Alex West is a principal analyst for the Manufacturing Technology Group at IHS. Based in London, he’s responsible for IHS’s coverage on smart manufacturing and industrial communications and oversees research on a range of transformational manufacturing technologies including the Industrial Internet of Things. He discusses the global outlook for manufacturing and its impact on the United States with CFE Media:
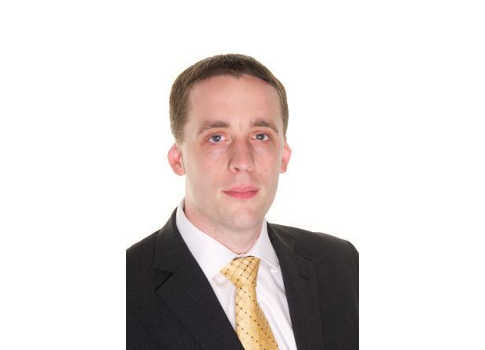
Alex West is a principal analyst for the Manufacturing Technology Group at IHS. Based in London, he’s responsible for IHS’s coverage on smart manufacturing and industrial communications and oversees research on a range of transformational manufacturing technologies including the Industrial Internet of Things. He discusses the global outlook for manufacturing and its impact on the United States with CFE Media:
CFE Media: What’s your overall outlook for 2016? What will be the key issues affecting manufacturing as we begin the New Year?
West: Headwinds will continue to buffet most industries, resulting in a challenging 2016. Many companies will be concentrating on survival rather than expansion. The dominant themes of a struggling Chinese economy and depressed commodity industries that dogged the second half of last year will continue to be at the forefront in this.
In 2015, several major currencies weakened notably against the dollar; they included the Yen and the Euro, by over 10% and 15% respectively. In 2016, the reduction in the cost of imports to, and the increase in the cost of exports from, the United States, will be exacerbated should the Federal Reserve continue to raise interest rates in 2016, as they intend. There is also the potential for Chinese RMB depreciation further reducing U.S. competitiveness in exports, and damaging countries in both Europe and North America. Competitive devaluation would be generally disruptive and damaging.
Conditions are also ripe for new mergers and acquisitions, especially in commodity-related industries, where companies with strong balance sheets will benefit from discounted acquisitions of struggling competitors.
CFE Media: Manufacturing was in a slump at the end of 2015. What are the driving factors for manufacturing going forward that will pull out of that slump?
West: As mentioned, 2016 is forecast to be another difficult year, and there are no simple remedies. This year many, manufacturing companies that can, will reduce their exposure to more volatile and depressed markets and spread their focus on others, such as water, and food and beverage. However, other than technologies with growing underlying demand, like robotics, there are no specific industrial sectors that are expected to outperform.
Although industries related to commodity markets will struggle with continued reductions in capital expenditure through 2016, the cutbacks have been so severe that significant reinvestment will be needed to meet long-term commodity demand, as the market bounces back, currently predicted for 2017. However, the recovery in the manufacturing sector will be more gradual, as many regions will feel the effects of both China’s slowing growth, and its slow transition to a more developed, service-based economy.
Although 2016 will be a difficult year, the silver lining is the resulting increased focus that industry will place on improving efficiency and reducing costs. This will help companies to emerge from this contraction as leaner, more balanced and productive organizations.
CFE Media: Everyone is hearing about the Industrial Internet of Things. Why should IIoT be important to manufacturers?
West: The evolution of IIoT is set to change not just manufacturing processes, but also the competitive landscape itself.
Although many of the technologies have been available for some years, to varying degrees, it’s the confluence of factors such as greater plant connectivity, closer integration between factory and the enterprise, and improvements in data recording and analysis, that is bringing us to this shift in manufacturing.
Allowing manufacturers to mass produce customized products; or adjusting manufacturing real time, based on demand; or minimizing costs through better visibility of the supply chain and energy consumption; the IIoT concept will revitalize flagging productivity growth rates. To facilitate IIoT, a variety of new types of companies are entering the industrial market including suppliers of Ethernet infrastructure components, telco’s, companies offering cloud based services, as well as a range of new software companies. As there are no companies able to offer all products and services, partnerships will be critical.
Manufacturers will also have to look closely at how these new technologies and manufacturing modes are implemented. Especially in the difficult conditions mentioned earlier, companies that are able to evolve, integrating these new techniques, will be well placed as the market recovers. Conversely there is a strong likelihood that some manufacturers will fall by the wayside as they fail to adapt.
CFE Media: We talk a lot about IIoT, globalization, safety and productivity. What’s the one big issue that you think manufacturers should talk about that doesn’t get a lot of attention?
West: One area manufacturers will need to monitor closely is training. With a large proportion of the engineering workforce approaching retirement over the next decade, and difficulties in getting students to focus on engineering degrees, there is a serious threat of a skills shortage in much of the developed world. Part of the challenge is the need to ensure existing skills and expertise are transferred to the next generation of engineers. However, this is only a part of the problem.
Companies must also change how they manufacture to remain competitive. The more difficult task may be training and convincing experienced engineers to standardize on new workflows and techniques, from collaboration between the IT and OT departments to the implementation of new maintenance schedules based on asset monitoring.
Click here to read this story in the digital edition.