also be factored into evacuation routes and timing.
Freshwater flooding from torrential rainfall – Again, the FEMA flood map can determine areas vulnerable to freshwater flooding. Just like with tidal surges, flooding due to rain should be factored into evacuation procedures.
Wind damage – High wind speeds can cause significant damage. A category 1 hurricane (the weakest category) has wind speeds of 74 to 95 mph while a category 5 hurricane (the strongest category) has wind speeds over 157 mph. Power outages are likely, due to downed power poles and blown transformers, and must be planned for accordingly.
Planning
The purpose of an emergency response plan is to protect one of the most important assets: employees. A thorough plan will include:
- An evacuation plan and route
- Provisions for data backup, as well as alternate communications and power
- A list of vendors and contractors to provide disaster recovery services.
Identify leaders with the authority and skills to direct others during an emergency. Emergency leaders should be high-performing employees who are confident and cross-trained among divisions. During a hurricane, they will execute evacuation plans and provide instructions.
Access to safety equipment is also critical, plan for the unexpected. The following questions should be asked:
- Can employees easily locate and access emergency equipment in the dark?
- Is that equipment accessible along evacuation routes?
- Does the supply include face shields, respirators, safety glasses, hard hats, earplugs, and personal protective equipment for each employee?
- Is the emergency equipment supply regularly audited to ensure personal protective equipment will be available when needed?
Industry groups and government regulatory agencies provide requirements and recommendations to follow in developing a plan. The Department of Labor’s OSHA Hurricane Preparedness and Response guide is an example. Equipment Chart out the following:
- Plant areas impacted by a power outage
- Processes that may be shut down if rooftop equipment is lost
- Key areas that should be protected from water damage
It’s important to appoint a response team who understands all plant’s systems and how those systems can be safely shut down in the event of a disaster. In case of a fire, how is ammonia or refrigeration systems secured to prevent a release? Who is responsible for safely engaging the system shutdown?
Ammonia releases
Ammonia systems are important to secure in the event of a hurricane, as an ammonia release could be very harmful. One standard operating procedure may include pumping down the system and ensuring it is secured. To verify all roof-mounted equipment is as structurally sound as it was when it was newly constructed, inspect elements including:
- Pipe stands
- Condensers
- Valve groups
- Roof penetrations
- Rooftop unit (RTU)
- Refrigerated makeup air unit (RMAU)
Most insurance companies have a detailed hurricane preparedness manual. Carriers should be asked to provide one if it is not available. This can serve as a template to develop a facility-specific checklist for implementation.
Emergency Response
Facilities damaged by high winds, exposure to water, and/or debris are very dangerous sites. Often, people want to rush into the remains to help those who may be in danger. However, it is important to assess the damage before initiating rescue efforts. Not doing so can cause even further damage or injury.
Before sending in the cleanup crew, stop and answer the following to determine the building’s structural integrity:
- What’s required to stabilize the structure?
- How should access be restricted to dangerous parts of the plant?
- How should demolition be constructed without causing further damage to the facility?
- Are there gas leaks?
- Has power been shut down and electrical hazards evaluated prior to exposing personnel to possible electrical dangers?
If there is significant structural damage, bracing walls and shoring floors will help stabilize a facility’s structure. These are highly technical processes and should be handled by experienced professionals. Otherwise, personnel can be exposed to a hazardous situation.
Many companies offer bracing and shoring services, however, they may not be experienced in the techniques for emergency situations. For a facility’s safety, structural engineers should be enlisted with experience in bracing and shoring following disasters. Good planning and security and emergency preparedness plans are critical and should be in place so facilities can be ready for any storm that may come.
-Johnny Johnson is the vice president of field services at Stellar. This article originally appeared on Stellar Food for Thought. Stellar is a CFE Media content partner.